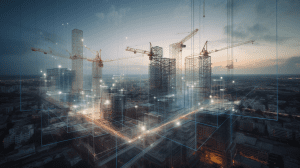
‘There’s still work to do’: Study finds alarming ‘knowledge gaps’ on Building Safety Act responsibilities
NBS’ 2024 Building Safety Survey reveals industry still ‘unsure’ of high-rise legislation… A new study by NBS, the UK’s leading specification platform, has found that nearly half of specifiers are still unsure of the responsibilities attached to the Building Safety Act 2022, a worrying sign that a high number of ‘knowledge gaps’ persist within the industry. Findings from NBS’ Building Safety Survey showed that half of respondents were either unsure or had no idea of duty holder responsibilities for Higher Risk Buildings (HRB). What’s more, just 12% felt ‘very clear’, demonstrating that more industry-wide training is needed in the run-up to the 1st of April 2024, when the grace period around the Act ends. The figures could be seen as concerning given that around two in three respondents (66%) have past experience working on HRB projects (although these are more likely to be suppliers and contractors than architects). Delving deeper, nearly half (44%) of respondents are unsure or have no idea what steps to take within the new building safety regime. These figures come nearly a year after the BSA was passed in Parliament, first introduced back in July 2021. Surprisingly, the figures are almost identical to that seen in NBS’ 2022 report (43%), showing that understanding of legislation has seen little improvement in this area. Worrying still, was that attitudes towards the Golden Thread and the crucial role it plays within HRBs appeared lax. As well as providing a continuous flow of information throughout the entire lifecycle of a building, it ensures all relevant safety-related information is readily accessible and up to date. However, only around half of respondents (45%) were clear as to how they would manage building information to realise the Golden Thread and just one in ten had a solid plan in place. Again, these are similar to 2022 figures, where in fact, more people felt confident managing building information than they did in 2023 (+2%). This is despite the increasing number of advanced construction-tech platforms designed to help specifiers capture each decision-making stage to form the Golden Thread. However, despite the obvious informational disparities, the study did highlight some more reassuring stats, particularly around third-party testing and the information being supplied by manufacturers – which is increasing safety within specifications. The report flagged that nine out of ten suppliers now provide ‘clear and accurate’ building product data in a digital format. At least eight out of ten also provide third-party certification with their products and have robust internal sign-off and version control processes. Commenting on the survey’s results, David Bain, NBS’ Research Manager, said, “Consistency is the backbone of progress and the stakes have never been higher when it comes to HRBs. These studies serve to highlight ‘trouble spots’ and importantly, offer an understanding of how to take the industry forward as a whole.” Russell Haworth, Chief Executive Officer UKI at Byggfakta Group, NBS’ parent company, said “At our Construction Leaders’ Summit last October, Dame Judith Hackitt told the audience, in no uncertain terms, that regulatory change is coming, and it’s unstoppable, so the construction industry needs to be fully prepared. Fast-forward to April 2024, and our research shows many specifiers are struggling to get to grips with the requirements, and this needs to be resolved. All designers must have the correct approach to specifications if the industry is to raise the bar on building safety. This includes getting to grips with the ‘nitty gritty’ of the BSA if they want to operate in the new regulatory landscape.” To download NBS’ Building Safety Whitepaper, click here. To find out more about NBS, its services, and expertise, click here. Building, Design & Construction Magazine | The Choice of Industry Professionals
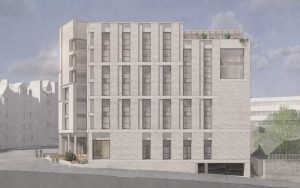
Reinforced concrete makes the grade for student accommodation
