Bespoke excavation support solution from Groundforce Shorco helps East Rudland Construction.
Groundforce Shorco has provided specialist shoring equipment and design services for a complex excavation at a new housing development in North Yorkshire.
Contractor East Rudland Construction is carrying out the groundworks and civil engineering for the project, which involves the construction of 25 executive-style homes for developer Gem Construction Ltd.
One of East Rudland Construction’s tasks is the installation of a stormwater attenuation tank – a large underground reservoir to store rainwater and prevent surcharges into the nearby watercourses during periods of high rainfall.
The attenuation tank is a large void made using ACO’s StormBrixx HD900 geocellular blocks encased within an impermeable 1mm LLDPE/HDPE membrane.
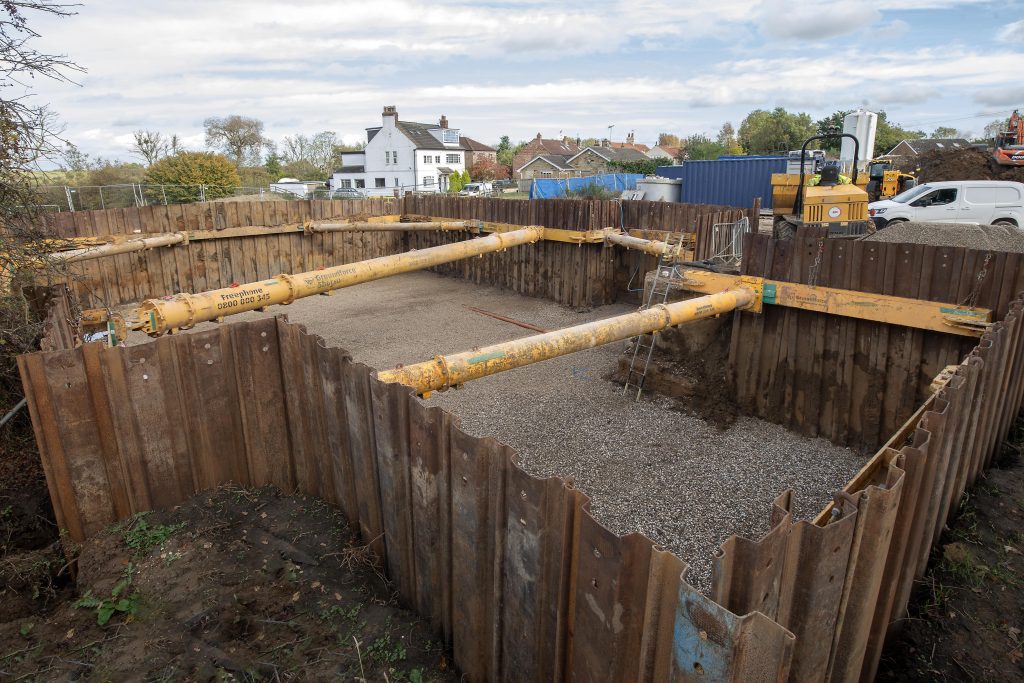
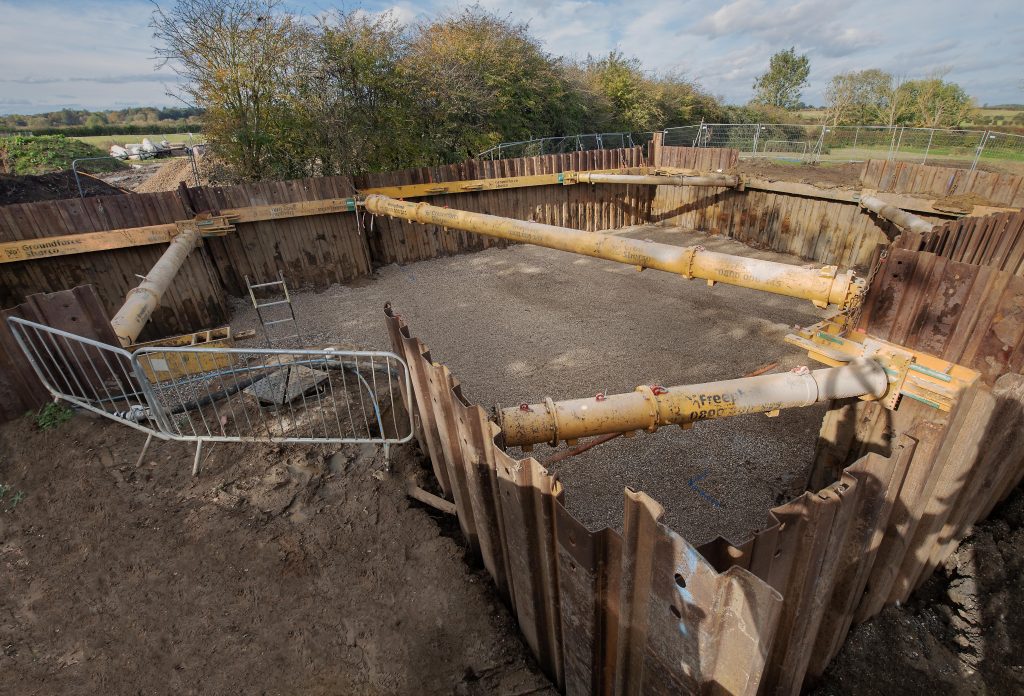
Ground conditions on the site at Ulleskelf, near Tadcaster, are very challenging, says Steve Hayhurst, co-owner of East Rudland Construction.
