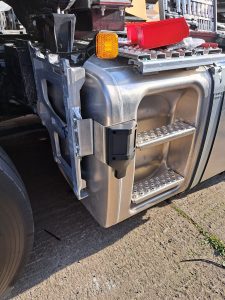
New collision prediction system launched by Brigade Electronics
Brigade Electronics has launched Radar Predict – its latest innovative side Blind Spot Information System (BSIS) collision prediction safety technology specifically designed to protect cyclists from incidents with HGVs. Even before its launch, this product was already receiving positive feedback during customer trials and has earned expert recognition, being honoured as the ‘Most Innovative Product of the Year’ at the Motor Transport Awards. Utilising artificial intelligence (AI), Radar Predict alerts the driver about potential collisions by analysing data such as the speed and direction of the vehicle, and cyclists nearby. The system uses its specially designed algorithm to alert drivers when an impact with a cyclist is likely. Incidents involving large vehicles, such as HGVs, are far more likely to prove fatal than those involving a car. Many of the collisions between cyclists and HGVs occur because the driver has limited ‘direct vision’ from their cab (the ability to see what is outside the vehicle without using indirect aids, such as mirrors or cameras). Radar Predict supports HGV driver visibility via a single dual-radar unit, which is fitted to the nearside of the vehicle to provide complete side coverage, including the trailer unit. A trailer discovery mode will detect whether the vehicle is fitted with a trailer and prevents the articulation from causing false alerts. The driver is alerted only if a cyclist enters the detection zone and poses a potential collision risk. The system issues differentiated visual and audible alerts based on the time to collision, providing an initial notification upon detection and escalating to a more urgent warning if it predicts an imminent collision. Radar Predict’s key features include: Thierry Bourgeay, Senior Product Manager at Brigade Electronics, said: “Radar Predict has been specifically developed to address the issues caused by blind spots for HGV drivers when manoeuvring in close proximity to cyclists. The system ensures full coverage down the nearside of the vehicle, including the trailer, and greatly reduces false alerts for drivers as it will only activate when a collision is likely. Additionally, Radar Predict will automatically activate when the vehicle is turning, so no indicator selection is required by the driver.” To find out more about Brigade’s Radar Predict and its portfolio of vehicle safety solutions, please visit https://brigade-electronics.com/products/radar-obstacle-detection/radar-predict/. Building, Design & Construction Magazine | The Choice of Industry Professionals
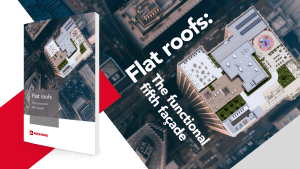
ROCKWOOL® launches whitepaper to support fire safety of multifunctional roofs
New whitepaper explores how to identify and mitigate fire risks for flat roofs functioning as additional social or practical spaces of a building, including for solar installations The role of the roof in modern building design has expanded significantly in recent years. Now ROCKWOOL® has published a whitepaper aimed at helping specifiers and roof contractors to consider and plan for possible fire risks arising from flat roofs being used as multifunctional spaces for a variety of social and practical applications, highlighting, for example, the increasing number of solar energy installations. The Flat roofs: The functional fifth façade paper explores the fire safety implications of modern multifunctional roofs and discusses best practices for identifying and mitigating the risks. It also explains the role of the guidance provided in approved documents, including Approved Document B (ADB) for fire safety, and examines potential limitations of such advice for non-standard flat roof circumstances and scenarios. The whitepaper can be downloaded at https://rockwool.link/ffpr “While the use of flat roofs as functional spaces is not a new concept, the practice has become more and more popular in recent years, especially in increasingly crowded urban areas,” explains Lisa Stephens, Product Manager – Building Envelope, ROCKWOOL UK. “Now, flat roofs don’t just house plant and building services but energy efficiency infrastructure and social spaces too.” With the increasing complexity of the flat roof space in mind, this whitepaper addresses the risks associated with social and commercial uses of flat roofs, considering implications such as greater footfall and the impact of penetrations from building services and cabling on compartmentation and fire resistance. With the market for solar energy growing rapidly in the UK and Europe, Flat roofs: The functional fifth façade also places a specific focus on the lack of dedicated guidance for solar panels despite evidence that their presence may increase fire risk. “The information in the whitepaper will help those involved in the design and installation of flat roofs to make responsible choices when selecting materials to enable a modern flat roof to be multifunctional, safe and long-lasting,” says Lisa Stephens. “It offers practical advice to simplify specification whilst going above and beyond legislative requirements.” For more information and to download the whitepaper go to: https://rockwool.link/ffpr Building, Design & Construction Magazine | The Choice of Industry Professionals
