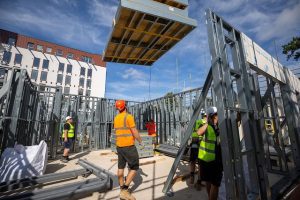
Adopt Off-Site Construction/MMC – Your Solution To Part L Compliance
Whilst large swathes of the UK construction industry continue to demonstrate a ‘head in the sand’ attitude by failing to adopt more performance and energy efficient ways of building, surely now it’s only a matter of time before they radically rethink things. Enter the recent changes to the all-important Part L of the building regulations. Having come into force in June of last year, the period for compliance is now firmly behind us, with the overall industry heading beyond what is an interim step to more stringent legislation that will come under the Future Homes Standards in 2025. Based against a background that provides a further uplift to existing energy efficient standards and carbon emissions for homes, the new regulations apply to anyone involved in designing, constructing or renovating buildings in England, including architects, builders, developers, engineers, and other building professionals. Whilst the latest Part L updates precede all new homes having to be produced with 75% – 80% fewer emissions from 2025, let’s first look at what is required to comply with the new measures, which include a mandate for new energy efficiency targets and alterations to assessment methodology. Part L Update – The Key Components Separated into four volumes to include new dwellings, existing dwellings, new buildings other than dwellings, and existing buildings other than dwellings, a fabric-first approach features strongly in the latest updates. This is not surprising given that this has long been considered a cost-effective way of saving carbon and delivering energy efficiency over the whole life of a building. Key considerations here centre on construction techniques that deliver maximising airtightness, optimising insulation and eliminating thermal bridging. Obviously using more energy-efficient walls, floors, windows and roofs can help reduce the dependence on secondary technologies and their associated energy costs. And what about all-important U-values? These are the main changes that need to be met under the Part L regulations: Who Will Be Impacted By The Changes? Obviously the new standards need to be considered from the very early design stages to ensure compliance. And whilst architects will need to work closely at overall building design efficiency, it is traditional builders that will feel the biggest force of the change through the need to adapt to newer energy-efficient designs, materials and construction methods. In essence, they must ensure that the building envelope is well insulated to reduce heat loss and minimise thermal bridging. This is likely to necessitate the use of thicker insulation materials and the introduction of more adequate airtightness measures, such as vapour barriers, tapes and sealants. As for other trades, then plumbers and HVAC technicians will be looking to install more efficient heating and ventilation systems and increase the use of renewable energy sources such as solar, thermal or heat pumps, whilst electricians will focus on more efficient lighting systems that minimise unnecessary energy use. They will also be increasingly involved in installing renewable energy sources such as PV panels and wind turbines. Other Key Compliant Considerations Whilst all elements of the regulations need consideration, understanding and planning that starts at the design stage, builders and developers also need to keep detailed records of the materials and systems used in construction, along with step-by-step photographic evidence. Failure to do so may result in potential rework, build delays, and possible financial penalties. The Solution Obviously reducing the carbon footprint and maximising the energy efficiency of any building is a task for everyone. So it will be imperative that those in the industry work collaboratively to ensure the necessary measures are implemented and complied with effectively. Indeed the overriding solution is not new! It’s not about reinventing the wheel but encouraging builders and contractors to adopt new ways and means of building using proven off-site and MMC system solutions such as those provided by the likes of Excel Group. Whilst many builders still see MMC and off-site building as purely timber frame, this couldn’t be further from the case. The focus should be on the specific needs of the project and this is where the Excel approach differentiates themselves in the marketplace. Standing as a specialist sub-contractor and having developed relationships with dedicated and sustainable supply chain partners across a range of component manufacturing disciplines, on offer is a range of off-site solutions (SIPs, timber frame, CLT and light gauge steel). After all, one size doesn’t fit all! In support of each solution, Excel has engaged software from industry specialists, FONN that captures all relevant details, dates and time steps making Part L assessment easier, while providing full transparency to the ERC assessor and end user. FONN also provides the opportunity for highly efficient project management workflows benefiting all project stakeholders. In addition, Excel Group operates a proven window and door business in partnership with leading global brands to offer a complete sustainable glazing solution – either stand alone or as part of an offsite structural package. Further expansion into SFS infill and external cladding systems has also facilitated the offer of bespoke packages for customers, developers and contractors to suit specific needs. So for any builders or contractors unsure, sceptical or lack the confidence and knowledge to embrace MMC and all that off-site construction has to offer, Excel can provide an initial system agnostic consultative discussion that serves to build trust on the basis that it is never going to be a single solution offering. Surely adopting building solutions that already exceed the requirements of Part L makes sense, as is the case with many of today’s off-site construction solutions? And for those who remain uncertain, then the further profound implications that Future Homes Standards of 2025 are set to bring, must be an eye-opener and catalyst to start considering other, more sustainable ways of doing things. Building, Design & Construction Magazine | The Choice of Industry Professionals
