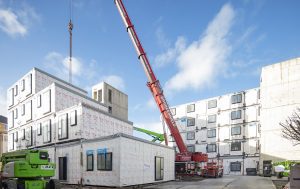
Increasing Sustainability Throughout the Value Chain
The construction sector is facing multiple challenges – some historic such as low productivity, others more recent such as environmental impact and a lack of lifecycle information. But why is it imperative to think of the ‘end’ right at the design stages to enhance the sustainability value chain? Richard Hipkiss, Development Director of the Modular and Portable Building Association (MPBA) explains. Progress has been slow but now with the advances in digital technology and new construction techniques such as design for deconstruction (DfD), design for reuse (DfR) and the one gaining most traction – design for manufacture and assembly (DfMA), we are finally making great strides in modernising the construction industry. These three disciplines can be difficult to implement in site based approaches however the stringent management and digital protocols within volumetric modular design and manufacturing processes create the ideal environment to optimise their use. The UK government has been promoting volumetric modular construction as a method that can improve productivity, but modular technology can help deliver sustainability gains throughout the entire construction value chain. At present the focus is concentrated on using volumetric technology to improve resource efficiency upstream at the design, manufacturing, and construction phases. This appears to be detached from the need to promote resource efficiency and productivity at the stages occurring downstream – disassembly and end-of-life management. Such divergence could hamper the construction industry’s efforts to reduce its long term environmental and economic impacts and points to the need of an integrated, holistic approach to improving the sustainability value chain as an end-to-end concept. What are the benefits throughout the entire construction value chain? Volumetric modular construction does indeed offer multiple benefits upstream, including ease of constructability, increasing quality and reducing time of construction as well as the capacity to cope with skilled labour shortages and creating much safer working environments. Most importantly, it can substantially reduce construction waste generated onsite via promoting resource efficiency at the manufacture and installation stages. But the efficacy of this construction method to yield benefits downstream at the end-of-life has received comparatively little attention. Advances made in the UK towards improving productivity in the construction sector via the application of volumetric modular technology and digitalisation are well documented, however as the trade body for the sector, the MPBA also needs to shine a light on the opportunity to improve sustainability performance throughout the value chain from concept to end-of life. Design for manufacture and assembly, design for deconstruction and design for reuse protocols are an exemplary way of connecting upstream and downstream construction stages and can be used as a means to actively apply sustainability principles. The digitally enabled volumetric construction model has the potential to capture and record this valuable lifecycle data. The rise of digital technology offers an opportunity to bring business transformation in the construction sector and promote a new way of doing things; effectively enabling transformative change which will enhance the sustainability credentials of volumetric manufactured buildings. Implementing smart modular regimes to mitigate the impact of climate change As the construction sector develops and adapts to meet changing government strategies to enhance sustainability credentials, I firmly believe the upward trajectory of volumetric modular buildings will continue and we need to act now to help mitigate the impact of climate change. A smart volumetric modular construction regime can operationalise the collection and storage of components’ lifecycle information, and help the sector build the capabilities needed to support the maintenance, recovery and reuse of modular components, and reduction of waste. For this to take precedence it is imperative to think of the ‘end’ right at the beginning of the design stage and foster improved collaboration between all construction partners involved in the supply chain. MPBA The Modular and Portable Building Association plays a key role in supporting all sections of the industry. Leading best practice principles and specialist training schemes, the association is represented on many committees for the benefit of members. Most importantly, the MPBA ensure evolving government policies and decisions are not made on behalf of the construction industry without due consideration for the impact they may have on the volumetric modular sector. Founded in 1938, with an in-depth understanding of the industry, the MPBA has represented this advanced and highly innovative sector for over 80 years. www.mpba.biz Building, Design & Construction Magazine | The Choice of Industry Professionals
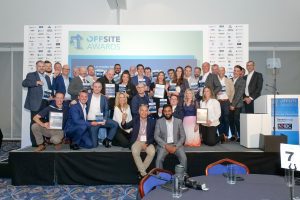
Celebrating Excellence in Offsite
