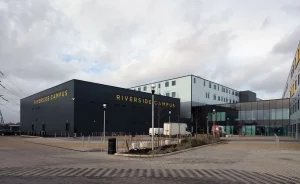
Why Modular Construction in the Commercial Sector Stacks Up
With the recent focus on the modular housebuilding industry, Richard Hipkiss, Development Director of the Modular and Portable Building Association (MPBA), considers why the outlook in mature commercial markets is on a different trajectory. Vast investment is required to set up advanced manufacturing facilities and production lines work best when demand is steady, and utilisation is high. But as we all know, construction is an unpredictable business – particularly in the housing sector, as we are currently witnessing. The underlying challenges of the housing shortage are much more complex and political than simply finding a quicker way to build. Manufacturing facilities require a substantial investment of time and money to set up and need a constant throughput of work to provide a return on that investment. The stop start nature of residential construction is not conducive to keeping a factory running at capacity all the time. This is why so many of our members operate in sectors such as healthcare and education where modular approaches have been successfully used for decades. Leading modular manufacturers strive to develop long-term strategic relationships by developing skills and sector specialisms. A healthier pipeline of future work allows modular players to optimise their products and develop their production capabilities. For innovative construction methods to become a preferred alternative that can truly compete with traditional methods, strategic alignment between modular producers and construction clients, particularly in the public sector – are mutually beneficial. The benefits of volumetric modular buildings come from the industrialisation of key construction tasks. MPBA members aim to standardise, streamline and automate major parts of the value chain. To get that right, modular companies need best-in-class manufacturing capabilities, including sophisticated digital design platforms and lean, efficient production lines. Investment in digital technologies such as Artificial Intelligence (AI), Internet of Things (IoT), 3D printing and real-time data analytics – is happening at pace. It is standard practice for Building Information Modelling (BIM) to be embedded into the design and advanced manufacturing processes involved in modular construction. Increasing technological advancements coupled with the advantages provided by modular construction such as vastly reducing building schedules and cost without impacting on quality, together with sustainability gains such as reduction in construction carbon and material waste – are contributing to demand in the commercial sector. Evidencing Value Pre-Manufactured Value (PMV) is another driving force in the specification of volumetric technology in public projects – particularly in the healthcare and education sectors. PMV is a core metric for measuring the level of MMC in a project and is central to the UK government’s procurement programmes. To secure a contract, suppliers are required to show that pre-manufacturing will account for at least 70% of their construction cost, which plays to the strength of a volumetric modular approach. Traceability and Accountability Since 2016 the BIM mandate has required UK public sector construction projects to use BIM technology. This has helped speed up the pace of adoption during the design and construction phases. It has been predicted that government intervention around the ‘golden thread’ will accelerate things further. Central to the concept is guaranteeing the traceability and availability of project data and all decisions relating to the design, construction, safety performance and maintenance of the building. The ‘thread’ involves the information handed over at the completion of a project which must be right from the start of client ownership and then must remain accurate throughout the building’s lifecycle. With traditional construction often key information such as product specification and maintenance details are not complete or accurate at the point of client handover which means the golden thread required for optimal running and safety cannot be achieved. As an established method of sharing building lifecycle data across design, construction and operation – BIM is also regarded as integral to achieving a golden thread. Accurate and Reliable Information With volumetric modular construction all data can be validated and coordinated as part of a structured process, which helps provide accurate and reliable information for clients at the point of handover. It also means it is easier to identify what products and material specifications were used on previous projects should any legislation changes occur. With its powerful combination of controlled deliverables and customisable outputs, modular construction provides cost and time efficiencies together with the repeatable quality and safety – meeting the key drivers and stringent protocols demanded by the commercial sector. About MPBA The MPBA plays a key role in the connecting of sectors in the modular and portable building industry. The association collaborates with specialist technical advisors to enhance innovation in the design and manufacture of modular buildings. These can be designed and manufactured from timber or steel in any size and shape to meet individual client needs while ensuring full compliance with Building Regulations. To discover how modular technology can benefit construction projects go to: www.mpba.biz Building, Design & Construction Magazine | The Choice of Industry Professionals
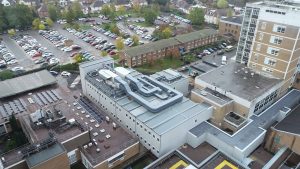
McAvoy Continues Rental Fleet Expansion in the UK and Ireland