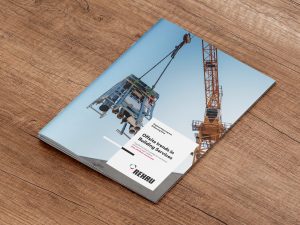
REHAU Report Shows How Offsite Construction Can Overcome Skyrocketing Demand on UK Building Industry
With pressure for major construction projects growing across the UK, a new report is encouraging mechanical services contractors, specifiers and developers to accelerate the uptake and deployment of offsite construction techniques, particularly when it comes to building services. The UK is currently falling short of its annual target to build 300,000 new homes in England[1], while 90% of student accommodation rooms for the 2023/24 academic year had already been sold by April 2023[2]. With a 17% increase in hotel construction projects also reported over 2024[3], pressure is on the construction sector to build faster as confidence in city centre building continues to rise.[4] REHAU’s new report, Offsite Trends in Building Services explores how modern methods of construction (MMC) can help tackle this issue. Underlining a skills shortage of 937,000 construction industry vacancies by 2032, it looks specifically at how to implement mechanical service installation into offsite projects to make builds easier and faster.[5] Steve Richmond, Head of Marketing and Technical, REHAU Building Solutions, said: “Building at pace within tight footprints and using traditional methods is undoubtedly difficult, necessitating new approaches such as MMC. This new report details what is possible and how different offsite methods suit specific projects and help provide simpler, faster and high-quality builds for contractors, all within a factory-controlled environment.” With high-rise construction increasingly necessary in high-density urban areas, REHAU’s guide highlights how the company can help with the challenge of building at height in smaller spaces. At the same time, it uncovers obstacles that contractors, specifiers and developers must overcome when using offsite construction methods to ensure quality work. The guide includes information on key components that can be assembled at the factory and transported and assembled onsite for a high-quality build. This includes modular shafts, pre-wall constructions, bathroom pods and polymer risers, as well as relatively new technologies such as thermally activated building structures (TABS), which can provide both heating and cooling. “There have already been many exciting innovations across the globe to further improve offsite construction methods that we have included within this new guide,” Steve concludes. “Like all fields, MMC is continually developing, and the hope is that through this whitepaper, readers can find out more about these innovative methods and solutions, and best put MMC techniques into practice to meet market demand.” To download REHAU’s report, ‘Offsite Trends for Building Services’, CLICK HERE. Building, Design & Construction Magazine | The Choice of Industry Professionals
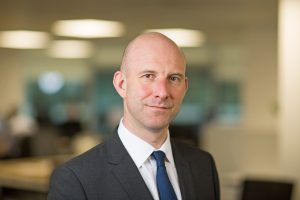
Industry survey provides insight to experience and challenge of MMC Projects
PRESSURE on public sector buildings has been dominating the news over the past six months, with a report analysing whether modern methods of construction (MMC) are helping or hindering projects reach successful outcomes. In a survey conducted by leading independent property, construction, and infrastructure consultancy Pick Everard, key questions were put to its multi-disciplinary connections including clients, consultants and contractors around their experiences with MMC. The uptake of such practices is clear, with 85% of those surveyed having actively used a modern method as part of a project, and 80% also expecting to see utilisation to increase over the next five years. Highlights of the Q4 Market Intelligence Report also revealed the potential impact of the new Building Safety Act Gateway 2, which came into effect in October 2023. 80% of contractors have reported they see it as either ‘affecting’ or ‘maybe affecting’ programmes and procurement for MMC builds. Kieran Bradley, director at Pick Everard, said: “By giving a voice to the construction industry through this survey, we have been able to supply insight around how MMC is viewed directly from those actually utilising such methods. It’s clear there are huge benefits particularly when addressing the challenges of the public sector, such as overcrowded prisons and aging schools and other public buildings that have become structurally unsafe due to RAAC – but is it always the right option? “An interesting breakdown in the results relates to improvement in the quality of buildings using MMC. There is a marked different between the views of contractors, with 92% citing an overall improvement, compared with a lower figure for consultants (72%) and clients (67%).” “This may be attributable to these parties’ specific roles in delivering projects. In some instances, MMC can prove to be too complicated, or the site might just be too small to use cranes. In other cases, it can be down to the actual scheme. Add to this the need to pay an upfront fee and immediate design approvals puts many at a significant disadvantage if changes need to be made later on.” In addition, the report also explores the ongoing inflation