By Dr Gareth Davies, Carbon Reduction Scientist, PhD & Dr Luan Ho, Carbon Reduction Scientist, PhD – Tunley Environmental
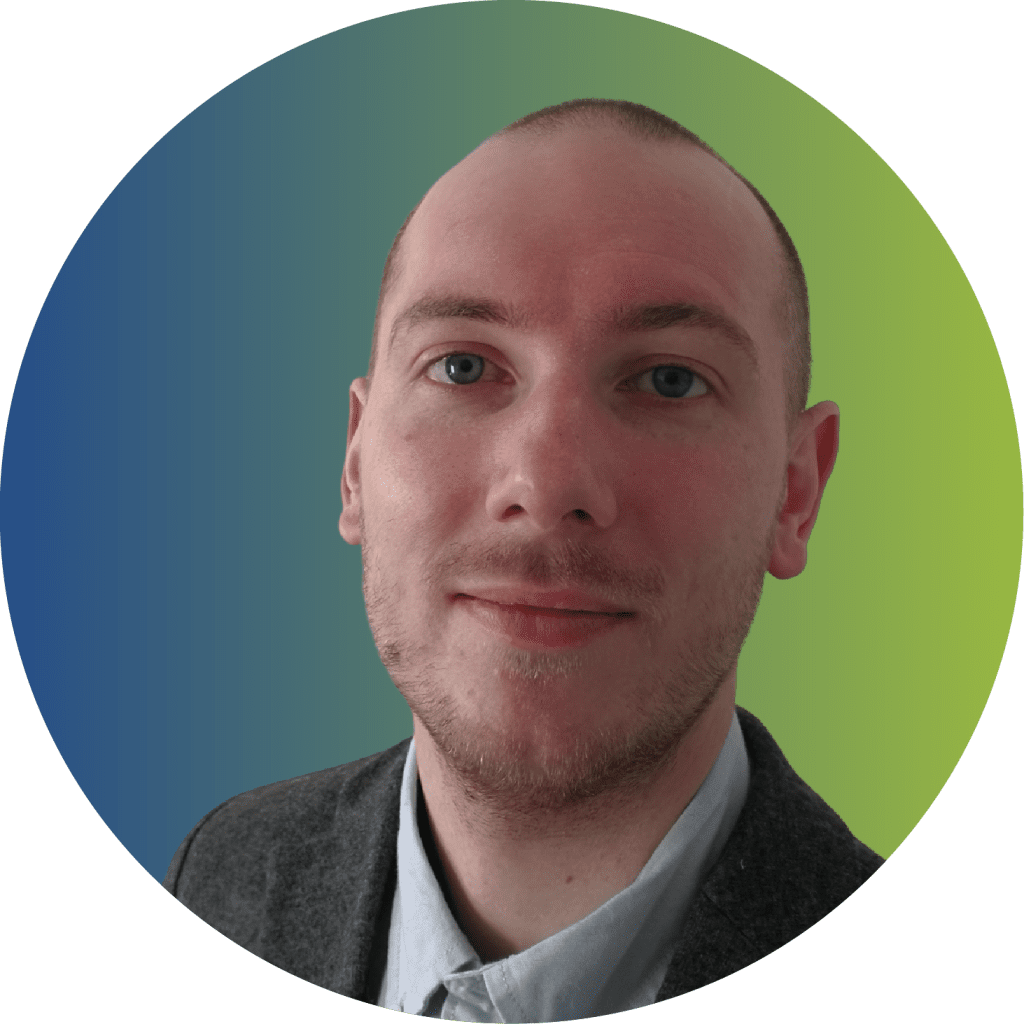
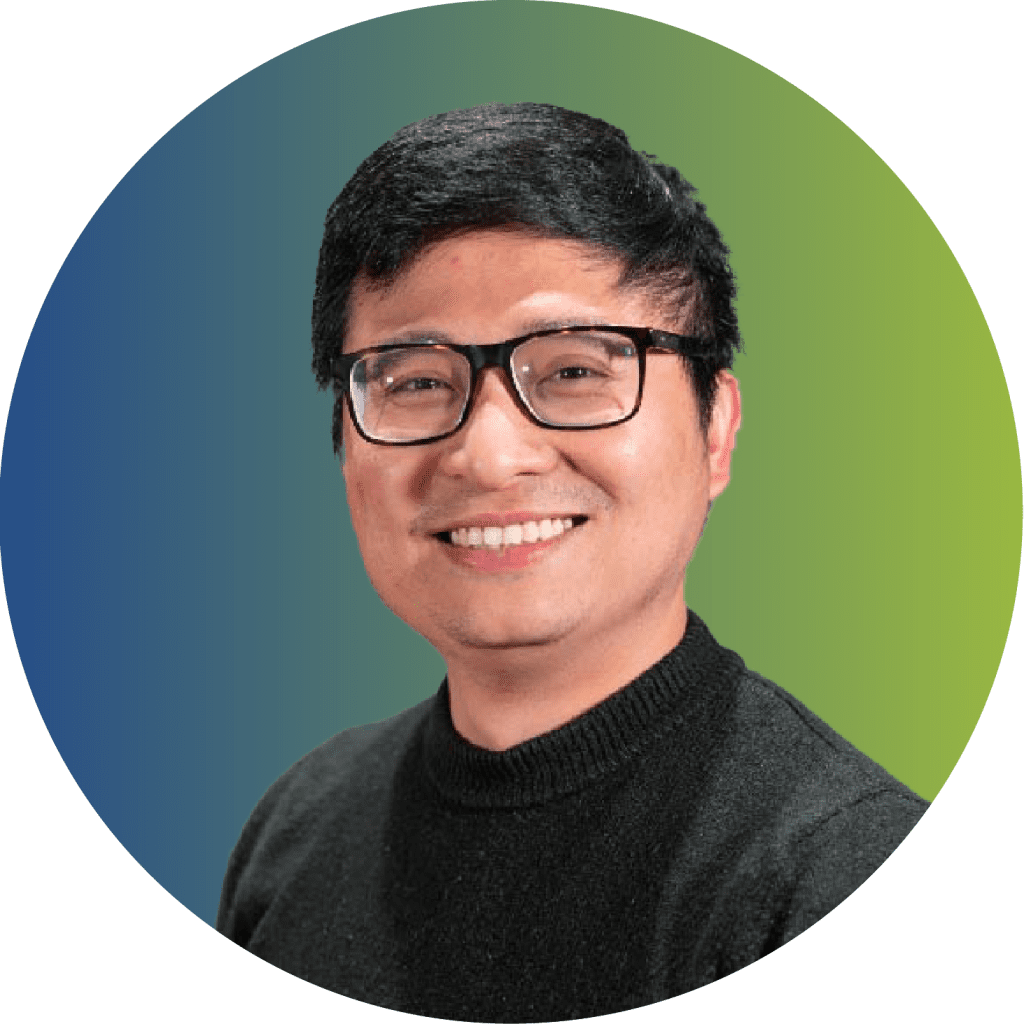
Concrete, the most extensively used manmade material worldwide, carries a significant environmental burden, contributing to 8% of anthropogenic GHG emissions. With a staggering 30 Gt produced annually, the material consumption is over 3.5 tonnes of concrete per person annually. The majority of the emissions (88.5%) emanate from cement production, the essential ingredient in concrete.
Carbon sequestration in concrete presents a promising avenue to offset these emissions. This process, often referred to as carbonation or mineralisation, essentially reverses the initial cement production steps, where carbon dioxide is detached from calcium carbonate (limestone). Controlled carbonation of cementitious material, although first proposed in the 1970s, is recently garnering increased attention due to its substantial potential to mitigate against the colossal emissions from concrete production.
However, carbonation is not without its challenges. Uncontrolled, it can lead to the corrosion of steel in reinforced concrete and the formation of harmful compounds, jeopardising the structural integrity of buildings. Yet, advancements in controlled carbonation methodologies have demonstrated the potential to not only sequester carbon dioxide but also enhance the properties of concrete.
One such method involves utilising accelerated carbonation chambers to carbonate pre-cast materials, offering control over essential parameters such as CO2 concentration, humidity, and temperature. This impacts the rate and depth of carbonation, with the formation of calcium carbonate in the exterior pores blocking further carbonation.
