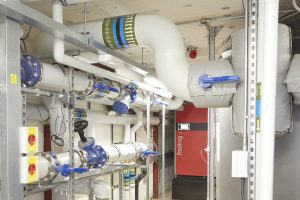
Energy efficient heating for sustainable living in Sheffield
Taconova installs 229 Heat Interface Units in new residential development A new £37m residential development in Sheffield is benefiting from sustainable and efficient heating, courtesy of Taconova’s market-leading Heat Interface Units (HIUs). The Ironworks: Redefining Urban Living Situated on Scotland Street, the Ironworks has been developed by Rise Homes and brings much-needed quality rented accommodation to Sheffield. Building work began in January 2021 on the site of the former Queens Hotel, and in September 2023, Rise Homes and Taconova were joined by the Mayor of Sheffield to open the new 12-storey Ironworks building. Inside The Ironworks This development encompasses 229 furnished apartments, comprising 144 one-bedroom, 80 two-bedroom, and 5 two-bedroom duplex units. A focus on sustainability is evident, with each unit connected to the building’s communal biomass boiler-powered heating system. The Heating System Water heated by the basement biomass boiler circulates through the building’s risers and into the Heat Interface Unit (HIU) in each of the 229 apartments. The HIUs ensure efficient and consistent heating and domestic hot water provision, maintaining optimal temperature and flow for the residents. TacoTherm H 3000E: The Core of Heating Each flat features a TacoTherm H 3000E Heat Interface Unit. This HIU is an electronically controlled, compact, and connection-ready all-in-one unit that offers indirect heat transfer for heating and domestic hot water. The 229 HIUs had to be supplied, installed, and commissioned within a three-month window. Taconova delivered 50 HIUs per week, and the contractor installed them in the utility cupboard of each apartment. The TacoTherm H 3000E has been designed specifically for multi-storey residential buildings and provides an operating pressure of 6 bar. It has an operating temperature of 90°C and generates hot water temperatures of up to 60°C. The TacoTherm H 3000E is highly efficient and has an overall Volume Weighted Average Return Temperature (VWART) figure of 26, making it a market leader – as independently tested by BESA (Building Engineering Services Association). More Than Just Hardware One of the standout benefits of opting for an electronically controlled HIU is the availability of data. The initial specification for this project was for Heat Interface Units only. However, the TacoTherm H 3000E offers much more than just hardware. The HIU has a smart meter which enables remote monitoring and analysis of heat consumption. The meter gathers information from across the network, from the plant room to the HIU. With this data, the system’s efficiency can be tracked, and improvements may be made based on the information. Likewise, if there are any inefficiencies or faults, these can be identified, pinpointed, and rectified quickly. The Ironworks management chose to also install the suggested smart heating controls and offer the controls to the residents through a smartphone or tablet app. These controls mean heating can be switched on or off remotely, potentially saving energy. Rigorous Quality Assurance Acceptance Test: Good Performance Before the project was completed, Taconova conducted testing on each HIU. This service formed part of the Taconova’s commitment to ensuring the HIUs function to the correct specification. The testing analysed the operating pressure, temperature, and hot water temperatures in each apartment and measured the overall efficiency of the heating system during a 48-hour period. The results were then measured against set parameters. After Taconova’s engineers had completed the adjustments and remedial work, the tests were conducted again. Improvements were evident and the scheme was performing according to the set design parameters and achieved overall network compliance. On-going Monitoring for Sustainable Living As part of its commitment to customer service and sustainability, Taconova will continue to monitor and improve the heating system for the lifetime of the scheme. It is well documented that the efficiency of a newly built property drops substantially after the first 12-month operation, so it’s important to monitor the efficiency of the whole heating system beyond the initial year. The ongoing monitoring provides complete oversight of the whole system, not just the HIUs. Therefore, it is possible to recommend improvements to ensure that the network remains at the optimum efficiency level. For example, adjusting the plant room temperature during the summer and winter can optimise the system and improve efficiency. As well as providing constant monitoring and improvement suggestions, Taconova will also support Ironworks with annual servicing of the HIUs, as part of the service level agreement. A Greener Future Exciting plans for the future reveal that things could get even greener if the Ironworks development can join the Sheffield City District Heating Network. This district heating network is one of the largest city heat networks in the UK and currently supplies 2,800 homes and 140 commercial buildings, saving 21,000 tonnes of CO2 emissions annually. The focal point of the network is the city’s incinerator which burns 120,000 tonnes of municipal waste each year, producing up to 60MW of thermal energy. With an expansion and improvement to the network, it is hoped that the Ironworks will be able to benefit from the waste heat generated from Sheffield’s incinerator. Joining the network will mean the Ironworks can replace the biomass boiler and utilise waste heat from the network, further enhancing the building’s green credentials. The indirect TacoTherm H 3000E HIU is future-ready and will seamlessly transition to the heat network and deliver efficient heating to the residents in the building. Thanks to the HIU’s pre-fitted heat meter, the residents’ heat consumption will be calculated based on what they use. Switching to the heat network will mean a lower heating tariff compared to the biomass boiler, so residents’ energy bills will also be lower. Innovative heating solutions like Taconova’s indirect TacoTherm H 3000E HIUs are part of the company’s mission to offer reliable, low-maintenance, and highly efficient heating solutions that save customers time, effort, and money. To find out more, please visit: www.taconova.com. Building, Design & Construction Magazine | The Choice of Industry Professionals