With the demand for purposed-built student accommodation (PBSA) predicted to soar, a new report from the British Association of Reinforcement (BAR) explains ‘Why Reinforced Concrete Makes the Grade for Student Accommodation’. The latest student population data from the Higher Education Statistics Agency (HESA) show that for the 2021/22 academic year the number of full-time students rose by 4%, to over 2.26 million. Meanwhile, the number of international students from India and China has more than offset the fall in EU students in the wake of Brexit as the UK continues to be one of the key global destinations for students looking to study abroad. Between 2019/20 and 2021/22, the number of full-time international students rose by 117,500. The increase in student applications and numbers is set against a growing shortage in student accommodation. This shortage is being exacerbated by the falling supply of Houses of Multiple Occupation (HMOs) resulting from landlord regulation and tax changes. Since 2017 there have been over 300,00 buy-to-let mortgage redemptions which has reduced the number of 5-plus bedroom rental properties by 31% since 2019. The reduced supply of private landlord HMO’s is increasing the demand for PBSA particularly from overseas students. To address the disparity between supply and demand more PBSA needs to be constructed. Reinforced concrete offers a wide range of inherent and free performance benefits that are particularly suited to building student accommodation. These include built-in fire resistance, significant noise and vibration reduction, thermal mass for energy efficiency and long-term robust finishes. Steve Elliott BAR Chairman explained: “Reinforced concrete offers a number of unrivalled performance benefits that means it should be awarded a 1st class degree with honours for the construction of PBSA. These concrete benefits are inherent and built-in. There is no need for any additional products, finishes or chemical preservatives. This significantly reduces both initial capital and the ongoing maintenance costs.” With regards to long-term sustainability reinforced concrete again gets top marks. The issue of sustainability is important for PBSAs. Students are some of the most motivated in tackling climate change reducing CO2 emissions. Elliott said: “Admittedly, the use of concrete construction raises questions concerning the level of construction embodied CO2 when compared to other structural materials such as timber. However, if you have to mechanical ventilate and cool a lightweight timber or steel building then the resulting operational CO2 emissions, over the lifetime of the building, will far outweigh any initial construction embodied CO2 savings.” He continued: “Similarly, concrete does need additional fire proofing, sound insulation, wall finishes, flood resilient materials. All of these additional materials have an additional CO2 impact for their manufacture and installation. With concrete construction all of the above performance benefits are provided without any further environmental or financial cost”. He added that all the reinforcement made in the UK is made from recycled scrap steel using the Electric Arc Furnace (EAF) process which consumes only a third of the embodied energy, emits one sixth of the CO2 and produces approximately half the amount of co-products (waste) compared with the traditional BOS blast furnace steelmaking process. Reinforcing steel can be recovered, recycled and re-used at the end of a building or structure’s service life. To download a copy of ‘Why Reinforced Concrete Makes the Grade for Student Accommodation’ visit: www.uk-bar.org/publications Building, Design & Construction Magazine | The Choice of Industry Professionals
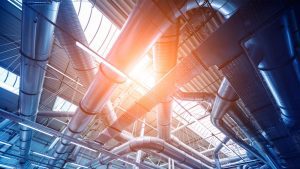
CIBSE and DESNZ partner to make CP1 (2020) Free-to-All: A landmark move for UK Heat Network Standards
The Chartered Institution of Building Services Engineers (CIBSE) and the Department for Energy Security and Net Zero (DESNZ) announce their partnership to make CP1 (2020), the recognised Code of Practice for heat networks in the UK, accessible to all, free of charge. CP1 (2020), a publication produced by CIBSE, serves as a comprehensive guide offering technical guidance and establishing voluntary minimum standards for UK heat networks. Widely acknowledged as the go-to resource in the industry, CP1 (2020) has garnered widespread acceptance and support since its last update in 2020. It has been utilised by industry professionals as a vital technical reference and by developers to set standards for their new heat networks. Previously available exclusively to CIBSE members, CP1 (2020) is now accessible to all stakeholders, thanks to the generous funding provided by DESNZ. This collaborative effort aims to democratise access to crucial information outlined in CP1 (2020) and facilitate better preparedness for the forthcoming heat network regulations in 2025. CIBSE and DESNZ are not only removing the paywall but also actively collaborating to update the voluntary Code of Practice throughout 2024. This joint initiative ensures continuous alignment with the evolving regulatory landscape, particularly with the Heat Network Technical Assurance Scheme (HNTAS) standards under development. The next version of CP1 is scheduled to be freely available for download in 2025. CIBSE’s Technical Director, Dr Anastasia Mylona said about this partnership: “We’re excited to partner with DESNZ to offer CP1 (2020) free to all stakeholders. This vital guide sets standards for UK heat networks, promoting industry preparedness for upcoming regulations. It reflects our commitment to advancing best practices and sustainability.” For more information and to access CP1 (2020), please visit CP1 Heat networks: Code of Practice for the UK (2020) (pdf) | CIBSE Building, Design & Construction Magazine | The Choice of Industry Professionals