Emerging techniques explore embedding CO2-rich materials within the concrete mixture. A notable investigation by MIT researchers examined incorporating sodium bicarbonate, which dissolves and releases CO2 during curing. This innovative method not only sequesters carbon but also addresses the detrimental impacts of late-stage carbonation, such as shrinkage and crack formation.
Furthermore, the possibility of reusing carbonated Recycled Concrete Aggregate (RCA) from construction and demolition waste, which amounts to around 3 billion tonnes annually, offers an additional layer of environmental benefits. Although using RCA poses challenges such as increased costs and micro-cracking, controlled carbonation mitigates these issues and allows for a decrease in both water absorption and leaching instability.
These advances in carbonation technology could potentially sequester 2 Gt of CO2 annually if implemented at scale, significantly reducing the environmental footprint of concrete production. When combined with the predicted 50% reduction from electrification, emissions could be curtailed to just 32.7% of the current levels.
However, the journey towards sustainable concrete production is multifaceted and complex. As researchers and engineers continue to explore the potential of carbon sequestration in concrete, the combination of controlled carbonation and the incorporation of CO2-releasing materials represents a leap forward in our quest to mitigate the environmental impact of this ubiquitous material.
In conclusion, the path to mitigating the environmental challenges posed by concrete production lies in innovative solutions such as carbon sequestration. By acting as a carbon sink, concrete has the potential to offset a significant portion of the emissions generated during its manufacturing stage. The incorporation of carbonated end-of-life concrete as filler material further underscores the potential of this material to contribute to a more sustainable future.