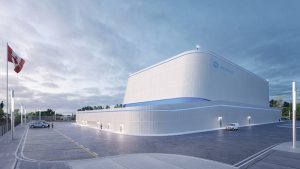
Nuclear regulator begins GE Hitachi new reactor assessment
The Office for Nuclear Regulation, along with the Environment Agency and Natural Resources Wales, has started a two-step Generic Design Assessment (GDA) for GE Hitachi’s BWRX300 reactor. The Department for Energy Security and Net Zero made the request to the regulators following its readiness review of the GE Hitachi application. This review concluded that the design is ready to enter the GDA process. The GDA will look to actively explore opportunities to maximise the value of international regulatory collaboration and identify efficiencies in processes. Two step GDA explained Building, Design & Construction Magazine | The Choice of Industry Professionals
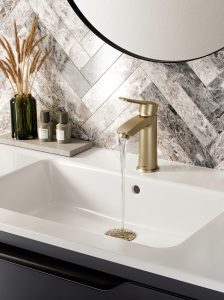
Bristan unveils range of water-saving products in new ESG pledge
The UK’s market leader for taps and showers, Bristan, has released its new Environmental, Social Responsibility and Governance (ESG) report which shines a spotlight on its water-saving products – including its new Eco Start technology. The report outlines the organisation’s commitment to sustainability with one of the key focuses being the innovation of energy and water-saving products. Recently, Bristan has introduced innovative Eco Start technology on bathroom taps, which saves energy by having cold water as the default central start position of the tap handle. This means that hot water is only activated when the tap lever is moved from the central position, so your boiler is not unnecessarily fired up. Also featured in its comprehensive water-efficient portfolio are pre-fitted flow limiters, infrared taps that automatically turn off when not in use, and BREEAM-certified self-closing ‘push button’ taps. As with all Bristan products, the water-efficient range is rigorously tested to comply with key regulations and industry requirements, so that specifiers can have complete confidence when working on a project. Plus, Bristan’s UKAS-accredited lab recycles 90% of the water used to carry out endurance testing of our products, further demonstrating its commitment to sustainability. Craig Rendall, Bristan Group Specification Director, comments: “Whether working in the housebuilding or commercial sector, we understand that sustainability targets are a key consideration when specifying for a project. That’s why we’re proud to offer our range of water-saving products, to make it a trouble-free decision for specifiers every time.” The ESG report also details the wider sustainability commitments of the wider Bristan Group. As a zero-to-landfill company, it has extensive measures in place to ensure that approximately 295 tonnes of waste produced each year are recycled, reused or repurposed. What’s more, Bristan Group is in the process of having 1666 solar panels installed on the roof of its Tamworth-based head office, which is expected to generate 600kw/hour of electricity to support business operations and will equate to a CO2 saving up to 111,292 kgs per annum. With a clear roadmap of sustainability initiatives behind them, Bristan Group’s products can be bought with confidence and trusted to help reduce the UK’s overall carbon footprint — one tap or shower at a time. Bristan Group’s Environmental, Social and Governance Report can be found here. To discover Bristan’s range of water-saving products, visit the website here. Building, Design & Construction Magazine | The Choice of Industry Professionals
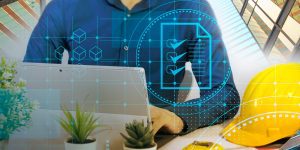
BuildData predicts information will be king in 2024
New building regulations with requirements for effective digital information management for compliance, will be a driver for tech buying decisions this year. 2024 is the year when the Building Safety Act (BSA) will come into full force, following the first provisions rolled out in 2022 and 2023. The BSA mandates digital building information and safety cases, as well as a golden thread of information, for higher-risk buildings (HRBs). Therefore, prioritising information will be high on the industry agenda in 2024, all delivered by technology to ensure effective information management. But the BSA is not the only regulation with a requirement for digital information competency for compliance. Photographic evidence is now mandatory to comply with Part L under Building Regulation 40. And more legislation and standards are set to follow with digital information requirements, such as the Future Homes and Building Standard, where information will be needed to support building design, construction, and management. With the evolution of the construction and property industry, there is no time like the present to get information, processes, and the technology in order to deliver better information and, therefore, building outcomes. This emphasis on digital data and information to better manage buildings throughout their lifecycle — from planning all the way through to operations and maintenance — is not necessarily new concept. However, it is only recently that the focus has shifted across the construction and building management sectors to prioritise its importance, driven