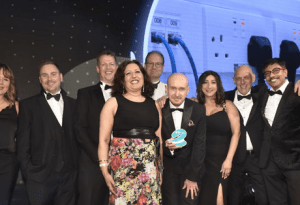
Game-changing energy monitoring sockets named physical technology of the year
Honeywell’s Connected Power, one of the first fully integrated commercial solutions for monitoring and controlling plug-in power, has been named a winner at this year’s Energy Awards in the Physical Technology category. Coming at a time when energy consumption is among the top priorities for businesses across the UK, the Connected Power solution is designed to give building and energy managers the capability to remotely monitor, control and automate sockets across their premises. Making this switch can help save energy consumed by plug-in devices, in the United States on average in a minimally code-compliant office building, plug loads may account for 25% or less of total energy consumption and in high efficiency buildings, plug loads may account for more than 50% of the total energy consumption[i]. “Celebrating excellence in ways to reduce energy consumption, winning the award for Physical Technology of the Year at the Energy Awards is not just a testament to the technology itself, but to the impact this solution can have on one of the biggest challenges faced by UK businesses today,” says Steve Kenny, vice president and general manager, Honeywell Building Management Systems. “One of the most overlooked factors during efficiency improvement plans is small power usage. It’s overlooked because there has historically been a lack of visibility into how much energy is consumed by plug-in devices, and a lack of control of unnecessary consumption. Connected Power has been designed to overcome that and give businesses the tools they need to fully manage their plug-in power usage. It’s the first time this has been possible for UK companies. “Businesses are continuously trying to minimise their energy consumption and costs. So, it’s imperative that they look towards longer term solutions that provide ongoing opportunities for improvement. There can be hundreds of electrical devices in any commercial building and taking charge of that energy usage becomes extremely important as energy prices shock businesses into reassessing their power consumption.” Connected Power, developed by Honeywell’s MK Electric and Trend brands, launched in Spring 2023 following a test period that saw it installed at several sites across the UK. Energy efficiency was seen in several different building locations by powering equipment only when needed, with evident energy savings once scheduling was applied through the Connected Power solution. The Energy Awards celebrates the energy industry’s innovations and achievements in best practice, business excellence, customer service and industry collaboration and brings together more than 600 key decision makers from across the industry. Building, Design & Construction Magazine | The Choice of Industry Professionals
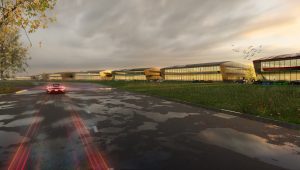
Green light for Bicester Motion’s new £50 million Innovation Quarter to boost future pioneering mobility discovery
Detailed designs for seven new, prestigious HQ buildings which total 212,030 sq ft (19,698 sq m) and will be built at Bicester Motion’s new Innovation Quarter have been given the green light by Cherwell District Council. Bicester Motion is a 444-acre former RAF site acquired in 2013 in the heart of Motorsport Valley in Oxfordshire and home to more than 50 industry-leading businesses in all forms of mobility technology, past, present and future. Companies include NEOM McLaren Electric Racing, Motorsport UK, the governing body of British Motorsport, PhysicsX, Polestar’s UK HQ, and record-breaking synthetic fuel manufacturer Zero. Bicester Motion’s masterplan has been adopted and supported by Cherwell District Council with consent for one million sq ft (92,903 sq m) across its Heritage, Innovation, Experience and Wilderness Quarters and hotel. Bicester Motion submitted the detailed designs for its Innovation Quarter which will see a £50 million investment to deliver seven new HQ buildings which will be suitable for R&D technology, light assembly and product showcase and will range from 7,500 sq ft (697 sq m) to 60,000 sq ft (5,574 sq m). Phase 1 will deliver the first two HQ buildings and construction is due to start in Spring 2024 and target practice completion in Q1 2025. The carbon-efficient buildings will target BREEAM Excellent certification and EPC A rating. They will be prepared for solar PV technology creation and include dedicated ecology and biodiversity areas, green space amenities for staff health and wellbeing, and more than 100 bicycle parking spaces. Bicester Motion has also committed to significant infrastructure improvements including cycle and connectivity to Bicester North station and the surrounding area. Future occupiers will have access to Bicester Motion’s annual programme of events, and vehicle tracks and active airfield for both testing and demonstration. Dan Geoghegan, chief executive, Bicester Motion said: “We acquired the abandoned former WW2 RAF base in 2013 and since then have been creating the pre-eminent destination to experience the full breadth of automotive and aviation engineering, events, culture, design, research, and manufacture. “Now home to more than 500 highly skilled jobs, from engineers carefully restoring the classics in our workshops to acclaimed