Launched in 2015, the Offsite Awards were certainly ahead of the ‘MMC’ curve. Last year the judges reported record entries and claimed the calibre of submissions revealed how far the industry has moved on in just eight years. Taking centre stage on the evening of 19 September 2023, the Offsite Awards will once again be returning to the Coventry Building Society Arena, alongside OFFSITE EXPO – creating a dramatic climax to the first day. The Offsite Awards celebrate excellence in precision building design and delivery. By recognising and rewarding outstanding examples of prefabrication and factory-based methods, these awards shine a spotlight on those who are leading the way in developing a more sustainable built environment. The judge’s feedback offers not only plaudits but sometimes useful advice with comments ranging from: “This project articulates many benefits of offsite construction, the net zero ambition and sustainability targets met as a result should be highly commended.” To: “A strong submission which demonstrates carefully considered use of offsite technology but more robust evidence relating to carbon reduction would have increased scoring.” Celebrating projects large and small, its technical innovation and performance details that catches the judge’s eye, together with strong supporting evidence and good images or visuals. Entry Deadline – Friday 26 May 2023 If you have an outstanding project, product or person that is making transformational change in the way buildings are designed, engineered and constructed, now is the time to start planning for the 2023 awards. These awards represent an excellent opportunity to increase profile and credibility in the sector, generate media attention together with gaining accolades and acclaim from a judging panel that includes some of the offsite industry’s most respected figures. Free to enter, there are 25 categories that cover every aspect of the industry from hybrid and modular technology to engineering and installation, ensuring that all phases of the offsite building process is celebrated. The Offsite Awards submission platform is now open for entries with the final deadline confirmed as Friday 26 May. Finalists will be announced in July 2023, with the awards being presented alongside OFFSITE EXPO on the evening of the 19 September 2023. For more information and to enter go to www.offsiteawards.co.uk Building, Design & Construction Magazine | The Choice of Industry Professionals
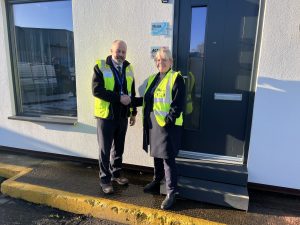
Kier Joint Ventures appointed to £10bn Offsite Construction Solutions framework
Kier, with Joint Venture (JV) partners, McAvoy and Metek has been appointed to all six Lots of Crown Commercial Services’ (CCS) new £10bn Offsite Construction Solutions (OCS) framework. The new framework replaces the existing modular building framework and will run for the next four years. Kier has created two unique JVs with external offsite manufacturing partners McAvoy and Metek, who are both experts in their method of construction, bringing high quality, innovative design, manufacturing and installation ability. The two JVs will allow Kier to deliver on every Lot in the OCS framework, which provides public sector organisations with all elements of offsite construction solutions, from design, fabrication, construction and installation, through to direct access to manufacturers. The OCS framework consists of six Lots. 3D Lots within the framework will be delivered by Kier McAvoy, and 2D Lots by Kier Metek. The Lots are: The appointment to the OCS framework builds on Kier’s award-winning cross-sector work in MMC and offsite construction, including HMP Five Wells prison, NHS Golden Jubilee surgical centre, Lewis Cubitt Square, as well as its innovative Choice Factory solution. Stuart Togwell, Group managing director at Kier Construction, said: “Building on the ambitions of the Construction Playbook of using MMC and offsite solutions to drive improvements is a core imperative for Kier, and securing a place on all Lots means we are well-placed to support the delivery of vital new infrastructure in the UK. “Our forward-thinking JVs with McAvoy and Metek will allow us to provide more capacity and high-quality end-to-end solutions for our public sector clients and to continue to deliver the best value through innovation across the wider industry.” Ron Clarke, CEO, McAvoy, from the Kier McAvoy consortium, said: “This is a significant milestone for McAvoy, and we are delighted to be combining our leading-edge, high-quality precision manufacturing capabilities with Kier’s scale and expertise. “We have been innovators and market leaders for more than 50 years. Our team is firmly focused on delivering consistently high-quality product and customer service across the UK and Ireland. “With significant experience of MMC we are very much focused on helping our clients meet their ESG goals. We look forward to working in partnership with Kier to deliver on that commitment within the OCS framework.” Oliver Rogan, managing director of Metek, from the Kier Metek consortium, said: “Winning this OCS framework has demonstrated the importance of working as a team. Metek