and interest rate situation and the impact on the construction sector regarding demand for work, wages and skills shortages. Gavin Mason, director at Pick Everard, said: “Despite the figures falling, we are also still facing high inflation rates, which is only adding to the pressure for our public sector clients and how we respond to that from our industry. The government has pledged to halve inflation by the end of the year, from when it peaked at more than 11% at the end of 2022. While there is promising movement in some regions, nationally demand is still in decline. “From our construction survey, we predict construction inflation will slow to a rate of 2.5% per annum, based on current demand in the property sector for new work and an assessment of capacity within the industry. When asked about what the biggest contribution to inflation has been, we found the majority (45%) of participants believe wage inflation has been the main factor. We can therefore see where part of the challenge lies when looking at the labour gap, with a shortage of around 45,000 skilled workers according to the, which we believe vocational training is essential in combatting.” Factoring this in when looking at the potential for MMC is potentially where some of the results came from regarding the downsides to its utilisation. In addition to the increased upfront costs (32%), and programming issues (24%), the market research has found that future flexibility and design change (31%) to be the biggest challenges of using MMC. Interestingly, design compliance (13%) and quality of the finished article (0%) weren’t seen as so challenging (graph 3). However, the report also aims to look ahead to how MMC could be improved, and more opportunities revealed for the sector to make the most of its advantages. Kieran added: “When we asked people what one change to MMC would improve its uptake, three key themes were returned; education, early integration and flexibility. Enhancing a more rounded understanding of the process and the appropriate use for MMC was a view held by the majority of respondents and one that we echo. “Supporting the sector through knowledge sharing, such as this report, is integral to our goals of a collaborated approach and supporting the sector through the next quarter and throughout 2024. We feel positive inflation rates will level out over the course of the next year, and hopefully bring back more investment and opportunity for our industry.” Pick Everard employs more than 650 staff across its 15 offices, providing a range of project, cost, and design consultancy services. To read the Q4 2023 Market Intelligence Report in full, visit https://landing.pickeverard.co.uk/Downloads/Pick-Everard-Q4-2023-Market-Intelligence.pdf Further details on Pick Everard can be found at: http://www.pickeverard.co.uk Building, Design & Construction Magazine | The Choice of Industry Professionals
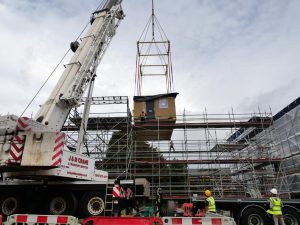
New modular homes for Maidstone
Golding Homes’ Somerfield Terrace development in Maidstone has seen the arrival of its cutting-edge, factory built “fully modular” homes. The houses were manufactured in three parts by leading fully modular developer TopHat at their Derbyshire factory, fully fitted with kitchens and bathrooms, then transported to Maidstone, lifted into position by crane and bolted together to create new homes. The six four-bedroom houses will be available for shared ownership and market rent customers in 2024.Modern methods of construction – and fully modular in particular – are a more efficient and sustainable way of building homes, with lower carbon emissions to build and more energy efficient to run. The Somerfield Terrace site dates back to 1850 and was formerly a private and military hospital. The site includes four blocks of Grade II listed semi-detached villas which have been converted, with some of the original features being preserved. Once complete, the development will consist of 73 homes – including flats and houses – for market rent, shared ownership, social rent and discount market sale. Executive Director of Development at Golding Homes, Tom Casey, said: “Somerfield Terrace is an exciting development with both Grade II listed buildings and ultra-modern homes side by side, bringing a unique housing offer to the county town. “Using modern methods of construction is part of our commitment to providing homes that are both sustainable and affordable. This is the first time we’ve used modular homes at one of our developments in Maidstone, so seeing them arrive here on site is a significant milestone that we’re really proud of.”Jordan Rosenhaus, CEO and Founder of TopHat said: “We are delighted to see our beautifully designed, precision engineered new homes arrive on site in Maidstone. “There’s increasing awareness of the benefits of modern factory-built homes – from the lower carbon to build and run, through to quicker, quieter building sites – so it’s great to work with Golding Homes and to be bringing this to life in Maidstone.” Building, Design & Construction Magazine | The Choice of Industry Professionals
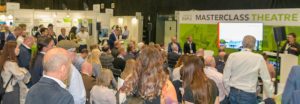
Offsite Expo: Supporting Building Safety Standards