national headquarters at the cutting edge of innovation, together with our amenities, track and aerodrome facilities, not to mention our regular fun-fuelled events with footfall of 200,000+ visitors per year, we’re a unique and thriving community. “Since 2013 our purpose has been to create a place unlike any other to promote the development of pioneering technology especially, as you would expect, mobility and transportation. This sector is booming, with both start-ups and mainstream manufacturers racing to develop new technologies and transportation options. “Today’s planning news is a significant milestone in our evolution to invest in and deliver our new Innovation Quarter. We are resolute in our focus to deliver a unique home and space for future innovating mobility pioneers, putting Bicester on the technology map, and boosting the economy in creating jobs both through construction and specifically within the future companies which join our thriving estate.” Sebastian Johnson, head of innovation and inward investment, OxLEP said: “Bicester Motion is a nationally and internationally significant centre for future mobility innovation and emerging technologies. OxLEP supports and recognises the talent and expertise and research capabilities at Bicester Motion and the opportunities to grow the cluster of companies and the innovation that will impact on net zero and sustainability in future mobility. Alongside the innovation is an impressive and well-developed skills offer for young and emerging talent and an amazing visitor experience attracting people nationally and internationally.” George Brown, associate, Bidwells added: “Bicester Motion’s firm commitment to deliver this new Innovation Quarter and specifically the first two high spec HQ buildings is welcome news for the market and those pioneering future mobility companies needing stand-out space in an unrivalled motorsport-focused place. Bicester Motion should be credited for raising the bar in Oxfordshire through their innovative masterplanning and building design and investing and delivering to meet occupier demand.” Acting on behalf of Bicester Motion are 3D Reid, IKS Consulting Ltd, Hydrock, Mcgregor Smith, Ecology Solutions, Edgars, Worlledge Associates, and MODE. Commercial leasing agents are Adalta Real and Bidwells. Building, Design & Construction Magazine | The Choice of Industry Professionals
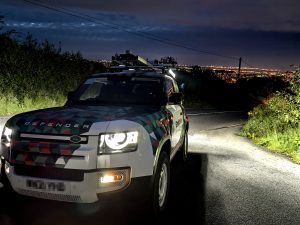
Murphy Geospatial Launches Geodrive: A New Mobile Mapping Solution
Geospatial leader Murphy Geospatial, is launching a bespoke mobile-mapping technology to support faster and more accurate geospatial data capture in the built environment. The eye-catching vehicle, called GeoDrive, can easily capture up to 100km of geospatial survey data in just one day. In a world where the sustainability and maintenance of infrastructure assets are of utmost importance, Murphy Geospatial plays a crucial role by providing accurate geospatial data. This data empowers asset owners to make well-informed decisions, ensuring the longevity and efficiency of their infrastructure investments. The new service, aimed at large projects within construction, infrastructure, and energy and utility sectors, will gather significant volumes of data on large geographical areas at higher speeds and lower cost compared with traditional data capture methods. How does GeoDrive work? GeoDrive uses high precision scanners and a multi-camera system to collect sub centimetre accuracy information and is mounted on top of a uniquely branded vehicle or it can be fixed to trains or other moving vehicles. The extremely precise data captured by this new service is also thanks to Murphy Geospatial’s emphasis on quality control of workflows, managed by well-trained staff with their own expertise in geomatics, allowing them to focus on even the most trivial details of a project. Murphy Geospatial Associate Director Maciej Targosz commented: “This new solution is going to make a huge difference to clients gathering information in relation to large-scale projects. The speed at which GeoDrive can capture data will save clients both time and money when compared with the method of taking a total station along the length of a site. “GeoDrive also supports cost-effectiveness of projects as it means more-detailed methods of surveying are deployed where they are needed, having already gathered base data for a project’s entirety. This supports informed decision making and optimised resource allocation. “For clients managing projects that cover highways, it will also eliminate the need for traffic management. GeoDrive will also help clients mitigate project delays, public inquiries, protests, and production bottlenecks. “We’re looking forward to supporting clients access and analyse the quality data at speed that GeoDrive can gather, and will be offering this new service throughout Ireland, UK, and Europe.” Building, Design & Construction Magazine | The Choice of Industry Professionals
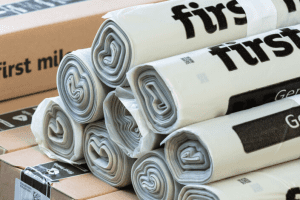
First Mile celebrates five years of tackling contamination and providing end-destination reassurance through QR codes on 40 million recycling sacks
