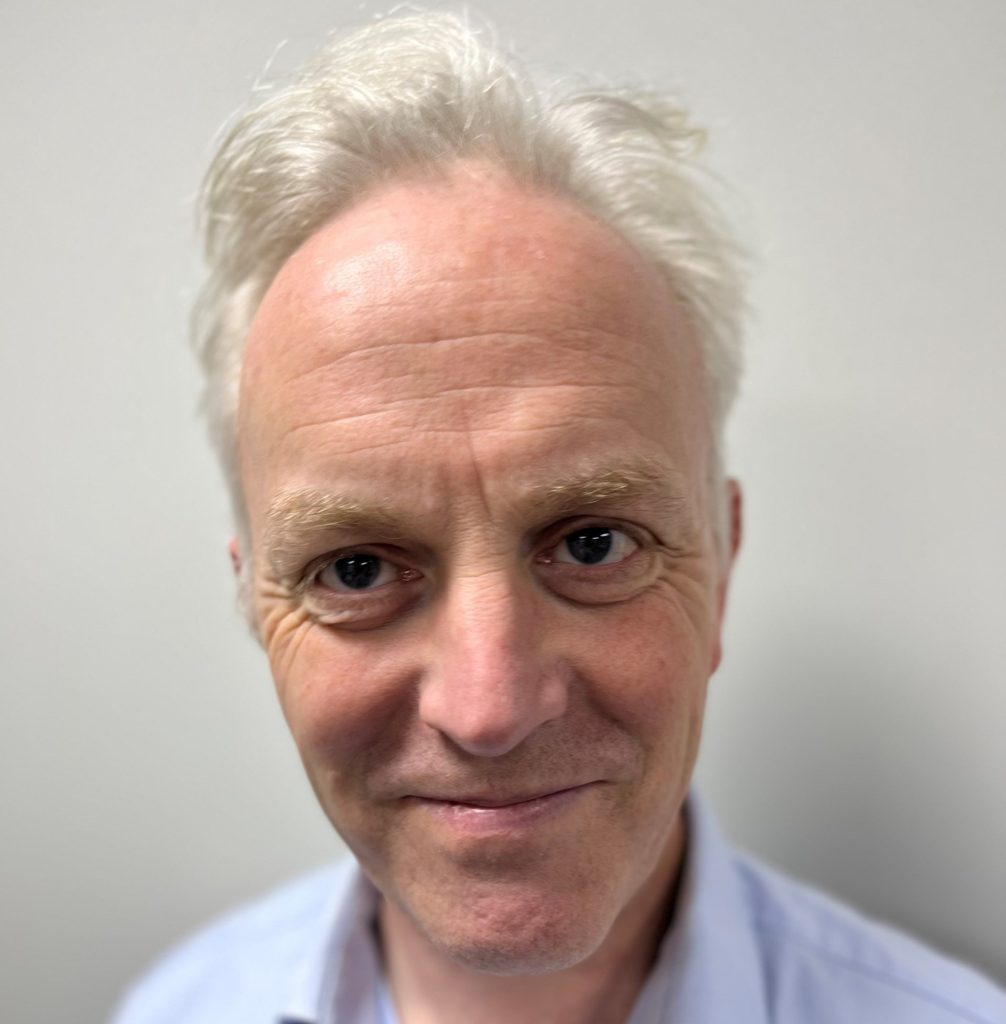
Panics come and panics go in the pragmatic world of engineering. It is part of the job to identify potentially intractable problems – and then bend the collective mind to creating a practical solution to them.
That is why the current disquiet over RAAC in a number of public buildings throughout the UK needs to be kept in perspective. If you subsisted only on a diet of mainstream media, you could be forgiven for thinking the entire built estate was on the point of imminent collapse.
For clarity, this is not the case. Yes, RAAC – Reinforced Autoclaved Aerated Concrete – exists in a number of buildings, but the number is small in comparison to the totality of schools (more than 20,000 in England), hospitals and other public buildings, and most closures are precautionary, rather than evidence-based.
But first of all, what is RAAC? It is an aerated lightweight cementitious material with no coarse aggregate, looking in cross-section a bit like the inside of an Aero bar. When it was introduced to the UK from Scandinavia in the reconstruction period after the war, it was hailed as an innovative wonder material.
In fact, if RAAC planks – the technical name for the concrete panels – in a building are properly protected, there is a maintenance schedule and there is no sign of water ingress, the roof will likely be fine and the facility can continue to be used.
According to construction and engineering materials expert Professor Chris Goodier of Loughborough University, RAAC is still manufactured and installed all over the world and can be an appropriate construction material if properly designed, manufactured, installed and maintained.
The problems arise in situation where maintenance has been neglected over the course of years, or indeed decades. In buildings from the fifties, sixties and seventies, when RAAC was used freely, maintenance regimes were not as comprehensive as they are now and users did not know what to look for or what to do.
Given that the material was lightweight and economical, it is hardly surprising that many manufacturers were happy to supply it – with the best of intentions and with no foreknowledge of the issues which would rear their heads further down the line.
Although local authorities have been aware of RAAC in their buildings for some time, things came to the boil a year ago when the Office of Government Property sent a Safety Briefing Notice to all Property Leaders, regarding the dangers of RAAC, stating that “it is now life-expired and liable to collapse”.
It put the onus squarely on those responsible for the management, maintenance or alteration of central and local government buildings to know whether their buildings contain RAAC and, where they do, to act appropriately to ensure that such buildings are deemed safe.
How can those concerned go about this? The first step is inspection, either by a surveyor or a structural engineer. Both are professionals who will act in the client’s interest, the difference being that the former will identify problems while the latter will also propose manageable solutions.
Inspection is eased by the fact that most RAAC planks are in flat roofs on single-storey buildings. Drones can give a clear picture of the roof covering and heat sensors can check if water has penetrated.
If there is water ingress, then as far as RAAC is concerned it is game over. There is no remedial solution and use of the building has to be immediately stopped. However, RAAC planks can be replaced with traditional roofs with timber joists or a dual-pitch roof truss.
The good news is that RAAC does not affect residential buildings. The bad news is that, like a previous panic – asbestos, many owners or operators of public or commercial properties do not know that they are, or might be, affected.
The issue is not going to go away. But there are answers to it, and prudence would dictate more regular monitoring and inspection regimes – something that will almost certainly be factored in by insurance companies at renewal time.
However, It’s not a case of RAAC and ruin. Professional advice and guidance can alleviate the understandable instinct to panic.
Alan Ferns is Director – Structural Engineering at Dougall Baillie Associates
Building, Design & Construction Magazine | The Choice of Industry Professionals