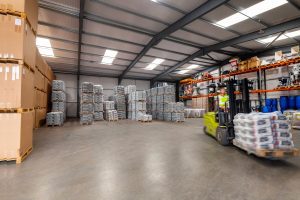
First UK Mapecrete jointless floor system installed in the UK
Mapei UK’s first Mapecrete jointless floor system has been installed at P1 The Plasterers One Stop Shop & Plastering Superstore, in Cheltenham. The seamless finish was installed over the 440m2 floor area, which will be used as new warehouse space. Concrete was supplied by Flowmix and pumped by Max-Pump. Suitable for all environments – from commercial and industrial to residential – the Mapecrete system provided benefits including enhanced durability, reduced maintenance and a fast-track installation. Fibre-reinforced concrete (FRC) jointless slabs represent a significant advancement in concrete technology, offering numerous benefits over traditional reinforced concrete (RC) slabs. The Mapecrete FRC jointless system is based on a shrinkage compensated concrete technology where contraction is compensated by restrained expansion through structural reinforcement. The modular system consists of four Mapei products which work in synergy to create a jointless finish: they include Dynamon XTend W300 N, Mapecure SRA 25, Expancrete, Mapefiber ST42 and Mapecure E30. Whilst RC slabs are jointed to assist in controlling cracking, FRC jointless slabs contain fibres within the concrete mix to enhance performance and reduce cracking and spalling. The slab’s increased durability provides increased load-bearing capacity and greater ability to withstand heavy loads and high traffic. As well as reduced maintenance, further cost savings result from reduced downtime and repairs, and from a less labour-intensive installation. The jointless system is also more resistant to environmental factors, such as freeze-thaw cycles. “The Mapecrete system provided a multitude of installation and performance benefits, as well as a safer working environment. The FRC jointless slab system eliminates the need for steel mesh and greatly reduces labour days. Installation was also far easier, compared to traditional RC slabs, creating a seamless floor. Further down the line, we’ve also eliminated the issues that can arise from having joints every 5-6 linear metres. It’s a fabulous innovation and we’re delighted with the finish achieved in the superstore, ”commented Andrew Hill, Managing Director at Plastering Superstore. For more information about Mapei products and applications, please contact: info@mapei.co.uk or visit www.mapei.co.uk Building, Design & Construction Magazine | The Choice of Industry Professionals
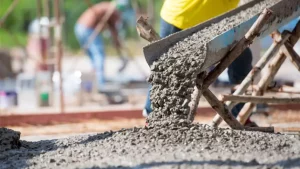
Leading materials scientists call for wider adoption of low carbon cement technology to slash emissions by 2030
A group of leading materials scientists has called for the cement and construction sectors to urgently adopt low carbon cement technologies to radically reduce CO2 emissions. Cement is responsible for almost 8% of global CO2 emissions – more than shipping, aviation and long-haul trucking combined. Convening at a symposium in Paris hosted by Ecocem, Europe’s leading low carbon cement technology business, the scientists shared latest research papers on low carbon cement technologies and focused on ideas and materials which can accelerate decarbonisation of the sector. Global demand for cement is expected to grow in the coming decades. The WEF (World Economic Forum) amongst others, predicts that demand for cement could increase by up to 45% by 2050. The scientists said that “effective solutions are needed urgently if the construction sector as a whole is to decarbonise in line with a 1.5°C trajectory.” The scientists concluded that adopting the latest developments in low carbon cement technology is the quickest and most scalable way to make substantial emission reductions across the cement and construction industries by the end of 2030. The cement industry has long been considered hard-to-abate due to the use of clinker, the primary ingredient in cement, which is produced by heating limestone at extremely high temperatures. While low carbon cements already exist, the challenge to date has been to scale them. During the two-day event, the scientists reviewed new evidence on the use of alternative materials that reduce the volume of clinker, replacing it with a wide variety of locally sourced filler materials and natural Supplementary Cementitious Materials (SCMs). In a call to action, the eleven scientists, representing a range of institutions from around the world (a full list of the academics and their institutions can be found in the editors’ notes), said that “it is no longer possible to say that we lack the technology or that the costs are prohibitive.” Materials science has advanced to a point