
Because It’s Your Job to Know – Quelfire Launches Campaign and White Paper
In the ever-changing world of construction, staying informed is crucial. Quelfire’s campaign and white paper aim to shift the narrative and promote an open conversation about embracing responsibility. They also focus on the importance of early engagement, collaboration, and education in the construction industry. Because it’s your job to know. Since the Grenfell Tower fire and subsequent changes to legislation, fire safety has become a significant industry focus, and the importance of passive fire protection has started to be acknowledged. The campaign emphasises the industry’s responsibility to recognise the significance of early engagement in firestopping and the selection of suitably tested details. It also highlights the imperative for manufacturers to operate transparently, providing key information to all parties involved in building projects. Following the campaign, Quelfire’s white paper delves into early engagement in more detail, exploring best practices that can save lives, reduce damage to a building and its contents in the event of a fire, and minimise construction delays and costs. Early engagement is about collaborating with the relevant key stakeholders as early as the design stage to retain fire ratings of walls and floors. This is achieved by appropriately sealing service penetrations with tested firestopping systems. It is also about cross-party communication, sharing of information and competencies, and understanding a project’s requirements before build commences. The white paper is a useful guide for anyone designing and managing the installation of service penetration seals, from main contractors to designers and firestopping contractors. It is an invaluable resource for professionals looking to enhance fire safety in their projects. Because it’s your job to know. Craig Wells, Sales Director at Quelfire, said, “The construction industry is starting to realise the responsibility it has when it comes to protecting people and property. Though it has taken a national tragedy and subsequent legislative changes to create the catalyst for change, change is happening. We at Quelfire will continue to test, share, and educate to support this change and, ultimately, create safer spaces. It is a pleasure to launch this campaign and white paper, which seeks to provide insight into best practices concerning the passive fire protection of service penetrations. Knowledge is power.” ——————– Quelfire is a leading manufacturer and supplier of tested firestopping solutions for service penetrations in buildings. What makes Quelfire stand out is the unwavering passion that everyone, from management to production, has for what we do: Protecting People & Property.Our mission is to support all parties involved in the design and installation of service penetration seals, including architects, designers, main contractors, firestopping contractors, and other specialist trades from dry-lining contractors to mechanical and electrical contractors. Building, Design & Construction Magazine | The Choice of Industry Professionals
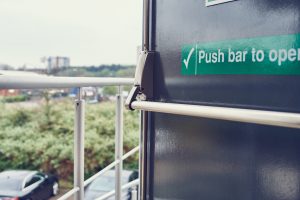
Panic Hardware vs Emergency Exit Hardware: Where, When and Why?
Sue Corrick of Allegion UK explores the evolution of panic and emergency exit hardware, examining the specification and installation points that decision makers must consider throughout modern application. The swift evacuation of a building and its occupants is critical in an escape or emergency situation. And for decades, escape doors and exit hardware have been co-dependent in their purpose of facilitating safe egress when it matters most. In fact, exit hardware has been providing users with a safe means of escape since the early 20th century. Following a string of high-profile disasters, including the infamous Iroquois Theatre Fire in Chicago in 1903, the conditions of the world’s built environment and its emergency exits were more closely inspected as crucial elements of public safety, in large part to The National Fire Protection’s (NFPA) Life Safety Code in the US. Incidentally, this period was a catalyst for change in the exit device industry, with the world’s first panic bar made available in an assortment of configurations in 1908, courtesy of Von Duprin. Today, the term ‘exit hardware’ is more conventionally categorised as either panic hardware or emergency exit hardware. With distinguishing characteristics and features, both categories of exit hardware provide users with a safe means of escape, and both have come a long way since their inception all those years ago. As such, selecting the most suitable solutions can be a challenge for modern projects and decision makers are reminded to consider a number of key factors. Distinctive door hardware In a fire scenario, a building’s evacuation methods must be as straightforward and defined as possible. When a person reaches an exit door, it is essential that the door can be operated with ease, regardless of who is operating it and where it is being used. While all exit hardware plays an integral role in this process, decision makers must consider a building’s type, application and its occupation levels when selecting between panic and emergency exit hardware, since there are meaningful differences between the two. Panic hardware for example, is a type of exit device that has been designed to provide safe and effective escape through doorways with minimum effort and without prior knowledge of its operation. Panic hardware devices come in the form of horizontal push or touch bars and are commonly applied to outward opening doors in public facing buildings or buildings with more than 60 occupants, where they can be operated by untrained people or members of the public, ensuring safe and effective escape. As such, panic device push and