and Kier have been working closely together for the past 12 months, driving a strategy to build projects in a more energy efficient and cost-effective manner, whilst maintaining the very highest health & safety standards. This ground-breaking collaboration unlocks Metek’s manufacturing and installation potential, whilst enabling us to grow, learn and develop alongside a formidable Kier team. “Here at Metek, we have been at the forefront of light steel framed Modern Methods of Construction for over 23 years. I feel that this new alliance is a game changer in terms of adding components to the manufacturing process. “Working with the Kier team on this bid has been inspiring and the whole Metek team are excited to be embarking on this journey and committed to delivering the key requirements of the agreement, whilst continuing to champion UK manufacturing.” Crown Commercial Service supports the public sector to achieve maximum commercial value when procuring common goods and services. In 2021/22, CCS helped the public sector to achieve commercial benefits equal to £2.8 billion – supporting world-class public services that offer best value for taxpayers. Building, Design & Construction Magazine | The Choice of Industry Professionals
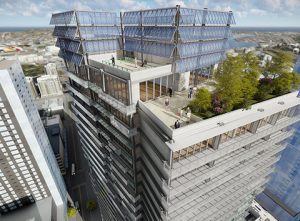
‘Modular Construction: Off-site and On Trend’
Supported as a route to more efficient and sustainable construction, modular construction is an evolving sector that offers the industry progressive benefits, says Daniel May of Consort Architectural Hardware. Recognised as an emerging model in modern methods of construction (MMC), modular construction is an industry on the rise, albeit one that’s still in its infancy. In broad terms, the concept is often described as the process of constructing a building in a controlled, off-site setting, before being transported and assembled at its intended destination. In 2019, modular construction was reported to be worth £753m in the UK market and was projected to grow by 14% between 2020 and 2024. Globally, the numbers are much higher, valued at $72 billion in 2020 and predicted to reach over $175 billion by 2025. Its growth – although slower in the UK – can be attributed to the needs of modern markets, where modular initiatives are praised for their ergonomic and environmental benefits, as it produces buildings at a more efficient rate and lower cost – and often with more sustainable materials. Efficient production At its core, modular construction shares many similarities to any construction project, where under controlled conditions, teams use the same materials and design to the same codes and standards as conventional developments. Yet, for many, modular construction provides answers to some of the industry’s most pressing issues. Britain’s housing crisis for example, is exacerbated by a shortage in homes, unaffordable rents and rising purchase prices, and coupled with modern carbon initiative targets, there’s a need to find a swift and sustainable solution. Currently, only 15,000 modular homes are built in the UK each year, despite modular construction presenting itself as a viable MMC. But, as experts suggest, the potential is far greater, and the production of over 75,000 modular homes is considered a fair target to aim for, with the Homes England programme now aiming to construct 25% of affordable homes using MMC. By manufacturing structural components off-site (at the same time groundworks and foundations are completed on-site), the process of modular construction can offer various sectors (such as residential housing) a more flexible and cost-effective option – not to mention, one that’s completed in a much quicker time than traditional methods. In fact, where the turnaround time of projects is concerned, building in an off-site setting is said to reduce construction times by up to 30%, with total development time halved. From a sustainability perspective, the quicker delivery of development projects is also contributing to the reduction of carbon emissions. With less time spent on site and less manufacturing machinery used, total pollution is moderated in pre-set factory environments. Already, UK studies have also found that up to a 90% reduction in materials can be achieved with modular building methods. And as more sustainably sourced materials are used to create better energy efficient buildings, construction’s green initiatives appear evermore achievable this way. Staying on track When it comes to the production of our built environment, the speed and sustainability benefits modular construction offers will continue to turn the heads of decision makers who recognise efficiency and cost-effectiveness. Yet, as the method continues to advance, those involved in the procurement of modular components and materials must continue to give considered thought to the supply, transportation and design process of projects to truly unlock its potentially progressive benefits. With a constant flow of components, from structural modules right through to hardware products, decision makers must continue to factor how building materials may interact with each other upon completion of