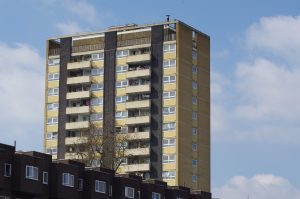
Fire services in England have received just 30 percent of building plans since introduction of fire safety regulations update
New research by signage specialists, FASTSIGNS UK, has revealed fire and rescue services in England have, on average, received just 30 percent of high-rise building plans and 21 percent of external wall plans, required under the UK Government’s updated fire safety regulations. The updated regulation, Fire Safety (England) Regulation 2022, which came into play on 23 January 2023, made it a legal requirement for responsible persons of high-rise residential buildings of 7 storeys or more to provide local fire and rescue services with appropriate safety information, including up-to-date building and external wall plans. The research sheds light on the percentage of building plans and external wall plans submitted by qualifying high-rises across England since the introduction of the regulation, using data from a series of Freedom of Information Requests (FOI) made to 18 fire services – compared against data for the number of high-rises each service serves. Cheshire Fire and Rescue Service has the highest percentage of submissions for both criteria received, with 88 percent of up-to-date building plans submitted and 88 percent of up-to-date wall plans submitted. Only Oxfordshire Fire & Rescue Service has received more for building plans, comparably though, no external wall plans were received. Nottingham Fire & Rescue Service received only 6 percent of building plans and just 4 percent of external wall plans for high-rises in its area. The regulation was introduced in response to the Grenfell Tower tragedy in July 2017, where on-site emergency response teams reported that navigating such a complex residential building, without clear directional signage, prevented them from carrying out their duties safely. Consequently, a recommendation was made that signage, building and external wall plans in multi-occupied high-rise residential buildings should now be a legal requirement. Using the information, fire services would be able to plan an effective response in case of an emergency in the future, while also enabling residents to exit following clear, signposted instructions. The breakdown of county-specific findings includes: Fire and Safety Service % of those who have submitted external wall plans % of those who have submitted building plans Essex County Fire & Rescue Service 0% 27% Hampshire & Isle of Wight Fire & Rescue Service 0% 13% Oxfordshire Fire & Rescue Service 0% 100% Northamptonshire Fire & Rescue Service 0% 9% Nottinghamshire Fire & Rescue Service 4% 6% Surrey Fire & Rescue Service 10% 0% Kent Fire & Rescue Service 12% 18% Leicestershire Fire & Rescue Service 13% 11% Dorset & Wiltshire Fire & Rescue Service 14% 6% Greater Manchester Fire & Rescue Service 15% 8% Norfolk Fire Service 17% 55% Devon & Somerset Fire & Rescue Service 17% 25% Lancashire Fire & Rescue Service 20% 9% Royal Berkshire Fire & Rescue Service 24% 18% Tyne & Wear Metropolitan Fire Brigade 40% 59% Staffordshire Fire & Rescue Service 53% 47% Cambridgeshire Fire & Rescue Service 56% 52% Cheshire Fire & Rescue Service 88% 88% National Average 21% 31% John Davies, managing director of FASTSIGNS UK, added: “No matter what the industry, health and safety signage is fundamental in minimising risks and supporting people’s wellbeing as well as being crucial in the event of an emergency. “With certified safety and directional signage, both residents and response teams will be able to clearly navigate high-rise buildings when an incident occurs. We work closely with our customers around England so that any buildings that fall under this criteria meet these new requirements.” For more information on FASTSIGNS UK, visit: www.fastsigns.co.uk Building, Design & Construction Magazine | The Choice of Industry Professionals
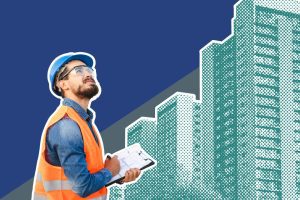
Building Safety Act: Is the industry ready?
