Considerations for facility owners and operators…
While it may seem counterintuitive that fire is even a risk in spaces designed to maintain cold temperatures, cold storage in fact presents a huge fire hazard for warehouse designers and builders, life safety installation companies and facility owners. In this article we cover the risks, considerations and best detection products when thinking about life safety for cold storage warehouses.
In the last year, the UK’s cold storage industry capacity has topped 40 million cubic meters, for the football fans amongst you that is the equivalent to the bowl volume of 35 Wembley Stadiums. This is being driven by consumer demand and big business for perishable goods and pharmaceutics, making cold storage an essential cog in the UK economy.
From a feasibility point of view however, cold storage is substantially more complicated and more expensive than dry storage because of the regulations around refrigerated freight. Plus, the very nature of the materials used in cold storage, means it presents a higher risk factor when it comes to fire. So as the demand for refrigerated products grows, so does the need for better fire safety.
Why no two cold storage units are the same
Cold storage areas vary in size, usage, and ambient temperature, meaning that any fire detection equipment or system must be specifically designed to each warehouse. You may be surprised at some of the products that may need cold storage. There are the obvious ones like perishable food (vegetables, fruits, meat and seafood, dairy products), but what about flowers and plants, biopharmaceutical products and did you know, even some artwork needs to be kept at low temperatures. Understanding the unique circumstances of the product is essential for cold storage fire safety.
A bespoke fire risk assessment will determine the life safety system needed to maintain optimum fire security 24/7, protecting the goods, equipment and most importantly staff operating within the building, but this can be a complicated task to map out and assess for the responsible person. So, where to start?
What are the fire risks in cold storage warehousing?
Besides arson attacks and carelessness from people on site (think discarded cigarette butts), fire risks within cold storage mostly arise from electrical or mechanical faults in the conveyor systems which transport the goods around the building, wiring that is housed in the roof or faulty lighting systems. The fuels which power the evaporative condensers used to sustain the low temperatures in cold storage warehouses is highly flammable so must be stored safely, and the machines themselves can also be a major contributor to fire risk. These machines remove air moisture to extremely low levels of humidity to keep the warehouse cool, which can create an increased risk of static electricity and in the case of a fire could accelerate the spread of flames.
Cold storage fires have the potential to be devasting, posing a threat to life, destroying business operations and be detrimental to the supply chain. Even small fires can cause huge damage to a refrigeration business – a rise in temperature due to cooling plant down-time following a fire, can lead to stock being damaged. The strict laws around downtime requirements make it even more important to choose the right method of fire protection.
There are also considerations to be made around smoke damage, as any stock exposed to low levels of smoke over an extended period can quickly become contaminated and therefore not fit for human consumption.
Of course, the issues are further compounded by the fact that modern technology now means that an increased number of warehouses are automated almost 24 hours a day, meaning very few or no personnel are on site. This makes visual identification of a fire incident unlikely, so the safety of the building is completely dependent on automatic fire detection systems – making it imperative that the system in place is up to date and well maintained.
What can be done to prevent a cold storage warehouse fire?
Dangerous scenarios are preventable when fire safety experts have been consulted, the correct life safety equipment is installed, the electrics and mechanical devices in use within the building are well serviced and the correct health and safety regulations are followed. Essential action when you consider preventable fires in the UK warehouse industry costs our economy upwards of £230 billion each year.
A risk assessment, when carried out properly and thoroughly according to law (The Regulatory Reform (Fire Safety) Order 2005), is the first place to start. It is also advisable to get an independent audit by a consultant or insurer as this will help ensure any fire strategy for your cold storage facility is robust.
Many modern warehouses now include firewalls which are a cost-effective solution to manage the risk of fire. Smart warehouse managers should also consider the safe storage of waste and other flammable materials to stop the spread of fire if it were to break out. Keeping these materials in a designated safe storage area will reduce the risk of them causing a fire.
The best way to save lives of course, is to ensure automatic fire detection is in place, across your entire cold storage facility. With special attention paid to vulnerable areas. Fire specialists can advise on multiple fire detection solutions that are ideal for warehouses, but it is important to ensure that the right one for your scenario is installed.
Why air sampling fire detection is a good option for cold storage warehouses
There are multiple fire detection systems that can be used to protect warehouse storage, but when it comes to cold storage, you need to plan and design appropriately.
