Plastics are a ubiquitous part of our lives, offering versatility and functionality in countless applications. However, the plastics manufacturing industry faces significant challenges in achieving a more sustainable future. Here, we explore the six key hurdles and potential solutions that can pave the way for a more responsible and environmentally friendly approach.
The Challenges
The plastics manufacturing industry grapples with several environmental and economic challenges that threaten its long-term sustainability. From the environmental impact of production to the complexities of waste management, these hurdles demand innovative solutions.
Environmental Impact
Plastic’s path from the cradle to the grave leaves a significant environmental mark. The extraction and refining of fossil fuels for raw materials creates greenhouse gas emissions that contribute to climate change. Manufacturing itself is energy-intensive. For example, injection molding machine require significant amounts of power to operate. This adds to the industry’s carbon footprint.
The problem doesn’t end there. Disposal of plastic products often leads to overflowing landfills or, worse yet, plastic pollution in our oceans, harming marine life and ecosystems.
Waste Management
Our throw-away culture collides with the reality of plastic’s durability. With a meager global recycling rate of around 20%, most of the plastic ends up in landfills or the environment.
This inefficient resource use not only squanders valuable materials but also contributes to the plastic pollution crisis. Landfills are overflowing, and plastic debris in our oceans threatens wildlife and disrupts entire ecosystems.
Cost Pressures
Manufacturers constantly walk a tightrope between cost and sustainability. Fluctuations in oil prices, a key material in plastic production, can wreak havoc on production budgets. Other economic factors also play a role.
In this environment, manufacturers are often incentivized to choose cheaper, less sustainable production methods to maintain profitability. This short-term gain comes at a long-term cost to the environment.
Supply Chain Disruptions
The global supply chain is fragile. Disruptions can occur at any point, from the source of raw materials to the destination of finished plastic products.
These disruptions can lead to production slowdowns, causing shortages and driving up prices for both manufacturers and consumers. A more robust and geographically diverse supply chain is crucial for the industry’s resilience.
Skilled Labor Shortage
The complex machinery used in plastics manufacturing requires a skilled workforce to operate and maintain it effectively. Unfortunately, the industry faces a growing shortage of qualified workers with the necessary technical knowledge and expertise. This lack of skilled labor can hinder production efficiency, limit innovation, and ultimately impact the industry’s ability to adapt and compete.
Government Regulations
As environmental concerns mount, governments worldwide are taking action. Stricter regulations on plastic use and disposal are being implemented, creating new requirements and challenges for manufacturers.
These regulations may limit the types of plastics used, mandate higher recycled content in products, or even ban single-use plastics altogether. While these regulations pose challenges, they also present opportunities for innovation and adaptation as manufacturers strive to comply while maintaining their businesses.
By embracing new technologies and sustainable practices, manufacturers can navigate a path toward a more responsible future.
Finding Solutions for a Sustainable Future
Despite these challenges, the plastics industry is not without options. Companies like Plastic Molded Concepts demonstrate how precision manufacturing can align with sustainability goals. With advanced engineering resins and efficient molding techniques, manufacturers can reduce material waste while maintaining durability for mission-critical applications.
By embracing collaboration and technological advancements, manufacturers can move towards a more circular and environmentally conscious model:
The Circular Economy
This approach throws out the linear ‘take, make, dispose’ model and embraces a closed-loop system. Imagine a world where plastic products are designed for multiple lives.
Products could be easily disassembled for reuse or recycling, made from similar plastic types for simpler sorting, and even compostable for organic waste streams. This not only reduces reliance on virgin plastic but also simplifies the recycling process, keeping valuable materials in circulation.
The Power of Recycling
Recycling plays a central role in the circular economy. By increasing the use of recycled content in new products, manufacturers can significantly reduce their dependence on virgin plastic feedstock. This translates to less reliance on fossil fuels and minimized waste generation overall.
Advancements in chemical recycling technologies offer exciting possibilities. These technologies can break down even complex plastic mixtures into their basic building blocks, allowing them to be reborn into new products, further closing the loop on plastic use.
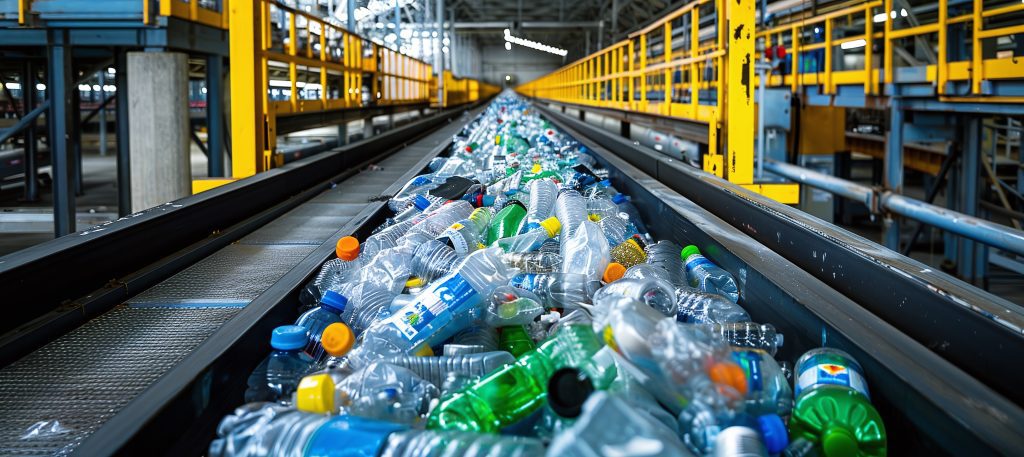
Bioplastics
Bioplastics, derived from renewable resources like plant starches, seem like a promising green alternative. However, the picture isn’t entirely rosy. The production methods and biodegradability of bioplastics can vary greatly.
Some may require industrial composting facilities, which are not readily available everywhere. Ongoing research is crucial to improve the overall sustainability profile of bioplastics, ensuring they truly live up to their potential as an environmentally friendly option.
Digital Transformation
The digital revolution is poised to transform the plastics industry. Data analytics can identify areas for waste reduction and optimize production processes.
Predictive maintenance can prevent equipment failures, minimizing downtime and wasted materials. These digital tools can streamline operations, improve efficiency, and pave the way for a more sustainable future for plastics manufacturing.
Innovation in Design
Rethinking product design is key. Imagine packaging that uses minimal plastic, perhaps even being entirely replaced by compostable alternatives. Designing products for easier disassembly, repair, and recycling extends their lifespan and minimizes waste generation from the very beginning.
By prioritizing reusability and recyclability at the design stage, manufacturers can create a future where plastic plays a valuable role in a circular economy.
The path towards a sustainable plastics industry is paved with collaboration and innovation. By embracing these solutions, manufacturers can ensure that plastics remain a valuable material while minimizing their environmental impact for generations to come.
In Closing
The plastics industry faces a crossroads. Environmental concerns and practical challenges demand change. However, through embracing the circular economy, innovation, and collaboration, manufacturers can navigate a path towards a more sustainable future. By prioritizing responsible production, design, and waste management, plastics can continue to play a valuable role in our lives without leaving a negative mark on the environment.