New research by NBS finds half of industry professionals still unclear on duty holder responsibilities for higher-risk buildings As the six-month transition period for Higher Risk Buildings (HRBs) comes to a close, new research from NBS, the UK’s leading specification platform, shows the industry is still struggling to achieve a consensus on the scope and requirements of the Building Safety Act 2022. The report reveals half of industry professionals remain unclear on the responsibilities of duty holders for the gateways defined for higher-risk buildings. What’s more, only 20 percent of respondents feel confident they are ‘very clear’ on the differences in responsibilities, if the project is defined as a higher-risk building. This is a deeply concerning figure. What the research makes clear, is a greater effort is urgently required to ensure a universal understanding of the BSA’s role; particularly, clarifying the lines of responsibility and duties, whilst improving the consistency and quality of documentation and record keeping on construction projects. Commenting on the findings, Russell Haworth, Chief Executive Officer UKI at Byggfakta Group, NBS’ parent company, said “At our Construction Leaders’ Summit last October, Dame Judith Hackitt told the audience, in no uncertain terms, that regulatory change is coming, and it’s unstoppable, so the construction industry needs to be fully prepared. Fast-forward to April 2024, and our research shows many specifiers are struggling to get to grips with the requirements, and this needs to be resolved. All designers must have the correct approach to specifications if the industry is to raise the bar on building safety. This includes getting to grips with the ‘nitty gritty’ of the BSA if they want to operate in the new regulatory landscape.” Worrying still are attitudes towards the Golden Thread and the critical role it plays for HRBs. For example, just under half of those surveyed (45%) are clear as to how they will manage building information to realise the Golden Thread and just one in ten have a solid plan in place. Dr Stephen Hamil, Innovation Director at NBS, said “The level of understanding around the golden thread of information is worrying. As well as providing a continuous flow of information throughout the entire lifecycle of a building, it is necessary to ensure all relevant safety-related information is readily accessible and up to date.” He stressed the need for robust specifications that will act as a point of reference to demonstrate that designs meet the Building Regulations as part of the submitted plans at the gateways. “However, the Building Safety Act presents a great opportunity for the industry to take back control of both the design process and through proper change control processes ensure that sub-standard construction does not happen. Safety starts with the specification and a well-managed approach to spec writing must form part of the standard design process.” David Bain, Research Manager at NBS, said “Consistency is the backbone of progress and the stakes have never been higher when it comes to HRBs. These studies serve to highlight ‘trouble spots’ and importantly, offer an understanding of how to take the industry forward as a whole.” The full report, which provides insight into industry views on the Building Safety Act and its implementation, launches in April 2024. To find out more about NBS, its services, and expertise, click here. Building, Design & Construction Magazine | The Choice of Industry Professionals
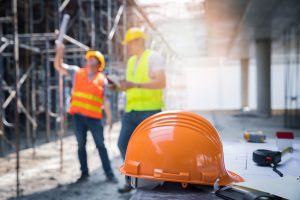
One new Act. Two different perspectives – A leading architect and manufacturer talk about the impact of the new Building Safety Act
The new safety regime introduced by the Building Safety Act 2022 came into force on 1 October 2023 putting residents at the heart of a new system of building safety. It makes all players in the construction industry more accountable for keeping buildings, and their occupants, safe. A leading architect and safety manufacturer each offer their thoughts on the implications of this new act will be for architects. Paul Bussey, Architect, RIBA, Allford Hall Monaghan Morris “The Building Safety Act is a whole new world for architects. As the principal designer it significantly increases our responsibilities, designating us as a ‘guiding hand’ for health and safety issues. “Some people think that the Act only applies to higher risk buildings and may think that if they don’t do high rise buildings (HRBs) they don’t need to worry about it. However, this is not the case. The act increases architects’ responsibilities for safety in the design and construction of all buildings. So, what does the new regime mean in practice for architects? “Well, it’s our job to eliminate hazards like fire and falls from height so far as is reasonably practical (SFAIRP). We also need to reduce risks from remaining hazards. “This