Beam detectors which are commonly used in large warehouses can frost over in a cold storage situation, there are options in the market now which include heated optical elements to negate this however they might not be a device to solely rely on. Point detectors would also frost over and wouldn’t necessarily provide the appropriate cover. Flame detection is a possibility, depending on the risk assessment, but it is important to consider the materials being stored and how a fire is likely to start with these materials. But generally anything kept at low temperature that might produce flames (chemicals for instance) could potentially cause an explosion before the flames were even registered. Therefore, working with specialist fire installers who have experience in this field and work with manufacturers who produce specialist devices is the only way to ensure your cold storage facility is adequately protected.
Air Sampling Fire Detection is a smart choice, especially in a cold storage facility. Just make sure suitable dust filtration is in place to prevent false alarms. If professionally designed and installed, they can be incredibly simple to maintain.
Air Sampling Fire Detection systems use the suction of air in conjunction with small pipe work to sample the air for smoke. This method is up to 200 times the sensitivity of a traditional point detector because of the strategically placed pipes and sampling holes. The air impeller can sample the air by drawing it along the pipe and into the detector measuring chamber. These aspirating smoke detection systems are designed to provide an elevated level of sensitivity to smoke detection, therefore detecting smoke at the earliest stage in the development of a fire.
With this high sensitivity capability of air sampling there is of course an increased risk of false alarms if it is not configured to suit the environment. False alarms can be reduced if the device in place uses a dust discrimination system which allows for the detection threshold levels to be set, helping to identify the difference between dust particles and smoke particles.
Some systems even allow for pipework to be customised to fit the unique circumstances of a cold storage warehouse, meaning sampling holes can be placed in specific locations for precision, accuracy, and efficiency in sampling – thus avoiding dilution. There are other things to consider when designing the pipework in the cold store. For example, the sampling pipe should be installed in the cold store itself rather than above it with capillary sampling points through the ceiling. This is because condensation could collect in the capillary pipe and freeze very quickly. Sampling points drilled in the side of the pipe rather than the bottom will prevent the sampling points becoming blocked by ice. Condensation will be created in the pipe when the air moves from the cold store to the detector. The provision of a moisture trap or heater box will ensure that all the moisture is removed before the air reaches the detector.
These are just a few pointers to be mindful of but following the manufacturer guidelines will ensure that the Aspirating detectors provide reliable, trouble-free, and false alarm-free protection.
Aspirating detectors are a great option to investigate with your fire safety consultant or installation company to help avert disaster, satisfy insurer oversight, and improve safety for workers and of course any surrounding buildings or the public.
Why warehouse managers need to review their fire strategy
Driven by consumer demand, the trend for more (and larger) cold store warehouse units will continue to grow; take a drive along any major motorway in the UK to see these huge buildings becoming common place. Globally, the cold storage market was valued at $112 billion in 2021 and is expected to reach $330.2 billion by 2030. With this growth, the risk of fire also increases, so it is important for logistics companies and cold warehouse managers to understand the risk.
For business to meet demand and grow safely, it is important to have a thorough and up to date fire safety strategy in place for the unique circumstances of your cold storage. The fire strategy needs to meet the latest government legislation and consider the fact that insurance companies are tightening their belts when it comes to fire risk, particularly for cold storage with fire-accelerating environments. Responsible persons who work with experts to ensure a robust fire strategy that is best for the unique products of their cold storage is key. This includes advising on design of a life safety system and the ongoing maintenance of any devices or systems in place. Cold storage fire safety cannot simply be a fit and forget scenario. The teams who make these considerations will be the ones who benefit from better insurance premiums and be able to provide the best and most reliable service to their customers, allowing the industry to grow to the predicted rates safely
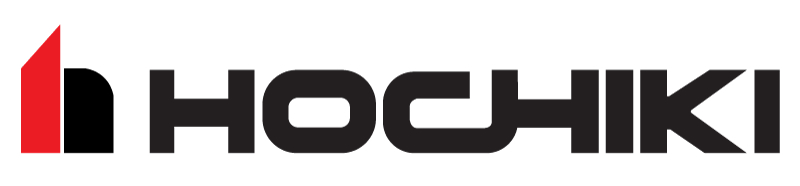
Building, Design & Construction Magazine | The Choice of Industry Professionals