by new and updated standards and legislation. That is why BuildData Group, with its brands Zutec, Createmaster and Createmaster Information Management, believe information will be king, and should be given the same attention as the physical asset. Emma Hooper, Head of the Research Institute at the BuildData Group, states: “As an industry we need to shift our thinking about information and data, as it lies at the core of regulation, digital transformation, and the way a built asset is designed, constructed, and operated. Essentially, we need information management to enable us to find, share, understand, use, and query what we do in an easy, digestible, and decisive way, while ensuring quality and trust. It is the linchpin of everything we do across the built environment, and without it we cannot operate effectively. In our minds, information and good information management should be as important as the built asset itself.” So why will information be king in 2024? Keeping people and our environment safe, keeping well-maintained buildings The construction, built environment and digital worlds are constantly evolving. Therefore, ensuring the right stakeholders have the right information at the right time to make decisions, control risk, keep buildings well maintained and people and our environment safe is critical. Information is only useful if it is available, accessible, easily discoverable, and understandable and a golden thread of information is now legal requirement of duty holders and accountable persons of occupied higher-risk buildings under the BSA. This is to ensure that everyone involved in building safety management and maintenance, whether directly or indirectly, has access to key details that can help identify, assess, and mitigate risks. When the right information is delivered at the right time — whether it’s to facilities management, the fire department, or tenants — more informed decisions can be made more quickly. With the right technology platform and stack in place building information can be surfaced, managed, and shared, and kept up to date to meet compliance. Being able to integrate with other systems means all building information can be managed in one place, supporting the journey to a golden thread of information, and making information king. Quality over quantity There is a plethora of information required to meet building regulation compliance. From fire and emergency files to structural information, health and safety files, as well as operations & maintenance manuals and completion certificates – all this information should have a purpose. Without purpose it is useless. This means information must be high quality to the degree that it performs that purpose, is usable and enables the outcomes it is intended for. There are several criteria used to measure information quality, including accuracy, completeness, consistency, timeliness, and validity. All of this is important because it ensures that the information used to make key decisions is reliable. It is therefore critical to ensure information quality throughout the information management process, as without this it can lead to ineffective decision-making, construction and operational errors, and ultimately put lives and our built environment at risk. There is also a direct correlation between information quality and information compliance. Lost, inaccessible or inaccurate information can cause huge issues, and one of the reasons we have building standards and regulations in place. With a consistent structure, schemas, and workflows, as well as standardised forms, templates, and checklists, one platform for information management can ensure that data meets quality standards. And, when construction quality is a huge factor in delivering buildings that meet standards and compliance, then the information quality related to that building should be equally as good. Another reason to make information king. Right data in, is right information out Leading on from good quality information, is the right data going into the information management system or platform. The right information in, results in the right information coming out to drive the decision-making process, while controlling risks and reputation. Many systems today have AI or machine learning functionality to help surface the right information. However, the main obstacle for AI is poor quality data, which directly impacts the reliability of the AI model in place. When in investing in technology, it is also crucial that the data going into a platform is accurate, representative, and of high quality. When information comes from so many sources, the construction and property industry has always struggled to collect documents and data, structure this information and label it correctly, all while maintaining quality. Companies like Createmaster, can help collect, tag, and review the information for quality, and store in one platform (like Zutec), with dashboards to manage that information to ensure data governance and robust and accurate information,
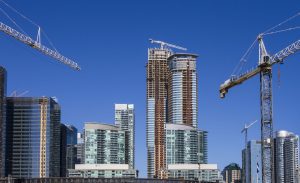
Sherwin-Williams points to technology to address new legislation