where rapid decarbonisation of cement without excessive cost is now a reality. At the forefront of these advances is ACT, Ecocem’s latest technology which can reduce emissions from cement by 70% while ensuring that the concrete produced retains its workability, strength and durability, with the added benefit of using substantially less water and energy. ACT is globally scalable due to its compatibility with a wide variety of locally sourced filler materials and natural SCMs and can be produced in existing cement plants with minimal additional investment. Mohend Chaouche, CNRS Research Director, ENS Paris-Saclay, Laboratoire Mécanique de Paris-Saclay, and Director of the CNRS-Ecocem joint laboratory MC²E, said: “The urgency of developing and deploying low-carbon cements is no longer up for debate. ENS Paris-Saclay is very proud to have contributed to the birth of the ACT technology, which reduces the carbon footprint of cement by 70%. The intense years of R&D have paid off.” Martin Cyr, University Professor at University of Toulouse, Laboratory of Materials and Sustainability of Constructions and Director of the joint LMDC-Ecocem ORISON laboratory, added: “Low-clinker technologies developed and validated in the laboratory can now be deployed without scientific or technical barriers. These technologies represent a significant step towards reducing CO2 emissions, ahead of the industry’s 2030 roadmap.” Donal O’Riain, Founder and Managing Director of Ecocem, concluded: “The widespread adoption of ACT technology will enable the cement industry to drastically reduce its global emissions rapidly and cost effectively. Policymakers must speed up regulatory enablement to ensure low carbon cement technologies can be used more widely and that the investment made available to accelerate industrial deployment of these new technologies. I urge the cement sector to move quickly. We have opportunity to be the first industrial sector to comply with a 50% reduction in emissions by the end of 2030. The technology is available to decarbonise the whole cement sector in line with limiting global warming to 1.5°C. It is now our responsibility to ensure this happens.” Building, Design & Construction Magazine | The Choice of Industry Professionals
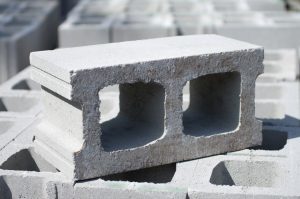
Paving the Way: Carbon Sequestration in Concrete to Mitigate Environmental Impact
By Dr Gareth Davies, Carbon Reduction Scientist, PhD & Dr Luan Ho, Carbon Reduction Scientist, PhD – Tunley Environmental Concrete, the most extensively used manmade material worldwide, carries a significant environmental burden, contributing to 8% of anthropogenic GHG emissions. With a staggering 30 Gt produced annually, the material consumption is over 3.5 tonnes of concrete per person annually. The majority of the emissions (88.5%) emanate from cement production, the essential ingredient in concrete. Carbon sequestration in concrete presents a promising avenue to offset these emissions. This process, often referred to as carbonation or mineralisation, essentially reverses the initial cement production steps, where carbon dioxide is detached from calcium carbonate (limestone). Controlled carbonation of cementitious material, although first proposed in the 1970s, is recently garnering increased attention due to its substantial potential to mitigate against the colossal emissions from concrete production. However, carbonation is not without its challenges. Uncontrolled, it can lead to the corrosion of steel in reinforced concrete and the formation of harmful compounds, jeopardising the structural integrity of buildings. Yet, advancements in controlled carbonation methodologies have demonstrated the potential to not only sequester carbon dioxide but also enhance the properties of concrete. One such method involves utilising accelerated carbonation chambers to carbonate pre-cast materials, offering control over essential parameters such as CO2 concentration, humidity, and temperature. This impacts the rate and depth of carbonation, with the formation of calcium carbonate in the exterior pores blocking further carbonation. Emerging techniques explore embedding CO2-rich materials within the concrete mixture. A notable investigation by MIT researchers examined incorporating sodium bicarbonate, which dissolves and releases CO2 during curing. This innovative method not only sequesters carbon but also addresses the detrimental impacts of late-stage carbonation, such as shrinkage and crack formation. Furthermore, the possibility of reusing carbonated Recycled Concrete Aggregate (RCA) from construction and demolition waste, which amounts to around 3 billion tonnes annually, offers an additional layer of environmental benefits. Although using RCA poses challenges such as increased costs and micro-cracking, controlled carbonation mitigates these issues and allows for a decrease in both water absorption and leaching instability. These advances in carbonation technology could potentially sequester 2 Gt of CO2 annually if