With the current energy supply crisis and energy cost increases, coupled to our need to reduce emissions in line with net zero carbon there is an increased awareness of the importance of a properly and professionally insulated home.
Spray foam insulation is an important and effective method of improving the energy efficiency of our homes and buildings, but as with many construction improvements, installation must be done in accordance with all necessary approvals and relevant permissions.
Spray foam has been used successfully for more than 30 years in many countries from Canada to Spain (in very different weather environments). Many hundreds of thousands of properties continue to benefit from the application of spray foam, which is highly thermally efficient and extremely versatile. Once installed correctly spray foam will continue to perform as intended for the life of the building, without need for maintenance or servicing. But the need for correct installation cannot be over emphasised.
Spray foam must be installed in line with the manufacturers’ instructions and be carried out by a registered and professional spray foam installer. Unfortunately, there have been some occasions in the past where correct procedures have not always been followed and unscrupulous operators have been responsible for incorrect installation, poor workmanship and false claims relating to the use of spray foam.
Recent claims that any property with spray foam is unmortgageable are as untrue as they are unjustifiable which is why Insulation Manufacturers Association (IMA) along with spray foam manufacturers and installers, surveyors, valuers and lenders collaborated to develop an inspection protocol document for spray foam insulation. Inspection Protocol for building professionals who are asked to consider spray polyurethane foam that has been applied to the pitch. Alongside this collaborative protocol, IMA has also produced a Code of Practice for the Installation of Polyurethane Spray Foam (SPF) in domestic roofs which sets out the requirements for the procedures involved when specifying and installing spray foam products to the inside of roofs of domestic properties.
Whilst IMA does not represent installers or contractors of spray foam, it does represent some manufacturers and distributors of spray foam products. These manufacturers and distributors only ever supply to their approved contractors and we work with these suppliers to promote best practice and highlight the correct procedures for a spray foam installation. These procedures include pre-installation surveys and roof condition analysis, moisture risk analysis, product identification and supply information, as well as the post-installation home pack and these have all been incorporated into the code of practice.
All our members’ products are independently tested by UKAS accredited testing houses (either BBA or KIWA-BDA certification) and these products must always be installed in line with this certification.
The two new documents can be used to guide and inform building professionals, institutional bodies and trade organisations. The protocol provides a framework to assist property professionals and residential surveyors undertaking non-invasive visual inspections of spray foam applications to the inside of pitched roofs whilst the code of practice is designed to ensure that installers following all the necessary steps to ensure that spray foam is both specified and installed correctly.
Commenting Simon Storer, Chief Executive of Insulation Manufacturers Association said: “With government encouragement, many homeowners have done the right thing by investing in spray foam insulation improvements to their properties, but unfortunately, recent negative views have undermined the value of these insulation applications. Despite this, it should now be recognised that professional and accredited installations are as beneficial to a property as many other home improvements and should be considered as such.
These new publications provide excellent guidance and information about spray foam insulation, which we expect industry professionals to adopt and understand, so as to bring peace of mind to the thousands of homeowners whose applications are in line with third party approval and accreditation.”
To download and view the guidance click the following Code of Practice for the Installation of Polyurethane Spray Foam (SPF) in domestic roofs and Inspection Protocol for building professionals who are asked to consider spray polyurethane foam that has been applied to the pitched elevations of domestic roofs.
For more information about IMA visit www.insulationmanufacturers.org.uk
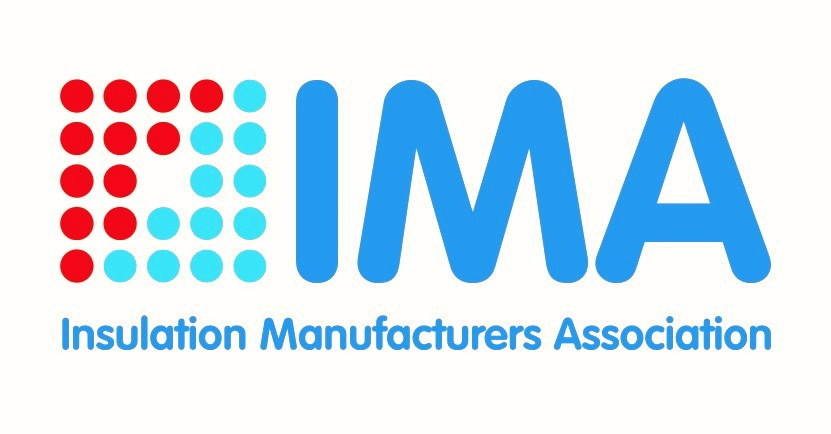
Building, Design & Construction Magazine | The Choice of Industry Professionals