means specifying safety solutions that will keep building contractors, maintenance workers and residents safe as well as be cost-effective and work well visually and structurally. “Clearly, we can’t be accountable for all the details ourselves, so we’re going to need increased support from the experts in our wider team including structural engineers, CDM advisers, building regulation advisers, fire safety experts, façade consultants and maintenance consultants. “We’re also going to need to work with industry more closely than we’ve done in the past. In particular, we’ll be seeking greater levels of transparency from manufacturers about their products so that we can be confident that we’re specifying solutions that are fit for purpose. “But our responsibilities under the Building Safety Act don’t stop there. Once we’ve decided on the solutions that will keep people safe, we then need to demonstrate to the Building Safety Regulator that we’ve complied with their requirements and that the solutions we’ve specified will actually work. This requires us to provide the regulator with a visual document giving calculations, architectural drawings, sections, structural detail and so forth. “For example, if we take a fall protection system, we must be able to demonstrate that the system will do the job it’s supposed to do – keep someone safe in the event that fall restraint is impossible and if they fall off the edge of a roof the entire fall arrest process is acceptable, including rescue. This means we must be totally confident that the system will work and make sure our client, funder and insurer are happy too. “Manufacturers have a key role to play here in providing us with the high-level information we need to be able to get a solution approved fast. We don’t want chapter and verse on everything – we just need to know what’s relevant and current that will help us demonstrate we’re fulfilling our responsibilities under the new Act. “I recognise that this can all sound a bit overwhelming but remember that as an architect you’re only responsible for managing safety risks so far as is reasonably practical. No one expects you to eliminate risks entirely. Basically, the new regime boils down to all the different players in the construction industry taking a more ethical approach and I, for one, welcome this.” Stuart Pierpoint, Specification Sales Manager, MSA Safety “For manufacturers, the Building Safety Act represents a big change in emphasis, ushering in a world where we need to take a scrupulously ethical approach. The consequences for those who behave unethically are pretty stringent – two years in prison and an unlimited fine. “In practice, the new regime means that manufacturers need to be more transparent when it comes to compliance. An example is when fall protection manufacturers offering products that only comply with the 1997 EN standard, rather than the revised 2012 standard, need to make this clear and avoid making misleading claims that their product meets ‘current standards’. “As an industry, we also need to be much clearer about when a product is ‘fit for purpose’ and when it isn’t – and be able to provide evidence to support any ‘fit for purpose’ claims. It is possible that some fall protection systems have not been tested on the same substrate that the architect is intending to use. Again, the load bearing capability differs between different substrates – thinner pliable substrates will have far less capabilities than heavier and denser substrates and both these factors are important considerations when choosing a fall protection system that is ‘fit for purpose’. “As manufacturers, we need to simplify the correct specification of a system. We need to get our manuals and documentation correct – making it clear what a product can and can’t do, what its limitations are and where it’s successful. And we need to make sure that the wording and imagery in these documents are clear for multiple users and in multiple languages. “We also need to ensure that our labelling, serialisation and evidence for any quality claims are all correct, that we follow quality management processes to the letter, do enough batch conformance testing to know that our products are being manufactured correctly, and carry out the correct audit trail with our manufacturing. “Manufacturers also need to work in close partnership with both installers and architects. When we’ve worked with an architect to help them select a ‘fit for purpose’ fall protection solution, it’s important that their specification for the roofing type is maintained so that our recommendation for the safest system is accurate. “In short, there’s a lot that manufacturers can do to support architects and help achieve the new Act’s vision. Here at MSA Safety, we’re keen to play our part and help make buildings safer for everyone.” Ultimately, the new Building Safety Act is a positive step forward