Magnetic couplings, also known as magnetic drives, are contactless torque-transmitting devices with endless applications across a wide range of industries. Unlike mechanical couplings, magnetic couplings transfer torque through magnetic fields, eliminating issues with shaft misalignment, backlash, lubrication needs, vibration, etc.
Nested within nonmagnetic containment shells, magnetic couplings consist of two magnetic poles: a driving magnet rotor and a driven magnet rotor. As the driving magnet rotates under the influence of the motor drive, it causes rotation of the driven magnet while maintaining an air gap separation. This contact-free torque transmission makes magnetic couplings incredibly reliable and low maintenance.
In the following sections, you’ll discover the six common industrial applications taking advantage of magnetic coupling.
1. Sewage And Wastewater Mixing
You need dependable, rugged equipment to mix sewage and wastewater effectively. Submersible mixers prevent the escape of hazardous gases through vulnerable shaft seals. Magnetic couplings excel in these demanding mixing applications. Their enclosed design prevents abrasive solids and stringy materials from contaminating mechanical seals.
Without routine seal maintenance to worry about, you’ll achieve reliable, quiet operation. Magnetically coupled mixers maintain their integrity even after prolonged exposure to grease, rags, grit, and corrosive substances prevalent in sewage tanks.
Trouble-free operation translates to reduced maintenance costs and longevity of capital equipment. For mixing equipment able to withstand sewage plant conditions, look no further than magnetic couplings.
2. Chemical And Pharmaceutical Mixing
You need specialized mixing equipment when handling volatile chemicals or sensitive pharmaceutical compounds. Magnetic couplings perfectly suit these applications because their completely enclosed design prevents vapors from escaping the mixer vessel.
Without shaft seals that can leak, fail, or allow bacterial ingress, magnetic drives support sterile processes and hazard containment. They provide reliable, leak-free operation even when mixing volatile solvents, corrosive chemicals, or viscosity-sensitive pharmaceutical suspensions.
By customizing magnetic drives to correctly match process loads, you will achieve optimal mixing efficiency without routine seal maintenance.
3. Food And Beverage Mixing
Maintaining stringent hygiene standards is essential when mixing food or beverage ingredients. Magnetic mixers excel in these applications because their fully enclosed design eliminates shaft seals that can leak lubricants or allow bacterial ingress.
Without worrying about mechanical seal failures or costly seal maintenance, you’ll achieve reliable blending and mixing efficiency. The leakproof operation prevents contamination between batches and supports robust HACCP compliance.
Whether you need to stir vats of fruit juice gently, knead dough, or disperse powdered milk, magnetic mixers prevent leaks and keep the internal vessel surfaces smooth and easy to clean. Trust their clean-running, sanitary design for your food quality assurance and safety processes.
4. Pump Drives
Pumping abrasive slurries or corrosive fluids poses reliability challenges for mechanical seals and packings. By eliminating the pump shaft seal—the most vulnerable component—magnetic drives provide a robust sealing solution.
Without having to constantly maintain and replace leaky shaft seals, you will benefit from enhanced pump reliability and longevity.
Magnetically driven pumps excel when handling demanding fluids like crude oil, mine tailings, acids, solvents, or any liquid with suspended solids. Their leakproof operation prevents hazardous leaks while reducing downtime.
For pump applications involving hazardous, volatile, or abrasive liquids, magnetic drives keep pumps running efficiently without routine seal maintenance. Trust their uncomplicated yet ingenious design for your toughest pumping duties.
5. Metal Processing
Transporting or mixing molten metals exceeding 1,100°F quickly destroys mechanical seals and packings. This renders shaft-driven equipment unsuitable for foundries and metal processing plants.
In contrast, magnetic transfer drives reliably withstand extreme temperatures above 2,000°F. Thanks to their totally enclosed design, these drives won’t leak hazardous fumes or waste valuable metal alloys.
Magnetically driven pumps, screw conveyors, and mixers improve safety and longevity while reducing maintenance costs associated with mechanical seals. When handling molten aluminum, bronze, or steel alloys, trust magnetic drives to endure high temps and keep equipment fully enclosed for leakproof metal transport.
6. Plastics Manufacturing
Sealing extruders, kneaders, and mixing equipment against resin leaks is imperative for facility safety and to avoid wasted materials in plastic production. Magnetically driven equipment excels in these applications due to the fully enclosed design lacking vulnerable shaft seals. You can rest easy knowing resin leaks will not endanger employees or foul the production environment.
At the same time, leakproof magnetic drives prevent lost revenue from wasted materials. Their reliable sealing effectiveness continues even after prolonged exposure to abrasive compounds and corrosive cleaning chemicals used in plastics manufacturing plants.
Final Thoughts
In demanding industrial environments, magnetic couplings tick all the right boxes—safety, reliability, longevity, and efficiency. By eliminating rotating seals, they keep equipment fully sealed off from corrosive, abrasive, volatile, and extreme process fluids. This prevents leaks and hazards while reducing maintenance. Though advanced in design, magnetic drives provide trouble-free coupling thanks to simple operating principles that have been unchanged for over 50 years. They’re built to handle the toughest tasks across every industry.
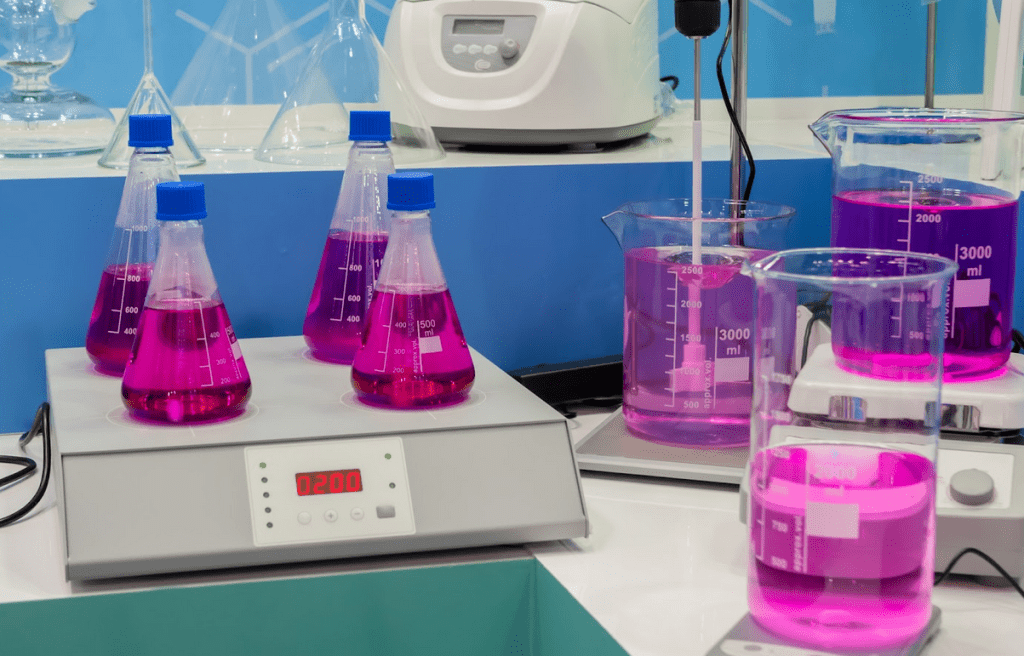