“The site has a very high water table which raises the risk of the groundwater floating the tank and lifting it out of the ground,” he explains.
To prevent this happening, it was necessary to increase the depth of soil on top of the buried tank to hold it down.
“We couldn’t bury the tank any deeper, so instead we had to change its shape,” says Steve.
The tank was therefore redesigned, reducing its height by approximately one metre to allow a greater depth of fill on top. However, to maintain the same volume, the tank’s footprint had to be extended outwards to make up for the reduced depth.
The redesigned tank now covered an area of approximately 25m x 17m but due to the space restrictions of the site layout, it has to be a complex and irregular shape in order to occupy the space available.
To support the sides of the excavation, East Rudland Construction called in Groundforce Shorco.
“I’ve worked with Groundforce for over 20 years and I know them well. I knew they would have the right solution,” says Steve.
East Rudland Construction gave Groundforce Shorco the dimensions of the tank and Groundforce Shorco designed the temporary works solution, employing its modular Mega Brace system to support a steel sheet-piled retaining wall and braced with MP50 and MP150 hydraulic props.
The Mega Brace system is designed so that beams of virtually any length can be assembled using the modular sections in different combinations. However, this excavation’s complex shape meant that certain lengths of the perimeter frame were little more than one metre in length – too short even for Groundforce Shorco’s standard equipment.
Groundforce Shorco therefore provided bespoke lengths, modified to suit the application. To support the sides of the 3m-deep excavation, they supplied 170 lightweight GFI interlocking steel piles, each 6m in length.
Larssen piles would normally have been the default option, but site constraints ruled this out, explains Steve.
“Larssen piles are strong, heavy-duty sheet piles with a deep U-shaped cross section and we would have struggled to remove them after completion of the excavation without resorting to a larger excavator.
“We couldn’t use a heavy excavator without risking damage to the installed tank. There was also very limited space in which to manoeuvre a large machine. Therefore, we had to find an alternative.
“We used about 170 6m-long GFIs to stop water flow into the excavation. These are interlocking sheets offering a lighter option than the Larssen piles. They are much easier to remove from the ground.”
To permit the lightweight GFI piles to be driven to the correct depth, East Rudland Construction pre-augured the perimeter of the excavation, loosening the soil and allowing insertion of the sheet piles.
Another requirement was to carry out extensive frame-to-sheet-pile welding to prevent lateral movement of the frame. The irregular shape of the excavation meant there were numerous short lengths of frame subject to relatively high end-loads. Welding the frame to the sheet piles helped ensure rigidity.
“We did all the installation ourselves, using our own plant and equipment, but we relied heavily on the design and technical support provided by Groundforce Shorco,” says Steve.
“I kept in regular contact with their area manager Trevor Kendrick – whom I have known for years – and he was absolutely fantastic,” Steve continues. “The job started out as a potential headache but together we found a solution and made it work smoothly.”
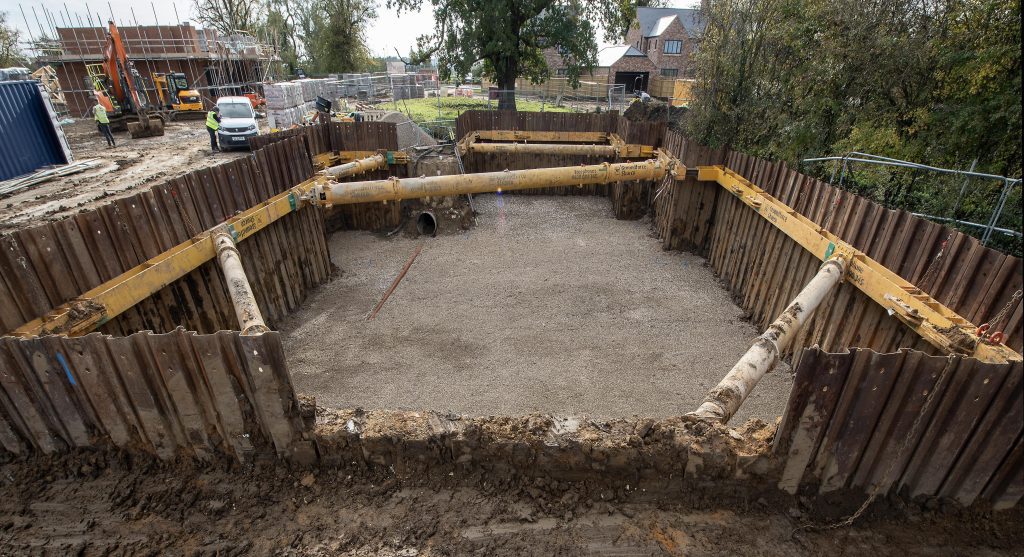
Building, Design & Construction Magazine | The Choice of Industry Professionals