In response to growing demand across the healthcare, pharma, education and commercial sectors, NI-based offsite manufacturer McAvoy continues to invest strongly in the growth of its SmartSpace temporary building fleet. It recently launched additional new innovative space solutions via its QSpace and ESpace single modular buildings. The business continues to experience high demand for rental projects in both the healthcare and education sectors, including a second, significant 10-year rental contract for University Hospitals Birmingham NHS Foundation Trust. Investment in manufacturing capability has continued with the acquisition of a custom-built mobile gantry, increasing efficiency, and improving workplace safety. This commitment to investment in the business also includes ESG, digital technologies, recruitment, and people development. CEO, Ron Clarke said: “The group continues to see strong interest in its proposition, and with the continued support of our shareholders the company is in an excellent position to deliver its strategic growth plan. We are confident that our high performing temporary and permanent buildings will continue to deliver modern, flexible, and sustainable space solutions to our customers. Looking ahead we are on track to deliver a significant increase in performance in 2024.” During the past year, the business has delivered a number of key projects across the country, including a new Collaborative Research & Innovation Centre in Wiltshire, the pioneering “Low Carbon Pathfinder” 900 pupil school at Redhill in Surrey for the Department for Education and two 24-bed ward buildings at Antrim Area Hospital. The company has also been chosen by the Department for Education to design and build a £37.5m, 1,200-place Academy in Essex. Furthermore, several of the company’s projects and innovations have been recognised by independent peer group awards, including Healthcare Project of the Year at the recent Offsite Awards. McAvoy is a leading provider of high-quality temporary and permanent modular buildings across the UK and Ireland. Its adaptable and sustainable space solutions are sought after in both public and private sectors including healthcare, pharma, education and commercial. Innovation continues to be a central part of the company’s activities. For the period ended 31 May 2023 McAvoy reports a strong performance within its rental division with revenues of £12m and EBITDA growing to £3.8m primarily due to rental fleet expansion in the health and education sectors in the UK. The business also reports a steady performance in its permanent offsite division. In its latest set of consolidated accounts McAvoy’s revenues were c.£60m and also generating c.£5m EBITDA. For the period ending FY24 the business is on track to achieve revenues in excess of £70m, primarily driven by investment in the fleet and further success in the temporary segment. Building, Design & Construction Magazine | The Choice of Industry Professionals

Boutique Modern expands in Newhaven with new factory
Construction company Boutique Modern will start building a new factory in Newhaven this year which will create more than 35 further jobs at the business and double its capacity. The BCorp modular housing company was given the green light by Lewes District Council to build the factory in Avis Way and plans to move in at the end of this year. The business specialises in delivering sustainable homes for affordable and social housing schemes in the South East, helping the most vulnerable people in society to find a place they can call home. Dick Shone, managing director at Boutique Modern, said: “This is an exciting new chapter for Boutique Modern, which will mean more homes and jobs for local people. “This will prepare us for the next exciting phase when we open satellite factories in other areas with housing demand. Each new factory will create upwards of 100 new jobs and generate more than £20m for the local economy per year, per facility. “It’s our belief that social and affordable housing should be beautifully designed and sustainable and it’s a privilege for us to be able to make a difference.” The factory has been designed by award-winning Brighton architects Morgan Carn and will feature a two-storey industrial building to be used to manufacture offsite modular housing units. Boutique Modern currently employs more than 70 people but has outgrown its current site in Beach Road. The new factory will take its headcount to more than 100 employees. The empty disused site in Avis Way was previously occupied by a large workshop, store and office building that was demolished in 2021 and the space is currently used by Boutique Modern for the temporary storage of off-site housing modules. When the new factory opens at the end of this year, it will enable the business to operate two manufacturing lines, which will provide more flexibility in terms of what it manufactures and increase control over delivery speed to clients. At full capacity the factory will be capable of producing up to 125 houses or 250 flats per year, whilst maintaining flexibility in its output to manage market peaks and troughs. Shone added: “The Boutique Modern business model has been developed over more than 10 years to allow us to open satellite factories in locations where there is housing demand. “Instead of growing one large factory capable of producing thousands of homes in a single location, the Avis Way Factory will allow us the opportunity to pilot setting up in a new facility with our existing processes and systems before we expand to other sites, thereby enabling the sustainable growth of our business.” The new factory will feature