touch bars should be installed to provide the maximum effective length, but never less than 60% of the door leaf width, as stipulated by BS EN 1125 and harmonised CE and UKCA designated standards. With its size, panic hardware is typically easier to see and operate than some emergency exit hardware devices. With this in mind, decision makers should often choose to implement panic hardware solutions in busy public spaces such as hospitals, shops and places of entertainment where usability is paramount. For spaces where opening width is limited, a non-intrusive touch bar can also be a practical option. Furthermore, in cases where users may wish to gain access from the outside of a door with a panic bar, an outside access device can also be applied to maintain equal levels of accessibility and security. Emergency exit hardware is dissimilar in a few areas. Typically smaller devices, emergency exit hardware is often applied in buildings with less than 60 occupants or non-public buildings, where its users have prior knowledge of the building’s layout, its escape routes and the exit devices placed throughout them. Think office spaces and warehouses for example. In design, emergency exit devices commonly comprise of a single push pad with a rim latch or a lever handle operating a mortice escape lock or nightlatch and allow for single action egress. Where emergency exit hardware is applied, it must be certified to BS EN 179. Information is key As per Approved Document B, all doors located on an escape route must have suitable exit hardware installed. And so, with varied solutions available, specification teams must also consider the door in which an exit device will be fitted. Will the device be applied to single or double doors? What are the height and width requirements? And does the device need anti-thrust bolts for added levels of security? Above all, does it meet the latest fire safety standards? If in doubt, decision makers are urged to select door hardware devices that are tested to EN 1125 while referring to harmonised and designated standards if they feel unsure. BS EN 1125 and BS EN 179 standards provide important safety and reliability details on panic hardware and emergency exit devices respectively, reviewing classification, product performance requirements, test cycles and test methods as standard. For traceability purposes, decision makers and end-users can also review the UKCA and CE marks on exit hardware to find its fire rating, certificate numbers and the manufacturer’s details. Typically, dependable devices will be supplied with full product information from the manufacturer – including Declaration of Performance (DoP), Certifire certification and product data sheets – showing that they comply with the necessary harmonised standards. The Code for Construction Product Information has been designed to assist people in reviewing and selecting door hardware solutions transparently and can also be referred to for clear, accurate and up-to-date product information, to ensure door hardware solutions conform to the latest building standards and UKCA and CE certifications. Similarly, when it comes to installation, teams are advised to use the support that’s made available by manufacturers, in the form of helpful online tools and product guides. This further helps to ensure there are no oversights made at the installation stage that could develop into life-threatening issues later down the line. Under current EN standards, it is also recommended that all of a fire door’s hardware devices should be supplied from the same manufacturer and tested together to ensure the full doorset remains
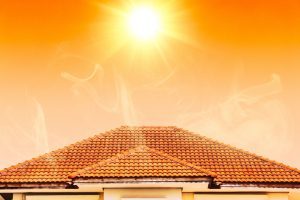
MPs back RIBA calls for National Retrofit Strategy to tackle overheating nightmare
On Wednesday 31 January 2024, the cross-party Environmental Audit Committee (EAC) has raised concerns over the UK’s lack of preparedness in its report on ‘Heat resilience and sustainable cooling’, after the world’s hottest year on record. The EAC’s report makes recommendations to the Government based on written and oral evidence given by the Royal Institute of British Architects (RIBA). RIBA President Muyiwa Oki said: “Today’s report is another stark warning about our warming planet – and the dangers it brings to both people and our built environment. It positively echoes our calls to accelerate action on heat adaptation measures as part of a well-funded National Retrofit Strategy and expand urban green space. These “no regret” solutions bring great benefits, not only mitigating the impacts of extreme heat, but also by supporting healthier lives. We hope the Government urgently acts on these recommendations and utilises our professional expertise – architects are critical to the delivery of a sustainable, more resilient built environment.” Building, Design & Construction Magazine | The Choice of Industry Professionals
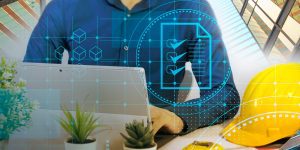
BuildData predicts information will be king in 2024
New building regulations with requirements for effective digital information management for compliance, will be a driver for tech buying decisions this year. 2024 is the year when the Building Safety Act (BSA) will come into full force, following the first provisions rolled out in 2022 and 2023. The BSA mandates digital building information and safety cases, as well as a golden thread of information, for higher-risk buildings (HRBs). Therefore, prioritising information will be high on the industry agenda in 2024, all delivered by technology to ensure effective information management. But the BSA is not the only regulation with a requirement for digital information competency for compliance. Photographic evidence is now mandatory to comply with Part L under Building Regulation 40. And more legislation and standards are set to follow with digital information requirements, such