Temporary works specialist, Altrad RMD Kwikform (Altrad RMDK), in partnership with Balfour Beatty VINCI, played a key role in the construction and repositioning of the A46 Kenilworth Bypass Box Structure, a critical element of the HS2 high-speed rail project.
Project Overview
The A46 is a major highway connecting Coventry, Kenilworth, and Leamington Spa to the M40. To accommodate the new HS2 rail line, a 14,500-tonne box structure was built adjacent to the carriageway before being manoeuvred into place beneath the A46. This approach significantly reduced disruption to road users by eliminating the need for up to two years of extensive roadworks.
Spanning 42 metres wide, the structure required extensive planning and engineering to manage its substantial weight. The installation followed a carefully coordinated sequence: first, the construction of the structure itself, followed by meticulous site preparation to ensure the controlled and precise movement of the box into position. Advanced engineering techniques were employed throughout to maintain structural integrity while minimising disruption to local traffic and the surrounding environment.
The Challenge
This was the heaviest bridge move in the UK. To achieve this, specialist civil and structural engineering company Freyssinet designed a guiding raft and jacking mechanism to push the box at an average speed of 6.5 metres per hour, ensuring accuracy in positioning while safeguarding the structure’s integrity.
Adding to the complexity, the project required a continuous supply of temporary works solutions and on-site equipment to facilitate the move. At its peak, over 800 tonnes of equipment were in use, with additional resources mobilised for night shifts to maintain progress and keep the operation on schedule.
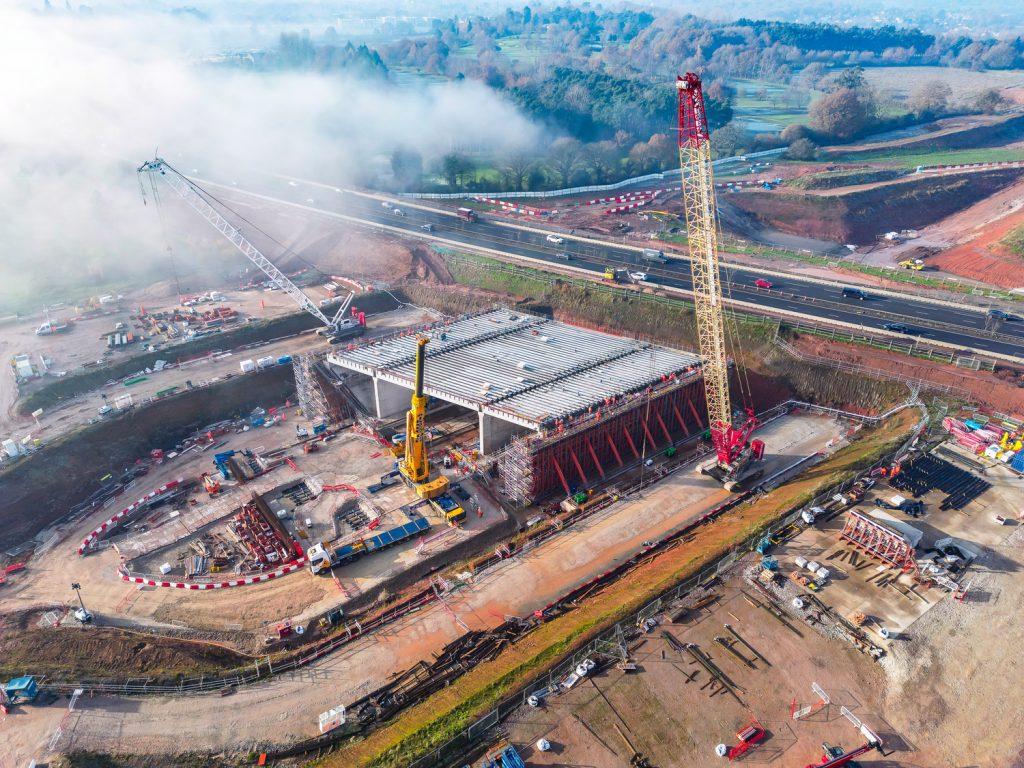
The Solution
To support the structure’s significant weight, Altrad RMD Kwikform developed an innovative temporary works solution, adapting a combination of formwork and falsework supports. This combination of advanced and conventional techniques ensured both safety and efficiency throughout the operation.
Superslim Soldiers, known for their exceptional strength-to-weight ratio, provided the primary structural support, ensuring stability in confined spaces and under tight time constraints.
Alform beams were also installed in conjunction with the Superslim Soldiers to form a shutter configuration on either side of the structure, offering robust support during each controlled concrete pour.
