In today’s fast-paced business world, efficiency is the key to success. Whether you’re running a manufacturing facility, a construction company, or any other industry that relies on cutting materials, having the right cutting equipment can make a significant difference in your productivity and bottom line. Investing in high-quality cutting tools not only saves time and money but also ensures precise and consistent results.
In this article, we’ll explore the various types of cutting equipment available and how to choose the best ones for your business needs.
Understanding The Types Of Cutting Equipment
When it comes to cutting equipment, there’s no one-size-fits-all solution. Different materials and applications require different tools. Here are some of the most common types of cutting equipment, like those from Milestone Equipment, you should be familiar with:
1. Shears and Scissors
Shears and scissors are among the most basic and versatile cutting tools available. While household scissors are designed for cutting paper and lightweight materials, industrial shears are heavy-duty tools that can cut through thicker materials like metal sheets, rubber, and even plastics. Shears come in various designs, such as straight shears, curved shears, and aviation snips, each tailored for specific cutting applications.
The advantages of shears and scissors include their portability, ease of use, and low maintenance requirements. However, they’re best suited for cutting thin materials and may not be practical for thicker or harder materials.
2. Band Saws
Band saws are powerful cutting machines that use a continuous loop of toothed metal blades to cut through a wide range of materials. They’re commonly used in metalworking, woodworking, and construction industries. Band saws come in different sizes and configurations, from small benchtop models to large freestanding machines.
One of the main advantages of band saws is their versatility. They can cut straight lines, curves, and intricate shapes with precision. Band saws are also capable of cutting thick materials, making them suitable for various applications. However, they require proper blade selection and adjustment for optimal performance.
3. Plasma Cutters
Plasma cutters are advanced cutting tools that use a high-energy plasma arc to cut through electrically conductive materials like steel, aluminum, and stainless steel. They work by ionizing the gas and creating a powerful stream of plasma that can melt and cut through metal with incredible precision.
Plasma cutters are known for their ability to make intricate cuts and cut through thick materials with ease. They’re commonly used in metalworking, fabrication, and construction industries. However, plasma cutters require specialized knowledge and safety precautions due to the high temperatures and electrical hazards involved.
4. Laser Cutters
Laser cutters are highly precise cutting machines that use a focused laser beam to cut through materials. They’re commonly used for cutting flat materials like metal, wood, acrylic, and fabric but can also be used for engraving and marking.
Laser cutters offer several advantages, including high accuracy, minimal material waste, and the ability to create intricate designs and patterns. They’re particularly useful in industries that require precise and complex cuts, such as aerospace, automotive, and sign-making.
However, laser cutters can be more expensive than other cutting equipment and may have limitations in terms of the thickness of materials they can cut.
5. Water Jet Cutters
Water jet cutters are cutting machines that use a high-pressure stream of water mixed with an abrasive material to cut through various materials, including metal, stone, and glass. They work by focusing a narrow stream of water and abrasive particles to cut through materials with precision and minimal heat generation.
Water jet cutters are known for their ability to cut complex shapes and patterns with high accuracy, even in thick and hard materials. They’re commonly used in industries like aerospace, automotive, and construction, where precise cutting is essential.
One of the advantages of water jet cutters is their ability to cut materials without causing heat-related distortions or material degradation. However, they require a consistent supply of water and abrasive materials, which can increase operating costs.
Factors To Consider When Choosing Cutting Equipment
To ensure you make the right investment, consider these factors when choosing cutting equipment for your business:
1. Material Type
Choosing the right cutting equipment for your business starts with understanding the materials you’ll be working with. Different cutting tools are designed to handle specific materials effectively. For example, shears and scissors are best suited for thin materials like paper, fabrics, or thin metal sheets, while plasma cutters are designed for cutting through thick, electrically conductive metals like steel and aluminum. Mismatching the cutting equipment with the material can lead to poor cut quality, excessive wear and tear, or even safety hazards.
2. Cutting Capacity
The cutting capacity of the equipment is another critical factor to consider. This refers to the maximum thickness and size of materials the cutting tool can handle without straining or compromising precision. For instance, if you frequently need to cut thick metal plates or large pieces of wood, a heavy-duty band saw or plasma cutter with a higher cutting capacity would be more suitable than a smaller, less powerful machine. Choosing equipment with insufficient cutting capacity can lead to inefficient operations, increased downtime, and potential safety risks.