as the Future Homes and Building Standard, where information will be needed to support building design, construction, and management. With the evolution of the construction and property industry, there is no time like the present to get information, processes, and the technology in order to deliver better information and, therefore, building outcomes. This emphasis on digital data and information to better manage buildings throughout their lifecycle — from planning all the way through to operations and maintenance — is not necessarily new concept. However, it is only recently that the focus has shifted across the construction and building management sectors to prioritise its importance, driven by new and updated standards and legislation. That is why BuildData Group, with its brands Zutec, Createmaster and Createmaster Information Management, believe information will be king, and should be given the same attention as the physical asset. Emma Hooper, Head of the Research Institute at the BuildData Group, states: “As an industry we need to shift our thinking about information and data, as it lies at the core of regulation, digital transformation, and the way a built asset is designed, constructed, and operated. Essentially, we need information management to enable us to find, share, understand, use, and query what we do in an easy, digestible, and decisive way, while ensuring quality and trust. It is the linchpin of everything we do across the built environment, and without it we cannot operate effectively. In our minds, information and good information management should be as important as the built asset itself.” So why will information be king in 2024? Keeping people and our environment safe, keeping well-maintained buildings The construction, built environment and digital worlds are constantly evolving. Therefore, ensuring the right stakeholders have the right information at the right time to make decisions, control risk, keep buildings well maintained and people and our environment safe is critical. Information is only useful if it is available, accessible, easily discoverable, and understandable and a golden thread of information is now legal requirement of duty holders and accountable persons of occupied higher-risk buildings under the BSA. This is to ensure that everyone involved in building safety management and maintenance, whether directly or indirectly, has access to key details that can help identify, assess, and mitigate risks. When the right information is delivered at the right time — whether it’s to facilities management, the fire department, or tenants — more informed decisions can be made more quickly. With the right technology platform and stack in place building information can be surfaced, managed, and shared, and kept up to date to meet compliance. Being able to integrate with other systems means all building information can be managed in one place, supporting the journey to a golden thread of information, and making information king. Quality over quantity There is a plethora of information required to meet building regulation compliance. From fire and emergency files to structural information, health and safety files, as well as operations & maintenance manuals and completion certificates – all this information should have a purpose. Without purpose it is useless. This means information must be high quality to the degree that it performs that purpose, is usable and enables the outcomes it is intended for. There are several criteria used to measure information quality, including accuracy, completeness, consistency, timeliness, and validity. All of this is important because it ensures that the information used to make key decisions is reliable. It is therefore critical to ensure information quality throughout the information management process, as without this it can lead to ineffective decision-making, construction and operational errors, and ultimately put lives and our built environment at risk. There is also a direct correlation between information quality and information compliance. Lost, inaccessible or inaccurate information can cause huge issues, and one of the reasons we have building standards and regulations in place. With a consistent structure, schemas, and workflows, as well as standardised forms, templates, and checklists, one platform for information management can ensure that data meets quality standards. And, when construction quality is a huge factor in delivering buildings that meet standards and compliance, then the information quality related to that building should be equally as good. Another reason to make information king. Right data in, is right information out Leading on from good quality information, is the right data going into the information management system or platform. The right information in, results in the right information coming out to drive the decision-making process, while controlling risks and reputation. Many systems today have AI or machine learning functionality to help surface the right information. However, the main obstacle for AI is poor quality data, which directly impacts the reliability of the AI model in place. When in investing in technology, it is also crucial that the data going into a platform is accurate, representative, and of high quality. When information comes from so many sources, the construction and property industry has always struggled to collect documents and data, structure this information and label it correctly, all while maintaining quality. Companies like Createmaster, can help collect, tag, and review the information for quality, and store in one platform (like Zutec), with dashboards to manage that information to ensure data governance and robust and accurate information,
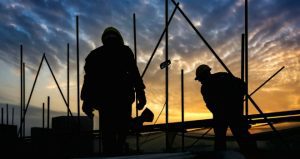
Planning delays: New law promises reform but will planners deliver on it?