This Recycle Week (16-20 October) First Mile is proud to celebrate the five-year anniversary of its RecycleID initiative – incorporating QR codes on 40 million recycling sacks across the UK and working together with its customers to tackle recycling contamination, boost recycling rates and reduce businesses’ carbon footprint. Each First Mile customer has a personalised QR code, which is printed on its recycling sacks and scanned on both drop off and collection by First Mile. Customers can also scan their QR code using First Mile’s Smart Cities App to access their account and information. This is particularly useful for businesses with complex waste management needs, such as multi-tenanted housing and shopping centres. This technology has revolutionised the recycling process, enabling customers to access real-time data about the recycling’s end location, ensuring complete transparency and accountability. It also gives customers the opportunity to access their individual recycling statistics, enabling accurate carbon data and recycling reporting. As each code is specific to a customer, the technology also means that any contamination issues – such as food waste being put in a dry mixed recycling sack – can be identified. First Mile’s app sends a picture which is then emailed to the customer, alongside advice on how to resolve the issue. Since 2018, First Mile has sent 200,000 contamination emails to customers, working with them to educate and support them in ensuring that the right items are being placed in the right sacks, fostering a sense of collective responsibility towards the environment. First Mile founder and CEO, Bruce Bratley, says: “Since its inception, First Mile has been committed to promoting environmental sustainability and the introduction of QR codes on recycling bags in 2018 marked a significant milestone in our journey towards a greener future. These QR codes have empowered our customers to gain valuable insights in their business recycling activity and they have embraced this technology wholeheartedly, with around 40 million bags being scanned and tracked to date. This achievement is a testament to our shared commitment to sustainability and our customers’ dedication to making a positive impact on the environment.” QR codes form part of wider focus for First Mile to empower businesses to improve their sustainability through data and education on their waste management, offering free waste audits, workshops and webinars, and help in setting up their recycling stations. For more information visit thefirstmile.co.uk Building, Design & Construction Magazine | The Choice of Industry Professionals
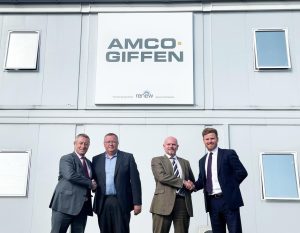
hyperTunnel and AmcoGiffen sign UK exclusive distributor agreement
hyperTunnel, a technology company innovating underground construction methods, has signed an exclusive distributor agreement (EDA) with AmcoGiffen for the application of its technologies and systems in the UK rail sector. Under the EDA, AmcoGiffen will have exclusive rights to use hyperTunnel technology – including digital twins, robotics, 3D printing and digital underground surveying, supported by AI and VR – for all enhancements, repair, rehabilitation and monitoring of underground spaces, slopes and track bed infrastructure, including stabilisation and water management. hyperTunnel launched exclusive distributor licensing agreements in 2022. EDAs provide engineering contractors the opportunity to differentiate themselves by offering hyperTunnel technologies exclusively within certain applications, sectors and territories. The solutions, which enable the highly efficient building, enlarging, repairing and monitoring of underground structures, allow license holders to increase their operating margins and grow market share while reducing environmental impact. “Construction and maintenance companies are consumed day-to-day with delivering against contracts on tight margins,” commented Steve Jordan, co-CEO of hyperTunnel. “Yet, at the same time, they need to develop sustainable innovations that will take their businesses forward, potentially leading the next technological leap. “Through this EDA, AmcoGiffen can tap into our approaches and methodologies, R&D investment and industry experts from day one. It is a win-win – our products are commercially ready and in AmcoGiffen we have a partner that will allow us to get robots into the ground quickly and prove the hyperTunnel method in an unforgiving commercial and operational environment.” Owned by Renew Holdings Plc and publicly listed on the London Stock Exchange, AmcoGiffen specialises in the design and delivery of innovative and complex multi-disciplinary engineering, construction and maintenance services across the transport, energy and environmental sectors. Dave Thomas, Operations Director at AmcoGiffen added: “We are convinced that the future of maintaining underground structures lies in robotics and automation. AmcoGiffen is equipped and ready to partner with hyperTunnel to pioneer its approaches in the UK rail sector while being fully aware of the challenges that may lie ahead for an early adopter of such exciting technology. This exclusive contract represents a significant business opportunity for AmcoGiffen and reflects our long-term ambition to lead innovation in the UK rail sector.” To discover more about hyperTunnel and becoming a technology distributor, contact distributor@hypertunnel.co.uk. Building, Design & Construction Magazine | The Choice of Industry Professionals
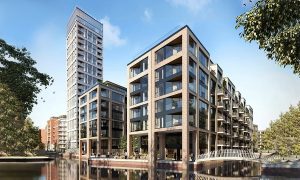