Using technology to provide information required under the new Building Safety Act 2022 – which has been enforceable since October 1st – can help relieve the pressure on suppliers who are responsible for submitting the data, says Bob Glendenning, Fire Design Engineering Manager of Sherwin-Williams Protective & Marine Coatings. The Building Safety Act is designed to take forward a fundamental reform of the building safety system and address the issues identified by Dame Judith Hackitt in her independent review, Building a Safer Future. The Government stated that the Act would deliver ‘the biggest changes to building safety for nearly 40 years and make residents safer in their homes’ and named the Health and Safety Executive (HSE) as the new Building Safety Regulator to oversee the safety and standards of all buildings. In doing so, the legislation has also brought challenges for those in the complex supply chain who are required to provide specific information at each key stage which should be digitally stored and available for the lifetime of the building, described as The Golden Thread of information. For the protection of structural steel with intumescent coatings, the different parts of the engineering community and the supply chain also need to understand more detail of certain stages or Gateways as they are described under the terms of the act. Structural engineers, designers and specifiers will be more concerned with the requirements under gateways one covering the planning stage and parts of gateway two dealing with building control approval. Applicators will need to understand parts of gateway two on building control and gateway three covering safety information. Fabricators will need to understand the wider picture across all three gateways. Overhaul in existing regulations The intention is to ensure that the right people have the right information at the right time to ensure buildings are safe and building safety risks are managed throughout the building’s lifecycle. For the construction industry, and related specialisms such as Passive Fire Protection, this means an overhaul in existing regulations, with new guidance in how higher risk buildings should be designed, constructed and managed to ensure that those who use them are safe and feel safe. These buildings are defined as being a minimum of 18 metres or seven storeys in height and comprise of at least two domestic premises. Resource is limited in many organisations, so how are suppliers to approach these challenging requirements without cutting corners? At Sherwin-Williams, we use our years of expertise along with the appropriate technology. This technology allows us to understand what is required at the start of the process working in collaboration with our customers. To this end, we have invested in Building Information Modelling (BIM) process and technology for many years and also partner with leading global software developers including Trimble. Such systems allow for data transfer and make storage much simpler. They are future-proofed and permanent. They also provide important information and documentation required under the new act in the digital format required. Benefits to the process are apparent for main contractors, architects, structural engineers, steel fabricators and site inspectors. Accessing a BIM model collaboratively aids efficiency and versatility, particularly on projects with global players, where project team members may reside in different geographies around the world. All can access the model over the internet and collaborate using cloud-sharing technology. We have been committed to this approach for some years and, to this end, we have developed our own proprietary software called the FIRETEX Design Estimator 2.0 (FDE). The software offers calculated solutions for the safe protection of structural steelwork framing elements, and embraces BIM with an integrated plugin tool allowing 3D modelling data to be directly linked into the software. Manging the whole process This offers the capability of providing calculations for coatings thicknesses of all shapes and sizes of steel sections, fire engineering, and in the case of cellular beams, allows for any configuration of web apertures to be seamlessly incorporated and the fire protection specification passed back into the model. For the steelwork fabricator, the approach with BIM means they can manage the whole process from concept to design through to delivery of materials on site including the off-site applied fire protection. The same principle could also be adopted for use with on-site applied fire protection, offering advantages to the main contractor and eventually to the owner-operator. FIRETEX embodied carbon values, using our third-party certificated EPDs, are also stored within the 3D model. Once the fire protection properties have been passed back into the BIM model, future interested stakeholders can access any of that information to manage many areas such as inspection and onward building fire maintenance. Even fire and rescue services could create strategies using this data. There are real savings in efficiencies, time and cost here, with the added benefits for the users in the longer term. One example of these efficiencies can be seen in the huge time savings in a recent project where all the floor plates were unique. That in-turn made all the floor beams – which were cellular beams – unique designs in themselves so this was a huge design undertaking. The BIM workflow is a ‘push-pull’ system. We added missing dry film thickness design properties to the steelwork 3D model using the FDE. All of the coatings properties were then stored on every piece in the model, including the EPD values, meaning we had access to this information to share with other parties for the lifetime of the building. The newest development released very recently includes the ability to synchronise any optimised steel profiles back into the model. After synchronisation the end-user can then produce documents, drawings, labels, barcodes and any other relevant documentation. This is fast and accurate and provides certainty for the purposes of the new Building Safety Act. New powers of enforcement This information is critical and the technology enables us to be accurate from the outset for our customers in the interests of safety. As a reminder as to why this information is so
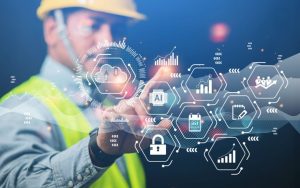
IS CONSTRUCTION’S DIGITAL REVOLUTION UNDERWAY?