projects. Where reliability and functionality are concerned, the specification of construction products is crucial and decision makers have a responsibility to ensure all materials and products are fit for purpose throughout the entirety of modular construction developments. The supply chain is often simplified for modular construction projects, and with various regulations to follow and an assortment of construction products to keep track of, the onus is on a smaller team of decision makers to make conscious choices that meet all of a project’s regulatory requirements. With this in mind, modern manufacturers and professional bodies are working to support professionals throughout the decision-making process. As part of the Building Safety Bill’s regulatory framework, the Golden Thread of Information has been developed to provide more complete and detailed product information in the form of comprehensive product datasheets and installation guides. The Golden Thread of Information encourages greater collaboration and education and can provide invaluable and transparent information on product performance and testing throughout the completion of modular projects. Enhanced traceability will lead to more informed and consistent product choices, and it is imperative decision makers remain informed if they aim to deliver complete and efficient buildings. If the acceptance of modular construction continues to ascend, we may shortly see a shift of landscape within the construction industry. The environmental and cost saving benefits are evident. But to effectively tap into the progressive benefits modular construction has to offer, the importance of specification must be widely understood. After all, safety, functionality and reliability will always remain unremitting themes in construction, regardless of method.
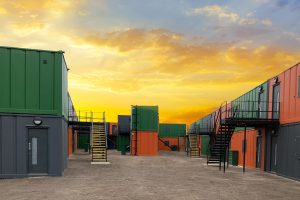
Integra Buildings named on £10bn Government framework to drive modular construction growth
Modular specialist Integra Buildings has been appointed onto a £10bn Government framework to drive investment in the offsite construction sector. Integra has been named as a supplier on the newly-launched Offsite Construction Solutions framework, which spans a variety of sectors including health, housing, education and defence. The framework, delivered by the Crown Commercial Service (CCS), will replace the existing £500m Modular Buildings Solutions framework in April. A total of 29 suppliers have been named on the new framework, which runs for four years, with the possibility of a three-year extension. It means Integra will be able to tender for major contracts with public sector clients across the UK. Gary Parker, Managing Director at Integra Buildings, said: “To be named on the new Offsite Construction Solutions framework is a huge vote of confidence in Integra and our proven capability to deliver major public sector projects to the very highest standards. “Since being appointed onto the old framework four years ago, we’ve delivered some of the biggest projects in our 25-year history. Integra continues to grow and evolve, with clients right across the UK. “The offsite and modular construction sector continues to expand at pace and being named on this framework ensures we’ll remain right at the forefront of that exciting journey.” The new Offsite Construction Solutions framework has an estimated total value of £10bn over at least the next four years. It is split up into six lots, each representing a different sector. Integra has been named in three lots – Built Estate Including Education, Justice and Defence – enabling the company to tender for major projects in these fields nationwide. Since joining the Modular Buildings Solutions framework in 2019, Integra has delivered a series of key projects for clients including Network Rail, the Environment Agency and the Department for Work and Pensions. Contracts completed under the previous framework include the construction of temporary housing for Reading Borough Council, a new job centre in Birmingham and modular units which were shipped to Cyprus for use by the Ministry of Defence. Integra designs and constructs buildings off-site in controlled conditions at its purpose-built factories in Paull, East Yorkshire, before delivering and installing them in situ, a process that reduces project timescales and minimises disruption to customers, with no compromise on quality. Integra is joined on the new framework by major suppliers including Portakabin, Wernick and Reds10. The Offsite Construction Solutions framework is delivered by the CCS, which supports the public sector to achieve maximum commercial value when procuring technology solutions. In 2021/22, the CCS helped the public sector achieve commercial benefits equal to £2.8 billion – supporting world-class public services that offer best value for taxpayers. John Welch, Deputy Director for Construction at the CCS, said: “This new framework will support the public sector in the design, delivery and commissioning of a whole range of offsite construction projects in the coming years, including social housing, new schools and hospital extensions. “These projects, and the many more which will come, have the potential to improve services and the lives of millions of people.” Integra has built a strong reputation over more than 25 years for its innovative, bespoke approach to modular construction, meaning it can match the design of a building to each client’s specific needs. Integra enjoyed a busy 2022 which saw it complete significant contracts including the delivery of new offices for Triumph Motorcycles at its site in Coventry, providing school buildings across the country, from Merseyside to Surrey, and forge an exciting new partnership with More Housing to supply modular accommodation units to combat homelessness across the UK. Building, Design & Construction Magazine | The Choice of Industry Professionals