3. Precision and Accuracy
Depending on your application, you may require cutting equipment that can deliver extremely precise and accurate cuts. Industries like aerospace, automotive, and precision manufacturing often demand tight tolerances and intricate designs. In such cases, laser cutters and water jet cutters are excellent choices due to their high precision and ability to create complex shapes and patterns with minimal material waste.
4. Speed and Efficiency
If your business has high-volume cutting needs, prioritizing equipment that can cut quickly and efficiently without sacrificing quality is crucial. Factors like cutting speed, feed rate, and automated material handling can significantly impact productivity. For example, a high-speed plasma cutter or a computerized numerical control (CNC) cutting machine may be more suitable for high-volume applications compared to manual cutting tools.
5. Cost and Maintenance
While high-end cutting equipment can be a significant investment, it’s essential to consider the long-term cost of ownership, including maintenance, repairs, and consumables. Some cutting tools may have lower upfront costs but higher operating expenses due to frequent blade replacements or higher energy consumption. Additionally, maintenance requirements and the availability of spare parts should be considered to minimize downtime and ensure a longer lifespan for the equipment.
By carefully evaluating these factors, you can make an informed decision and choose cutting equipment that aligns with your business’s specific needs, ensuring optimal efficiency, productivity, and cost-effectiveness.
Maximizing Efficiency With The Right Cutting Equipment
Investing in the right cutting equipment can significantly boost your business’s efficiency in several ways:
1. Increased Productivity
High-quality cutting tools are designed to operate at optimal speeds and with minimal downtime. They can cut through materials faster and with fewer interruptions, allowing you to complete more projects in less time. For example, a high-speed plasma cutter or a CNC cutting machine can drastically reduce the time it takes to cut through thick metal plates compared to manual cutting methods.
2. Reduced Material Waste
Precise cutting equipment ensures accurate cuts, minimizing material waste. This not only saves you money by reducing the amount of raw material you need to purchase but also contributes to a more sustainable and environmentally friendly operation. Laser cutters and water jet cutters are particularly effective at minimizing waste by making intricate cuts with minimal kerf (the width of the cut).
3. Improved Quality
Consistent and accurate cuts are essential for producing high-quality products that meet specifications and customer expectations. Modern cutting equipment, such as CNC machines and laser cutters, offer repeatable precision and accuracy, ensuring that each cut is identical to the next. This consistency in quality can enhance your reputation and customer satisfaction, leading to increased business opportunities and loyalty.
4. Safer Operations
Modern cutting equipment often incorporates advanced safety features, reducing the risk of accidents and injuries in the workplace. For instance, many machines have built-in safety guards, emergency stop buttons, and automatic shut-off mechanisms to protect operators from potential hazards. Additionally, some cutting tools, like water jet cutters, operate at lower temperatures, reducing the risk of burns or fire hazards.
Maintenance And Safety Considerations
To ensure your cutting equipment operates at peak efficiency and maintains a long lifespan, proper maintenance is crucial. Here are some tips:
1. Follow the Manufacturer’s Guidelines
Adhering to the recommended maintenance schedules and procedures outlined in the equipment’s manual is essential. This includes regular servicing, lubrication, and replacement of consumable parts. Failure to follow these guidelines can lead to premature wear and tear, increased downtime, and potential safety hazards.
2. Keep Equipment Clean
Regularly cleaning and lubricating your cutting tools can prevent the buildup of debris, dust, and other contaminants that can interfere with smooth operation. This simple maintenance task can extend the life of your equipment and ensure consistent performance.
3. Inspect and Replace Parts
Regularly inspecting your equipment for worn or damaged parts is crucial. Replace worn blades, filters, or other components promptly to avoid breakdowns or accidents. Continuing to use worn or damaged parts can compromise the quality of cuts and pose safety risks.
4. Train Employees
Ensure all employees who operate cutting equipment are properly trained in its safe use and maintenance. Provide comprehensive training on the equipment’s features, safety protocols, and proper operating procedures. Regular refresher training can also be beneficial to reinforce safe practices.