Tubeshor ground shoring props were applied in an inclined orientation at 45-degree angle along the outer edges of the formwork. A total of 22 Tubeshor props – 11 on each side – were deployed to supplement the primary support systems to facilitate landing of precast beams and deck casting. Until the structure was made fully integral, the cast inclined walls were not self-supporting.
Throughout the project, a series of concrete pours were meticulously executed to reinforce the structure. These included ten inclined wall pours, six tulip pier pours, four base pours, and one deck pour. A summary total of over 4300m3 of concrete was used during construction of the overbridge. The temporary works solutions ensured stability throughout the curing process, allowing the systems to be removed efficiently upon completion.
Altrad RMD Kwikform played a vital role in ensuring a seamless operation by supplying essential equipment around the clock and coordinating timely deliveries. This effort allowed the project to progress smoothly, meeting key milestones while minimising disruption to the local community.
Stuart Grant, Senior Sales Representative at Altrad RMD Kwikform, commented: “We pride ourselves on being a one-stop shop for temporary works solutions. From Superslim Soldiers to Tubeshor, we were able to provide all the essential equipment and expertise under one roof, ensuring we kept to the programme and successfully delivered this highly complex project.”
Sharon Liu, Sub Agent at Balfour Beatty VINCI added: “The success of this box push relied heavily on both the engineering expertise and the efficiency of the equipment used. Altrad RMD Kwikform’s ability to deliver and manage the right equipment on a tight schedule, and their hands-on expertise, directly contributed to the success of the offline build and completion of the bridge slide backfill, influencing reopening of the road 30 hours ahead of schedule.”
“Working with the team at Altrad RMD Kwikform has been a pleasure. Our collaboration has been highly rewarding and has allowed us to successfully tackle complex challenges using innovative technical solutions, demonstrating the strength of our partnership and shared commitment to excellence.”
For more on Altrad RMD Kwikform, please visit www.rmdkwikform.com.
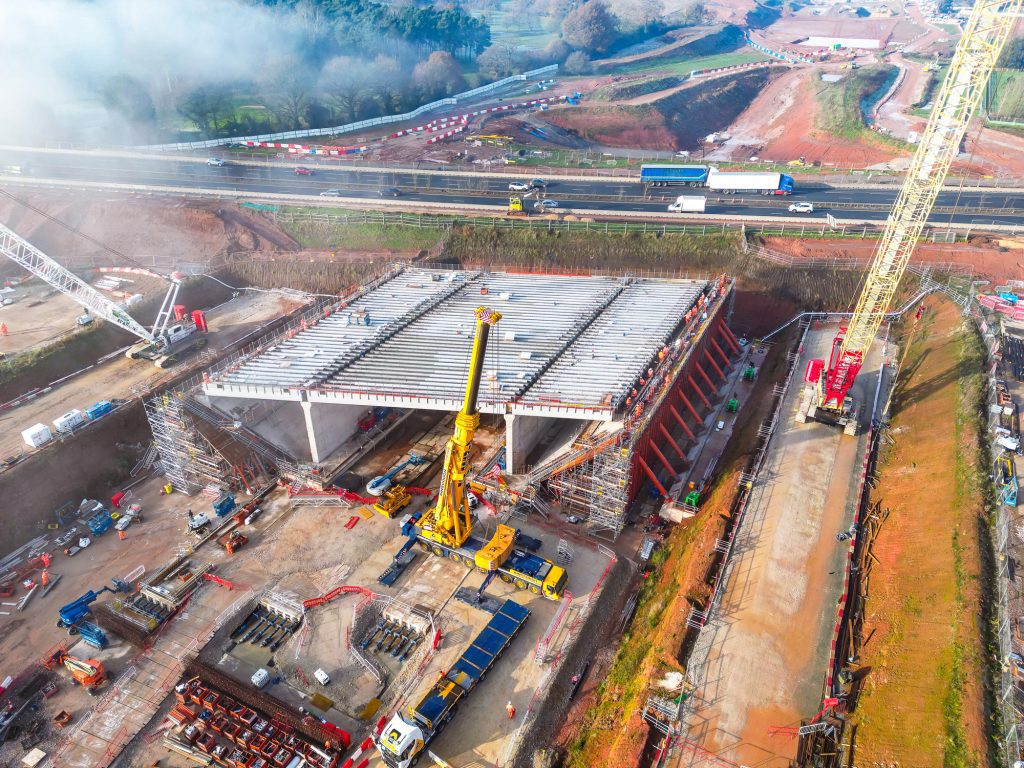
Building, Design & Construction Magazine | The Choice of Industry Professionals