NBS’ 2023 Digital Construction Report shows strong appetite for emerging tech NBS, the platform for connected construction information, has revealed the results of its 2023 Digital Construction Report. Focusing on emerging tech and the industry’s approach to digital transformation, the report offers a snapshot of industry professionals’ various views and evolving opinions. One of the most hotly debated topics from this year’s study concerns the industry’s rate of tech adoption and whether it now excels in terms of digital expertise. Despite an overall rise in the use of digital technologies, nearly half (47%) are concerned the industry is behind the times. Moreover, 36% of respondents said they worry that they will be left behind when it comes to digital know-how. However, around a quarter (26%) believe this is an outdated view and is no longer the case, and that construction has finally found its ‘digital feet’. With such a divided split, it could suggest that ‘digitisation’ is more prominent in some areas of construction than others. Further wins for digital twins and off-site NBS also found that the use of digital twins has increased by 50% since 2021 from 16% to 25%. What’s more, just over half (55%) of those that use digital twins, do so to mirror construction from other projects and to create an ‘as-built model’. This could be evidence that building safety and efficiency is now taking precedence. Figures relating to the number of projects using elements of off-site construction also showed an uptick. Over half of professionals (57%) had been involved in a project that used MMC in the past twelve months. In 2021, this figure was hovering at around 50% so an upward trend is taking place. Suppliers were the most likely (70%) followed by contractors (63%) and consultants (58%). The increased uptake of off-site construction has also been reflected in project data from Glenigan. Its industry intelligence shows a value-adjusted percentage of 11% of new-build projects using MMC during the first nine months of 2023. Glenigan predicts further growth to this figure over the next few years, with nearly 9% of new-build projects securing detailed planning approval during the first nine months of 2023 involving an off-site element. Becoming Immersed The study also flagged a growing appetite for the use of immersive technologies, such as AR (Augmented Reality), VR (Virtual Reality), and MR (Mixed-Reality) which are playing an increasingly important role. More than one in three professionals (36%) are already using this type of technology and a further one in five (20%) plans to within the next three years. Overwhelmingly, its main use is for stakeholder engagement (74%), where upcoming or ongoing projects can be digitally generated to present detailed plans. However, for two in three users (62%), immersive tech offers a way to visualise design interfaces, so they can better understand how construction projects fit within existing surroundings. Just over a third (35%) use it for marketing purposes, particularly amongst suppliers (67%) who recognise its value when selling products and systems. Machine learning Interest in AI (Artificial Intelligence) and machine learning has also seen a sharp rise within the past year following the launch of ChatGPT and other algorithm-based language models. Looking back to 2020, two in five (38%) said they were unsure if their organisation was using it, of those who did, just 9% were using AI. Although the use of AI in construction is yet to take its grip (43% said they have no plans to use it), signs of early adopters are already visible. More than one in five (22%) have already adopted AI, and a similar number (20%) said they will do so within a year. Head in the clouds Eight in ten now also use a form of cloud computing as part of their daily workflow. While mainly in the form of storage, including Google Drive, OnePoll, DropBox, etc, the study revealed that over seven in ten use it to share documents and information with clients. Three-quarters (75%) also use it to collaborate with other team members, particularly on 3D models and specifications. Given the industry’s push towards the Golden Thread and focus on digital information management, it shows that the sector is making the essential investment to increase efficiency and reduce risk in the built environment. A point of interest within the report was that despite overall growth in the use of tech, opinions on whether the industry is still lagging behind others remain divided. Nearly half (47%) are still concerned the industry is behind the times when it comes to the adoption of digital technologies, but over a quarter believe it’s no longer the case. Speaking on this year’s report, David Bain, Research Manager at NBS, said: “It’s clear from the results that construction has ramped up digital adoption in recent years and is a far stride from where it was three years ago. “Looking ahead, it will be fascinating to see next year’s report as 2024 is shaping up to be big on AI and machine learning.” Russell Haworth, NBS CEO, added: “Looking at the evidence, we can see that construction is shaking off old and tired misconceptions and now relies on all manner of digital skills to produce building excellence. That said, there are still some areas for improvement and no doubt next year will bring further leaps in tech know-how and application.” Click here for the full report. 723 construction professionals took part in this year’s Digital Construction Survey, which included views from architects/engineers and other consultants, contractors, clients, and suppliers in the UK and beyond. Previously known as the NBS BIM Report, the study is a benchmark for changing attitudes towards tech adoption and new technologies.