solar panels to provide on-site power generation for lighting and power tools, feeding energy back into the grid when not required on site. It will also include electric vehicle charging points and more than 30 covered cycle spaces for employees to cycle to work, together with trees and plants to improve the look of the site. Councillor Zoe Nicholson, leader of Lewes District Council, said: “I’ve placed a strong focus on community wealth building at the council, so to see a local contractor we work with growing so dynamically is really exciting and welcome news. “I recall being at the opening of the homes in Fort Road, Newhaven, the first modular project undertaken by Boutique Modern for Lewes District Council. “It was a proud moment seeing new council housing opened that is highly sustainable and of such high quality. There is so much good news coming out of Newhaven and plenty still to come.” Newhaven Enterprise Zone programme director Corinne Day said: “We are so happy Boutique Modern is expanding into a new site in the town. “We cannot wait to cheer on the business as it continues on its exciting journey and it’s fantastic news it will create even more jobs for local people, both here in the town and later on in other sites across the region.” For more information visit: https://boutiquemodern.co.uk/ Building, Design & Construction Magazine | The Choice of Industry Professionals
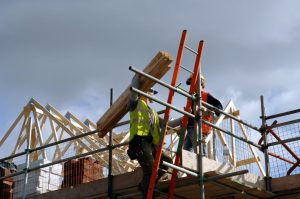
Building Better searches for traditional contractors to join £800m MMC framework
Building Better, the National Housing Federation-backed alliance of housing associations and councils set up to increase the use of modern methods of construction (MMC) in social housing, is hunting for dozens of local, traditional build principal contractors for a new MMC framework. Procurement for Housing (PfH) is working with Building Better to develop the £800m framework which will run over four years. Traditional construction firms in 10 different regions of England and Wales will be appointed, offering their services as lead contractor on MMC projects. The ‘Integrated Traditional Build & MMC framework’ is being designed in response to calls from social housing providers for a compliant way of involving trusted, local contractors on MMC projects, where elements of traditional construction are often still needed. With a growing number of MMC manufacturers supplying only their systems – rather than taking the principal contractor role – housing providers want to bring in local, trusted construction firms who can lead offsite projects. This will also allow housing associations and local authorities to continue investing in local contractors. To shape the framework, PfH and Building Better have spoken to SME building firms across the country, gathering feedback on how an agreement would best work, including ways to make the procurement process more straightforward and to develop the most effective contracting environment. The framework will cover the construction of housing, apartments, and extra care homes and there will be a regional lot structure. A contract notice will be issued in March 2024, with successful bidders appointed in the summer. Tony Woods, Technical Manager – Construction & Sustainability for PfH said: “We’ve been talking to traditional contractors to find out how they’d want to work on MMC schemes and, interestingly, many of their requests are the same as those from offsite manufacturers. Both want to be engaged early in the process, before set designs are in place. Both want a more transparent way of working with wider use of ‘pain and gain’ agreements and a simpler, more collaborative contracting environment. This feedback is now being used to design our integrated framework.” Trina Chakravarti, Director of Building Better said: “Increasingly, our members want a blend of different construction methods on their MMC projects. Traditional SME construction firms have a huge amount of expertise, and we’re keen to harness this through the framework. Using a collaborative approach means that manufacturers can concentrate on delivering their product, traditional firms can take control of the building process and we can offer housing associations and councils a wide range of construction solutions.” For further information about this procurement opportunity contact Tony Woods at Procurement for Housing (PfH) twoods@pfh.co.uk Building, Design & Construction Magazine | The Choice of Industry Professionals
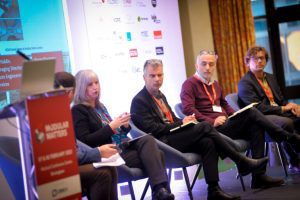
Modular Matters: Get the Housing Minister’s Take on the MMC Nation
The volumetric modular sector is at a critical tipping point. The industry faces unprecedented challenges following a year of fluctuating demand in the housing sector – combined with increased scrutiny from the market and media. But while there are many obstacles to overcome, those operating in the modular industry are still pushing game-changing technology and evolving to meet future demands. Taking place on 19 – 20 March 2024 at the Coventry Building Society Arena – Modular Matters aims to separate the fact from the fiction, tackling the big conversations and facing the positive and negative impacts of the last year. With Housing Minister Lee Rowley making the keynote presentation, this event offers a massive opportunity to find out first-hand about the ‘state of the MMC nation.’ Strategic Thinking It is not all doom and gloom, and despite a tough year volumetric modular technology remains at the forefront of innovation, capable of redefining how we think about construction, with the ability to not only improve structures but create sustainable spaces that support a circular economy. With game-changing industry leaders presenting success stories and demonstrating proven techniques for overcoming the current status quo – Modular Matters takes a frank and candid look at the commercial and financial barriers to growth, to determine the roadmap to stable and viable long-term business models. Influence the Narrative With a brand-new venue, the 2024 event will provide a more interactive and engaging platform that encourages active delegate participation through facilitated engagement and discussion. Lifting the bonnet to get to the detail, taking lessons from global benchmarks and client-led conversations. The conference will invite industry innovators, change-leaders, influencers and modernisers to have their say. Modular Matters will determine the actions needed to make radical transformative change in the market and develop a viable and sustainable modular supply chain. Modular Matters offers a platform for all voices in the industry to have their say on: Why Attend? Raising the bar, building on the successes of previous events, while diversifying and expanding the programme and exhibition to attract a wider audience – Modular Matters presents an opportunity to join the conversation and connect with key players in the sector as well as suppliers, manufacturers, architects and decision makers from local authorities and the public sector. Modular Matters 2024 invites delegates to deep dive into the current state of the modular market, tackling the recent changes and increased media attention following the withdrawal of multiple players from the sector. With an objective to influence, inform and investigate – Modular Matters will address roadblocks, identify solutions, analyse successes and separate the myths from the facts. Keynote speaker, Housing Minister Lee Rowley will be joined by presenters from Homes England, TopHat, Crown Commercial Services, Tide/Vision, Platform Housing Group, HLM Architects, Cartwright Pickard, Fulcro Engineering Services, Beattie Passive, Portakabin, Algeco, McAvoy, Elements Europe, Lighthouse, MTX, TG Escapes, Kope, So Modular, Mishcon de Reya and Reds 10. For the full speaker line up and to book your place, go to: www.modularmatters.co.uk
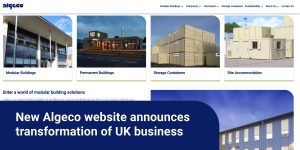
New Algeco website announces transformation of UK business
Algeco has relaunched its website with major improvements around content, navigation and additions to its full suite of site accommodation, storage units and offsite solutions. For the first time, the new website brings together Algeco UK Ltd and Mobile Mini UK Ltd into a single entity under the Algeco brand. A major benefit to customers of the redevelopment is that, www.algeco.co.uk, now incorporates one the largest fleets of storage containers in the UK. These are delivered to customers nationally in the company’s own fleet of delivery vehicles. Other improvements see dedicated pages for the Algeco 360 range of facilities services, making it even easier for customers to access full turnkey site accommodation solutions. Algeco 360 turnkey services means just one point of contact covers every base, making customer’s projects more streamlined, straightforward and efficient. The new website has been accompanied by a merging of Algeco and Mobile Mini social media channels, simplifying and creating a shared network of information for customers that is continuously updated, making social media the go-to place for the latest Algeco news. Visitors to the new website will immediately be familiar with the iconic Algeco logo and font, common across the wider Algeco European businesses. The website reflects the transformation the UK business is undergoing and visually represents the Algeco goal of being the leader in offsite construction, temporary accommodation and secure storage solutions. Easy navigation reduces the number of clicks that visitors have to make to navigate the site, whilst filters allow easy honing down of the Algeco product or service that customers require. A goal during the website redesign process was to create a customer-centric and responsive platform that makes it easier for visitors to learn and locate information about Algeco solutions for their particular application or industry. Case studies, again listed by sector, highlight completed projects and the value it delivers to customers throughout the UK. These range from turnkey site accommodation solutions through to offsite construction of an entire school, amongst others. A comprehensive section of the website is dedicated to how Algeco is helping customers achieve sustainable business growth. This essential resource will appeal to visitors seeking to enhance their environmental impact whilst ensuring long-term success. It brings together product advances, such as off grid solutions, and Algeco advanced programmes around ESG (Environment, Sustainability and Governance). Chris Coxon, Head of Marketing at Algeco, said: “The first thing that visitors to our new website will notice is that we now have an impressive container hire offer – one of the largest fleets in the UK, backed up with our own fleet of delivery vehicles.” Chris added: “Visually, our new website has everything you’d expect with inspirational images of 360 turnkey site accommodation though to multi-storey permanent offsite construction projects and everything in between! We are confident that it provides a fresh perspective and an enhanced online experience for our valued prospects, customers and partners.” Algeco is Europe’s leading modular and temporary accommodation brand, originally formed in 1955. To view the new website, visit: www.algeco.co.uk Building, Design & Construction Magazine | The Choice of Industry Professionals