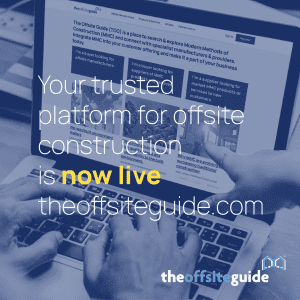
The Offsite Guide – A Revolutionary One-Stop Resource for Modern Methods of Construction (MMC)
Launched in January 2023 The Offsite Guide is the first B2B marketplace in the UK and Europe for MMC – a platform for businesses to explore options for using Modern Methods of Construction (MMC) and interact with specialist manufacturers. As a marketplace TOG facilitates engagement between key market participants and drives awareness of the many benefits of MMC including more efficient production, economies of scale and repeatability. In doing so it provides a central point of reference for product variety, availability, & pricing specification. Crucially, it provides a platform for direct communication between a wide range of providers and their potential customers in this fragmented market. “At The Offsite Guide we attract and facilitate early interaction with customers, allowing manufacturers of commercial and domestic modular buildings and offsite solutions to showcase a range of their products & help educate potential customers. We provide a trusted platform not only for showcasing offsite construction, but also to facilitate initial dialogue and ongoing interaction between customers, manufacturers and MMC suppliers.” Ingrid Orbie – Director For TOG Partners, listing MMC case studies & solutions on the Offsite Guide marketplace is a cost-effective method for manufacturers to bring in targeted traffic. Partners listings can easily be found under various search categories that can subtlety hand off and complement other marketing channels in the marketeer’s toolbox. Listing as a partner will also assist the partner company’s own website SEO ranking in an effective and cost-efficient way. For companies offering products and services complementary to MMC, creating an entry in the TOG Directory is an effective way to promote to the sector. These offsite system & product suppliers include companies offering panellised systems, sub-assemblies & components, as well as site based MMC structural components. This also includes offsite main contractors & other professionals including main & general contractors, offsite/modular solutions, offsite consultants & engineers, offsite designers, and digital designers and architects. A wider group of offsite trades people are also included in the Directory such as groundwork companies, electricians, carpenters, plumbers, landscape & external works contractors, flooring installers, painters & decorators, and all associated construction products like road signs, PPE, damage protection products, health & safety products. Whether listing as a TOG Partner on the marketplace or as Advertiser in the Directory, TOG offers an opportunity to raise brand awareness, increase a company’s visibility and gain access to new customers. Through TOG’s marketing and launch promotion campaigns TOG is striving to elevate MMC sales channels and engage with the market in a more efficient and effective way. Until now, there has been a lack of any resource for either private and commercial buyers to search & compare modular buildings and offsite solutions and engage directly with suppliers. The Offsite Guide provides this much needed resource in this fast-developing market. Online marketplaces are prevalent in many different B2B and B2C markets and are globally recognised as efficient methods of delivering fast, efficient and timely market interaction. By bringing proven marketplace technology to the MMC market TOG is strengthening the ecosystem of the MMC construction sector. Housing associations (HAs), developers, builders, self-builders, schools and universities, suppliers, central and local governments are all seeking more sustainable and efficient ways of construction. The TOG marketplace facilitates that search for proven solutions and gives examples and case studies that show ways that organisations and developers can break tradition and drive efficiency using MMC. Ultimately this is a wayto share information and experience, as well as to educate the market. To find out more and to benefit from TOG’s marketing expertise in the built environment and the construction sector go to www.theoffsiteguide.com. Partner and Advertiser eBooks can be downloaded from the site that give more detail of the services on offer. Building, Design & Construction Magazine | The Choice of Industry Professionals