5. Implement Safety Protocols
Establish and enforce safety protocols, such as wearing appropriate personal protective equipment (PPE) and following lockout/tagout procedures during maintenance. Additionally, ensure that work areas are well-ventilated and that all safety guards and emergency stops are functioning correctly.
Choosing The Right Cutting Equipment Supplier
Partnering with a reputable and reliable cutting equipment supplier is essential for your business’s success. Consider these factors when selecting a supplier:
1. Product Quality
Look for a supplier that offers high-quality cutting equipment from reputable manufacturers. Reputable brands often have a proven track record of durability, performance, and customer satisfaction.
2. Technical Support
Choose a supplier that provides comprehensive technical support, including installation, training, and maintenance services. Having access to knowledgeable technicians can ensure proper setup, operation, and maintenance of your cutting equipment, maximizing its lifespan and efficiency.
3. Inventory and Availability
Ensure the supplier has a wide range of cutting equipment in stock and can quickly fulfill your orders. This can minimize downtime and ensure that you have the necessary tools to meet your production schedules.
4. Customer Service
Prioritize a supplier with excellent customer service, responsive communication, and a commitment to addressing your needs. A reliable supplier should be able to provide timely support, answer your queries, and offer solutions to any issues you may encounter.
5. Warranty and After-Sales Support
Look for suppliers that offer extensive warranties and after-sales support for their products. This can provide peace of mind and protect your investment in case of any defects or issues that may arise during the equipment’s lifespan.
By partnering with a reputable supplier and following proper maintenance and safety protocols, you can maximize the efficiency and longevity of your cutting equipment, ensuring optimal productivity and profitability for your business.
Conclusion
Investing in the right cutting equipment is a crucial step toward maximizing efficiency in your business. By carefully considering your material needs, cutting requirements, and budget, you can choose the most suitable equipment that will enhance productivity, reduce waste, and improve product quality. Remember to prioritize maintenance and safety, and partner with a reliable supplier to ensure your cutting equipment operates at peak performance for years to come.
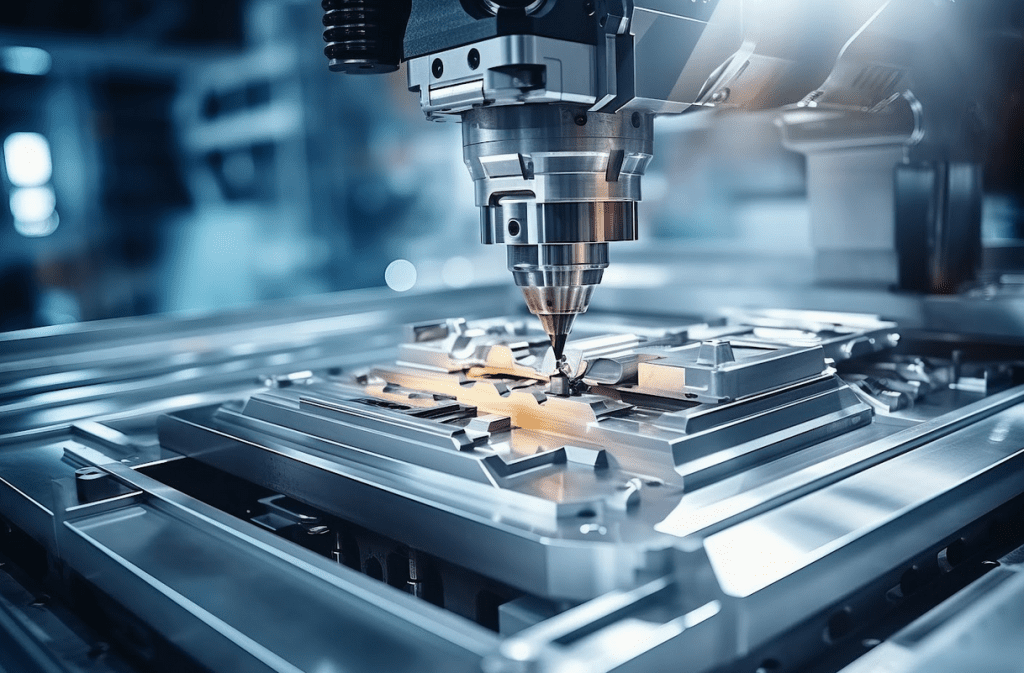