Smart water technology for West London Canalside living
I wanted to share a new case study on behalf of RWC, who have recently supported the renovation of a high rise development in Chelsea. High-rise living forms a critical part of the solution to the growing demand for homes across the UK. To ensure the success of these buildings, specifiers and consultants must select systems that align with modern construction methods and meet the demands of residents today and in the future. Water management is a particular consideration here, ensuring every dwelling has a reliable, consistent and safe supply of water, as well as contributing to broader sustainability efforts by supporting responsible usage and greater water savings. The Chelsea Creek development, which utilises solutions from RWC’s Reliance Valves range, demonstrates how water management systems can successfully control and monitor water supply to large numbers of apartments, while also mitigating against leaks to protect occupants and buildings from costly water damage. Smart water technology for West London Canalside living Water is at the heart of the canalside Chelsea Creek development in London, but to ensure a safe and reliable supply of water to 147 individual apartments, an innovative water management system was required. To efficiently control and monitor water supply, as well as mitigate against leaks, solutions from Reliance Valves were selected. Located in the heart of Chelsea, Chelsea Creek is the exciting transformation of a 7.8 acre brownfield site into a new development based around waterside living. Featuring stunning landscapes of tree-lined avenues and meandering waterways, the neighbourhood perfectly combines tranquillity and metropolitan living and brings a sophisticated European aesthetic to West London. Comprising of 1, 2 and 3-bedroom apartments, the development would require intricate plumbing pipework – not just due to the nature of high-rise buildings, but also to achieve the high specification ambitions of the project. To strike this balance, building services contractor, Briggs & Forrester Living, needed an innovative water management system to control and monitor water supply, mitigate the risk of leaks and the costly effects of water damage. Specifying for success The Tenant Valve Plus and MultiSafe Leak Detector Control Valve by Reliance Valves were specified by Briggs & Forrester to help fulfil their client’s risk management plans and leak mitigation aims. Saving time and space by combining several functions into one compact unit, the Tenant Valve [EM1] [AJ2] includes a BS1010-approved stop valve, a pressure reducing valve and strainer, double check valve, dual-reading pressure gauge, and a connection point for an optional water meter. The combination valve effectively controls and monitors water supply to individual dwellings, while its single-piece design significantly reduces the number of leak points compared to a traditional chain of individual valves. It was also more cost-effective and easier to install and maintain, all of which were crucial to Briggs & Forrester’s building design. Reliance Valves’ MultiSafe Leak Detector Control Valve was also selected to provide an intelligent leak detection system that continuously measures the flow rate, pressure, temperature, and the hardness of water. In addition to automatically shutting off water in the event of a leak or an abnormal water pattern, the system sends an alert to the concierge as well as the occupants, via a free app. Mark Durham, Project Manager at Briggs & Forrester Living, said: “Reliance Valves’ MultiSafe leak detection system was selected following trials with several manufacturers on performance, connectivity, control versatility and end-user functions for leak protection and water usage. Our client’s risk management plan and their aim for innovative leak mitigation was of paramount importance for protecting the project during the fit-out phases and was a prerequisite to be “online” prior to the testing and filling stages. “The system’s wireless connectivity, web-based platform and mobile app is ideal for real-time app alerts and email notifications, which performs superbly, fully satisfying the requirement of directive for effective leak mitigation. The leak detection valve coupled with the multifunctional space-saving Tenant Valves assembly, were the ideal paring in our aim to reduce risk of possible leaks.” As the demand for housing continues to soar across the UK, high-rise developments are becoming increasingly common additions to city skylines. While the trend to build upwards maximises limited inner-city space and delivers appealing living spaces for residents, it does pose challenges to specifiers and contractors, including around water supply, control and sustainability. By specifying systems from Reliance Valves, Briggs & Forrester were able to install high-quality and cost-effective systems on the Chelsea Creek development. In practice, this means water supply can be controlled and monitored, maximising efficiency and strengthening sustainability efforts, as well as meeting their client’s requirements for risk management through an innovative leak detection solution. To find out more, visit www.reliancevalves.com/gb/en Building, Design & Construction Magazine | The Choice of Industry Professionals