To be by-lined to Richard Brookes, Group Head of Health and Safety, South Staffordshire Plc…
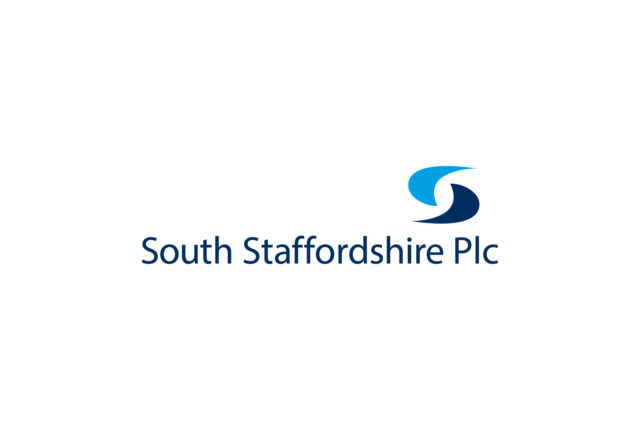
When we use the words Health and Safety, our first thoughts usually aren’t that; real work is messy, events have multiple causes, you should trust your experts or, you should be focusing where nothing has gone wrong.
The traditional and most common way to manage safety is to investigate after something has gone wrong, to identify the single root cause and, typically, put a person fix or new admin control in place to prevent the same thing happening again. We’ve become very fixated on this approach, and have perhaps, started to run the risk of over simplifying how we manage risk improvement.
As the world, work, systems and technology become ever more complex, we become more reliant on subject matter experts to help us manage our facilities and the equipment we depend on. As supply chains and contractual relationships become wider and deeper, we should ask ourselves some questions:
- given this complexity, should we continue to use simple, linear methods to review safety performance?
- Can we continue to see the root cause as a worker making a poor choice or failing to follow procedures?
- Or, do we need to start asking different questions?
Waiting for the bad outcome or assuming high risk tasks are well managed can no longer be good enough as work becomes more complicated.
A relatively recent development in safety management uses a Human and Organisational Performance viewpoint (or HOP). HOP takes a systems and person approach to work as a means to understand the conditions in which people are set to and work in. It emerged from the US Department of Energy and has been shared by safety thought leaders such as Todd Conklin.
HOP has five guiding principles; error is normal; blame fixes nothing; systems and conditions drive behaviour; leadership response to failure matters; and learning is deliberate. Taking the guiding principle of ‘learning is deliberate’, one of the changes that organisations can undertake is to implement ‘Learning Teams’ to adopt a HOP approach to safety.
What are Learning Teams?
They are a proactive way to understand how normal work gets delivered successfully. When we say successfully, we mean in the absence of anything going wrong, or anyone being hurt. It’s the inverse approach to traditional safety. Don’t wait – you investigate when nothing happens. That might sound strange, but things going wrong are an ever-shrinking data pool. You can conduct a learning team on anything, but a great place to start is with highest risk tasks; anything that has the capacity to kill or have life altering consequences.
Who should be involved?
The most important people to be involved are those who actually do the work. They know the job best and understand the changes and adaptations they make every day to get things done. This is one of the biggest benefits; deeper insight into work as it’s actually done, not as it’s imagined in the written process. You can start to understand how workers make decisions and how systems and procedures can alter overtime. If we are only interested after something’s gone wrong, it’s all too easy to see this gap. How often do we investigate what’s happened, after the bad outcome, to conclude that workers didn’t follow the process? That’s because processes often change slowly overtime, as work exists in the real, complex world and constantly changes to meet the demands of various trade-offs.
Having a coach, or facilitator is also essential; someone who can get people talking and make it ok to share. Creating a psychological safe environment is essential to learning.
The benefits of learning teams
- No one has to be harmed to learn something new and we will invariably find things we wouldn’t in a traditional post event investigation. Traditional investigations are the hardest places to learn, especially when someone’s been hurt – the emotional, ethical and political challenges are hard to get beyond. Learning teams, on the other hand, are proactive and don’t carry the same level of resistance and emotion.
- It keeps the highest business risks under constant curiosity, always seeking to improve rather that assuming we’re performing well. Understanding normal risk is a far bigger data pool to analyse and learn from.
- It helps to improve engagement and builds trust with operational teams who help create solutions and improvements. Ownership and accountability increases when teams are part of the solutions. We become more sensitive to the next deviation in work workers may need to make and allow the change to become visible.
- Learning teams embrace real work as it’s done and therefore the complexities of normal, messy work. It’s not about seeking root cause, but rather an appreciation for the numerous ways things could go wrong and the adaptions made to manage safe outcomes.
- They help identify the expectations and constraints we place on workers. This could be the expectation of the client, the principal contractor, the regulator, the boss, the auditor, the HR team or the H&S manager; competing priorities that have to be managed every day. The constraints that exist that workers absorb could be poor tools, schedules, resources, weather, unexpected change. Our people do this so well nearly all the time that we don’t even notice. The only time we currently do is when a bad outcome occurs, and it’s high time that this changed.
Building, Design & Construction Magazine | The Choice of Industry Professionals