In the search for the most cost-effective materials in the building, construction, and infrastructure sectors, the fire, smoke, and toxicity (FST) properties of materials are often considered too late. Here, Eric Moussiaux, VP technology at Exel Composites, explains why it’s important to understand the standards, select the right tests, and choose composites that deliver the best FST performance.
Whether it’s windows, doors or curtain-wall profiles, interior or exterior cladding, or even railway cable trays, the fire, smoke and toxicity properties of materials should be considered early in the journey of any new project. Fail to do this and by the time you come to consider the FST properties, you’ll already be on the backfoot, potentially having to overspend to acquire a material that meets all your needs. In extreme cases, not considering the FST properties of a material early on could result in businesses having to discard or offload materials they’ve already purchased or make costly adjustments to tooling investments.
Fragmented standards
Part of the problem stems from the historic discrepancy in fire standards across Europe, which weren’t unified until about two decades ago. Whether it was Germany’s Musterbauordnung (national model building code), France’s safety commissions, Spain’s onus on local authorities, or the UK’s devolved enforcement, there was little harmony in fire safety. Some of these rules were prescriptive — requiring structures to meet specific fire tests — others were based on performance testing, where the regulation only set out how a building or structure is expected to perform, not how it should be designed. Ultimately, it was clear that fragmentation was creating trade barriers, and hampering business.
A harmonized standard
In 2000, the European Union introduced the Euroclass system, or EN13501-1. This system classifies the reaction to fire of construction and building materials, based on three main factors: combustibility, smoke production and the production of flaming droplets or particles. Combustibility achieves a classification from A1-F with A1 being the least combustible; smoke production ranges from S1 to S3, with S1 producing the least smoke emissions; and flaming droplet production ranges from D0 to D2, with D0 demonstrating no dripping.
So, for example a material classified as B-s2,d0 would be one with limited combustibility, that produces smoke at a quantity and speed that is of an average intensity, and produces no flaming droplets during combustion.
Standard tests
However, the use of defined tests can be a limiting factor. In a recent project, Exel Composites worked with a customer in Germany to develop a composite cable-tray for use on embankments at the side of German railroad tracks. Hot summers can cause the desiccated grass to catch fire from sparks generated by the brakes of a passing train. The resulting bush fire can expose the underside of the elevated cable trays to fire, so it’s essential that the tray can continue to protect the cables inside it.
There is a danger that choosing a simple, well-known test in such specifications, can be less relevant to the real-world application and add unnecessary difficulty. One such test is the UL 94 vertical test in which a small sample — 25 mm wide by 100 mm in length — is lit at the bottom with a 20 mm flame. Picture it like holding a matchstick from the top and lighting it from the bottom; the flame will quickly reach and burn your fingers.
In this scenario, the specified bushfire test is much more appropriate. Here, a normalized quantity of hay is lit under the tray. The tray must then withstand the fire until it stops, without causing structural damage or allowing the internal temperature to rise high enough to damage the cables inside. The difference is that one material composition might fail the UL 94 test dramatically, while surviving the bushfire test with flying colors.
FST performance
As well as selecting appropriate FST tests, specifying engineers must ensure that the composites they choose are not hazardous to health. Many composites contain flame retardant additives, which reduce or delay the combustion process using substances such as aluminum trihydrate (ATH), which give off far less toxic smoke when burned compared to traditional halogenated additives. However, the associated filler material leaves less room for reinforcing fibers, which can affect structural performance. The answer is to work with a composites partner that understands the complex manufacturing and pultrusion techniques to produce composites that deliver both structural and FST performance.
The takeaway here for anyone working in the building, construction, or infrastructure sector is to consider FST requirements early, understand the standards, select the right tests, and choose composites that deliver consistent, high-quality results.
To find out more about composites for building, construction, and infrastructure applications, visit www.exelcomposites.com
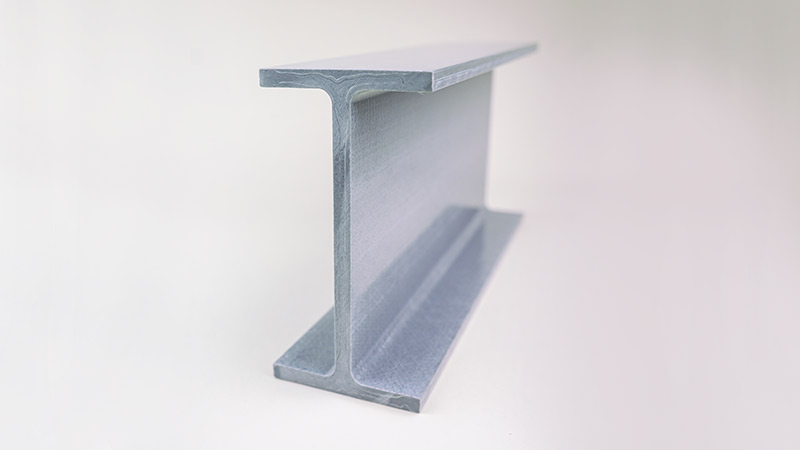
Building, Design and Construction Magazine | The Choice of Industry Professionals