By David Norman, Davon For smaller and medium-sized developers, 2023 was the year that everything took longer. It took longer to find and acquire land, longer to obtain bank funding and longer to get materials delivered but most of all, it took longer to get planning permission. There was barely a day all year when I didn’t have a discussion with a client involving planning. The industry’s frustration with the ponderous UK system is palpable. It’s particularly galling for the SME residential developers who are typically our clients because they have fewer resources to deal with the bureaucracy and face more intense financial pressures than the big hitters, notably on cashflow. When you are stretched on a project having shelled out for a parcel of land, planning delays pile up your bank interest. Time is money. And it is not just delays that eat cash. Even a small development of, say, two houses can incur upfront costs of £30-50,000 in planning and professional fees. For more complex projects, that number can easily top £100,000 when you factor in consultancy fees for a broader raft of planning hurdles such as right to light and environmental studies. Another big-ticket pre-planning bill can be option fees for the landowner. Unfortunately for developers, banks dislike lending against developments pending planning applications as there are no assets in the project, which means the developer must find the cash. These pressures have had a cataclysmic effect on smaller to medium residential developers. According to the Federation of Master Builders, 40 years ago SME house builders delivered 40% of our homes. Today, this figure is just 12%. Planning is not the only culprit. The FMB says the sector has been hit hard by successive recessions. They report that SME and custom builders say they struggle to access finance and land, but right up there on their list of complaints is the difficulty of navigating Britain’s complex planning system. Our experience at Davon talking to SME residential developers throughout last year bore that out, so we were pleased to give our support to the FMB’s campaign for: For years, successive governments have promised action to tackle the housing shortage and streamline the planning system. Yet the industry sees little or no progress and has become at least sceptical if not cynical. The latest government initiative is the Levelling Up and Regeneration Act which became law in October 2023. It is supposed to speed up the planning system, hold developers to account, cut bureaucracy, and encourage more councils to put in place plans to enable the building of new homes. The Act promises that new developments will be more attractive with better infrastructure such as GP surgeries, schools and transport links. Development will be shaped by local people’s democratic wishes, enhance the environment and create neighbourhoods where people want to live and work. That all sounds great, but will it happen? One feature of the Act that caught my eye is to give councils the power to work directly with landlords to bring empty buildings back into use by local businesses and community groups, “breathing life back into empty high streets”. Many people in the property and construction world will tell you that converting offices and retail premises into residential is fraught with difficulty, but it can be done successfully. Take our client, Barker Homes for example. We have provided mezzanine finance for a series of their conversion projects, the latest being a £10.5 million redevelopment to transform a town centre commercial building in Hemel Hempstead into 40 luxury apartments. If planning policy changes can smooth the path for more of these and other kinds of conversion of redundant buildings, that would be welcome. It will be necessary if the Act is to deliver on its objectives, which include directing growth to support the regeneration of brownfield sites and renewing and levelling up towns and cities with more homes in Britain’s largest urban centres including in the North and Midlands. The government says that this will not only make the most of brownfield land but also maximise the use of existing infrastructure, taking advantage of structural change in urban land use and reducing the need for unnecessary travel. One criticism we often hear is that national and local planning is not joined up. To some extent this is addressed in the Act with new joint spatial development strategies to bring together planning authorities across boundaries where there are strategic reasons to do so. But at the local level where our clients operate, it is the promise of a speeded up, streamlined planning service that is most appealing. Previously mooted planning overhauls have met with reticence from the planners themselves but this time, at least publicly, they are being supportive. The Act has been backed by the planners’ professional association, the Royal Town Planning Institute, although its chief executive, Victoria Hills, said if it is to be successful, the government must engage frequently with planners to ensure that new regulations and policy work as intended and deliver on those promises. To me, that is the crux of the matter. There have been too many initiatives for change in the system that have fallen by the wayside as well as promises to deliver on housing and regeneration that have been little more than re-hashed versions of existing policies. What the industry desperately needs is action, and that means ensuring that planners are on board with the spirit of the new law. Building, Design & Construction Magazine | The Choice of Industry Professionals
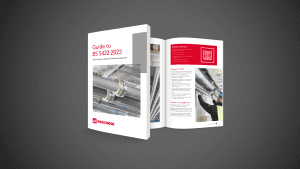
ROCKWOOL® launches CPD on building services insulation standard
CPD explains important practical changes and additions to BS 5422 ROCKWOOL, the UK’s leading stone wool insulation manufacturer, has launched an ‘Introduction to BS 5422’, a new CPD (Continuing Professional Development) module to support specifiers and engineers with advice on how to plan and implement the insulation of building services systems following a recent update to the standard. The CPD coincides with the recent publication of ROCKWOOL’s Guide to BS 5422:2023. BS 5422 provides a method for specifying thermal insulating materials needed on pipes, tanks, vessels, ductwork and equipment for certain defined applications and conditions within the temperature range – 40°C to +700°C in domestic, non-domestic and commercial buildings. The standard works as guidance for consultants, engineers, contractors and manufacturers of thermal insulation in the building services sector. It supports Approved Document L as the reference point to determine the minimum thickness of insulation required to limit heat losses and gains from building services. ROCKWOOL’s new CPD module explores the factors that need to be considered when deciding on the insulation of building services systems according to BS 5422. It also demonstrates how the standard aims to improve the living and working environment of the building as well as make it safer and more energy efficient. “With BS5422:2023, the insulation requirements for building services and HVAC systems have been aligned closely with current thermal Building Regulations,” comments Will Wigfield, Product Manager – Fire Protection & HVAC at ROCKWOOL UK. “The new CPD will explain how the standard makes it easier for designers and specifiers to choose the most appropriate material for each project and allow them to exceed the minimum requirements if they wish.” Learn more about BS 5422, register to attend the ROCKWOOL CPD session at https://www.rockwool.com/uk/advice-and-inspiration/learning/. Building, Design & Construction Magazine | The Choice of Industry Professionals