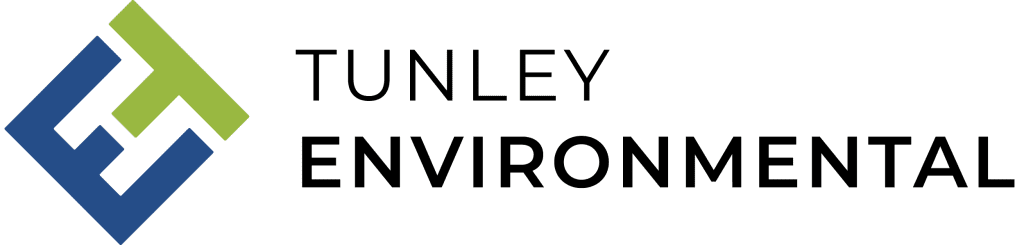
References
[1] S. A. Miller and F. C. Moore, “Climate and health damages from global concrete production,” Nat Clim Chang, vol. 10, no. 5, pp. 439–443, May 2020, doi: 10.1038/s41558-020-0733-0.
[2] A. Petek Gursel, E. Masanet, A. Horvath, and A. Stadel, “Life-cycle inventory analysis of concrete production: A critical review,” Cem Concr Compos, vol. 51, pp. 38–48, 2014, doi: 10.1016/j.cemconcomp.2014.03.005.
[3] P. C. Aïtcin, “Portland cement,” in Science and Technology of Concrete Admixtures, Elsevier Inc., 2016, pp. 27–51. doi: 10.1016/B978-0-08-100693-1.00003-5.
[4] M. Stefanoni, U. Angst, and B. Elsener, “Corrosion rate of carbon steel in carbonated concrete – A critical review,” Cement and Concrete Research, vol. 103. Elsevier Ltd, pp. 35–48, Jan. 01, 2018. doi: 10.1016/j.cemconres.2017.10.007.
[5] L. Qin, X. Gao, and T. Chen, “Influence of mineral admixtures on carbonation curing of cement paste,” Constr Build Mater, vol. 212, pp. 653–662, Jul. 2019, doi: 10.1016/j.conbuildmat.2019.04.033.
[6] S. Hussain, D. Bhunia, and S. B. Singh, “Comparative study of accelerated carbonation of plain cement and fly-ash concrete,” Journal of Building Engineering, vol. 10, pp. 26–31, Mar. 2017, doi: 10.1016/j.jobe.2017.02.001.
[7] B. Šavija and M. Luković, “Carbonation of cement paste: Understanding, challenges, and opportunities,” Construction and Building Materials, vol. 117. Elsevier Ltd, pp. 285–301, Aug. 01, 2016. doi: 10.1016/j.conbuildmat.2016.04.138.
[8] N. Lippiatt, T. C. Ling, and S. Y. Pan, “Towards carbon-neutral construction materials: Carbonation of cement-based materials and the future perspective,” Journal of Building Engineering, vol. 28. Elsevier Ltd, Mar. 01, 2020. doi: 10.1016/j.jobe.2019.101062.
[9] Z. Xu et al., “Effects of temperature, humidity and CO2 concentration on carbonation of cement-based materials: A review,” Construction and Building Materials, vol. 346. Elsevier Ltd, Sep. 05, 2022. doi: 10.1016/j.conbuildmat.2022.128399.
[10] J. Liu et al., “Carbonated concrete brick capturing carbon dioxide from cement kiln exhaust gas,” Case Studies in Construction Materials, vol. 17, Dec. 2022, doi: 10.1016/j.cscm.2022.e01474.
[11] Z. Li, Z. He, and X. Chen, “The performance of carbonation-cured concrete,” Materials, vol. 12, no. 22, Nov. 2019, doi: 10.3390/ma12223729.
[12] D. Stefaniuk, M. Hajduczek, J. C. Weaver, F. J. Ulm, and A. Masic, “Cementing CO2 into C-S-H: A step toward concrete carbon neutrality,” PNAS Nexus, vol. 2, no. 3, Mar. 2023, doi: 10.1093/pnasnexus/pgad052.
[13] Y. Pu et al., “Accelerated carbonation technology for enhanced treatment of recycled concrete aggregates: A state-of-the-art review,” Constr Build Mater, vol. 282, May 2021, doi: 10.1016/j.conbuildmat.2021.122671.
[14] D. Xuan, B. Zhan, and C. S. Poon, “Assessment of mechanical properties of concrete incorporating carbonated recycled concrete aggregates,” Cem Concr Compos, vol. 65, pp. 67–74, Jan. 2016, doi: 10.1016/j.cemconcomp.2015.10.018.
[15] T. Kikuchi and Y. Kuroda, “Carbon Dioxide Uptake in Demolished and Crushed Concrete,” 2011.
[16] Z. Guo, A. Tu, C. Chen, and D. E. Lehman, “Mechanical properties, durability, and life-cycle assessment of concrete building blocks incorporating recycled concrete aggregates,” J Clean Prod, vol. 199, pp. 136–149, Oct. 2018, doi: 10.1016/j.jclepro.2018.07.069.
https://www.tunley-environmental.com/
Building, Design & Construction Magazine | The Choice of Industry Professionals