implemented at scale, significantly reducing the environmental footprint of concrete production. When combined with the predicted 50% reduction from electrification, emissions could be curtailed to just 32.7% of the current levels. However, the journey towards sustainable concrete production is multifaceted and complex. As researchers and engineers continue to explore the potential of carbon sequestration in concrete, the combination of controlled carbonation and the incorporation of CO2-releasing materials represents a leap forward in our quest to mitigate the environmental impact of this ubiquitous material. In conclusion, the path to mitigating the environmental challenges posed by concrete production lies in innovative solutions such as carbon sequestration. By acting as a carbon sink, concrete has the potential to offset a significant portion of the emissions generated during its manufacturing stage. The incorporation of carbonated end-of-life concrete as filler material further underscores the potential of this material to contribute to a more sustainable future. References [1] S. A. Miller and F. C. Moore, “Climate and health damages from global concrete production,” Nat Clim Chang, vol. 10, no. 5, pp. 439–443, May 2020, doi: 10.1038/s41558-020-0733-0. [2] A. Petek Gursel, E. Masanet, A. Horvath, and A. Stadel, “Life-cycle inventory analysis of concrete production: A critical review,” Cem Concr Compos, vol. 51, pp. 38–48, 2014, doi: 10.1016/j.cemconcomp.2014.03.005. [3] P. C. Aïtcin, “Portland cement,” in Science and Technology of Concrete Admixtures, Elsevier Inc., 2016, pp. 27–51. doi: 10.1016/B978-0-08-100693-1.00003-5. [4] M. Stefanoni, U. Angst, and B. Elsener, “Corrosion rate of carbon steel in carbonated concrete – A critical review,” Cement and Concrete Research, vol. 103. Elsevier Ltd, pp. 35–48, Jan. 01, 2018. doi: 10.1016/j.cemconres.2017.10.007. [5] L. Qin, X. Gao, and T. Chen, “Influence of mineral admixtures on carbonation curing of cement paste,” Constr Build Mater, vol. 212, pp. 653–662, Jul. 2019, doi: 10.1016/j.conbuildmat.2019.04.033. [6] S. Hussain, D. Bhunia, and S. B. Singh, “Comparative study of accelerated carbonation of plain cement and fly-ash concrete,” Journal of Building Engineering, vol. 10, pp. 26–31, Mar. 2017, doi: 10.1016/j.jobe.2017.02.001. [7] B. Šavija and M. Luković, “Carbonation of cement paste: Understanding, challenges, and opportunities,” Construction and Building Materials, vol. 117. Elsevier Ltd, pp. 285–301, Aug. 01, 2016. doi: 10.1016/j.conbuildmat.2016.04.138. [8] N. Lippiatt, T. C. Ling, and S. Y. Pan, “Towards carbon-neutral construction materials: Carbonation of cement-based materials and the future perspective,” Journal of Building Engineering, vol. 28. Elsevier Ltd, Mar. 01, 2020. doi: 10.1016/j.jobe.2019.101062. [9] Z. Xu et al., “Effects of temperature, humidity and CO2 concentration on carbonation of cement-based materials: A review,” Construction and Building Materials, vol. 346. Elsevier Ltd, Sep. 05, 2022. doi: 10.1016/j.conbuildmat.2022.128399. [10] J. Liu et al., “Carbonated concrete brick capturing carbon dioxide from cement kiln exhaust gas,” Case Studies in Construction Materials, vol. 17, Dec. 2022, doi: 10.1016/j.cscm.2022.e01474. [11] Z. Li, Z. He, and X. Chen, “The performance of carbonation-cured concrete,” Materials, vol. 12, no. 22, Nov. 2019, doi: 10.3390/ma12223729. [12] D. Stefaniuk, M. Hajduczek, J. C. Weaver, F. J. Ulm, and A. Masic, “Cementing CO2 into C-S-H: A step toward concrete carbon neutrality,” PNAS Nexus, vol. 2, no. 3, Mar. 2023, doi: 10.1093/pnasnexus/pgad052. [13] Y. Pu et al., “Accelerated carbonation technology for enhanced treatment of recycled concrete aggregates: A state-of-the-art review,” Constr Build Mater, vol. 282, May 2021, doi: 10.1016/j.conbuildmat.2021.122671. [14] D. Xuan, B. Zhan, and C. S. Poon, “Assessment of mechanical properties of concrete incorporating carbonated recycled concrete aggregates,” Cem Concr Compos, vol. 65, pp. 67–74, Jan. 2016, doi: 10.1016/j.cemconcomp.2015.10.018. [15] T. Kikuchi and Y. Kuroda, “Carbon Dioxide Uptake in Demolished and Crushed Concrete,” 2011. [16] Z. Guo, A. Tu, C. Chen, and D. E. Lehman, “Mechanical properties, durability, and life-cycle assessment of concrete building blocks incorporating recycled concrete aggregates,” J Clean Prod, vol. 199, pp. 136–149, Oct. 2018, doi: 10.1016/j.jclepro.2018.07.069. https://www.tunley-environmental.com/ Building, Design & Construction Magazine | The Choice of Industry Professionals
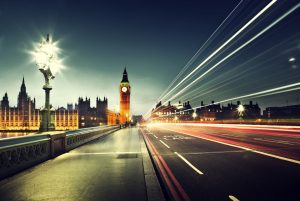
How do you rewire a city? Balfour Beatty Shows us
A team of experts, innovative plant and equipment, 200km of cables and a 32.5km underground tunnel network, 40 metres beneath the city of London. Find out how we’re rewiring London’s electrical transmission system to keep Londoners connected to a safe and reliable electricity supply. #Expertengineers #BuildingNewFutures Building, Design & Construction Magazine | The Choice of Industry Professionals