Coming in the wake of the Hackitt review, receiving Royal Assent in April 2022, the Building Safety Act covers a raft of changes for housebuilders and developers. These include a new system of accountability for safety in projects, a construction products regulator and a refreshed regulatory framework. It is claimed to be the biggest change in building safety for over 40 years. More than a year on, with many key aspects of the act now in force, industry professionals are still grappling with the implications to ensure their operations and developments are compliant. Providing an opportunity to get to grips with the latest information and achieving building safety standards through modern methods of construction, Offsite Expo 2023, being held at the Coventry Building Society Arena on 19 and 20 September – is the place to go to hear direct from industry experts about achieving safe and compliant buildings. Offsite Masterclasses Chaired by Tom Mason, Director of Fire Safety Engineering at Kiwa Fire Safety Compliance – the CPD accredited Fire Protection Masterclass will shine a spotlight on building safety. David Fitzpatrick, Head of SFS, will focus on the impact of ‘the new Building Safety Act on Smoke Control Systems.’ SFS is a division of Extye Hargreaves which delivers complex engineering projects including HVAC and full mechanical and electrical systems, associated structural steelwork and civil engineering. David has worked within the building services industry for 35 years and has been a member of CIBSE for over 25 years and has had two periods on the CIBSE board. Passive fire protection specialist FSi, will be using the Fire Protection Masterclass as a platform to highlight the benefits that offsite construction can bring in the efficient installation of cavity barriers to help protect buildings in the event of a blaze breaking out. With the recent announcement that the government’s cladding safety scheme is to be expanded, fire protection measures continue to be a major consideration in all aspects of construction. Liam Blears on behalf of FSi will discuss how ‘Forward Planning is Key to Ensure Correct Sequencing in Offsite Construction’ and also how the controlled environment used to create modules supports excellence in cavity barrier installation, including the ability to carry out on-site checks. Presenting ‘The New Fire Safety Regulations and the Benefit of Offsite Construction’ – Nichola Harrison is passionate about health and safety. Assistant Director – Facilities, Fleet and H&S at Paradigm Housing Group, Nichola has had great success leading organisations in creating healthier and safer environments and improving their safety culture by making use of her diverse background in medium to high risk organisations. In the Structural Timber Masterclass, Julie Bregulla Strategic Advisor for high profile organisations such as Swedish Wood, Structural Timber Association and Timber Development UK – will introduce ‘The Timber Fire Safety Platform.’ Previously Executive Director of the Building Research Establishment – Fire and Building Technology Group, Julie has over 20 years’ experience working in academia, consulting and construction. She has been active in research, testing and certification of construction products and systems, including timber. ‘Fire Safety in Building in Cavities’ will be presented by Craig Fyall, Category Director – Walling for Permavent in the Facades & Fenestration Masterclass. Craig has over 20 years of extensive experience in roofing and construction membranes and building structure fire safety. In 2012 Craig led the design team in the specification and detailing of the first Passivhaus 56-bedroom care home in the UK. Curated by Leading Offsite Experts The masterclasses at Offsite Expo will provide a comprehensive and balanced perspective from a host of renowned experts. Delegates will experience an interactive learning environment which will actively encourage engagement with the key themes. One of the reasons Offsite Expo has experienced incremental growth year-on-year is the quality of the speaker programme. Helping the development of new skills and specialisms and a central part of the Offsite Expo experience – with over 80 confirmed distinguished speakers, Offsite Masterclasses and Spotlight on Offsite Sessions are the place to gain insights, learn from the best and meet experts offering in-depth analysis and technical know-how in an extensive range of CPD-accredited sessions – all free of charge. For the full seminar programme visit: www.offsite-expo.co.uk/masterclasses Register To Attend Offsite construction is changing the norms for contractors, developers, architects, engineers and specifiers. There is an urgent need for construction professionals to get to grips with the latest industry innovations and building safety regulations. Offsite Expo is the place to go to take a deep dive into the emerging trends that are making the building process safer, faster and more sustainable to reach net zero goals. With the government mandating 70% pre-manufactured value (PMV) in all public sector projects and developers recognising the safety, quality and predictability benefits – offsite technology is becoming an increasingly dominant force in the world of building safety and construction. Offsite Expo will be taking place at the Coventry Building Society Arena on 19 and 20 September 2023. Entry to the exhibition, CPD Accredited Explore Offsite Masterclasses and Spotlight on Offsite Panel Discussions – are free of charge. To book tickets go to: www.offsite-expo.co.uk/book Building, Design & Construction Magazine | The Choice of Industry Professionals
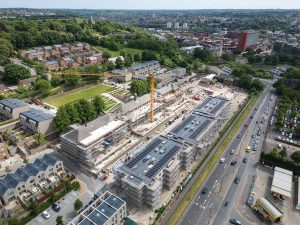
O’Keefe prepares the ground for pioneering modular development
O’Keefe is carrying out the second phase of groundworks and infrastructure works for a new residential development by modular off-site specialist TopHat. Although located on the site of the historic Kitchener Barracks in Kent, the apartments themselves are precision-engineered at TopHat’ s factory in Derbyshire and delivered to site ready for installation. The project is part of a larger scheme that will see TopHat deliver almost 300 new homes over three phases on the 4.8-acre Kitchener Barracks site. O’Keefe is the groundworks contractor on the current second phase, which started with enabling works in January 2022 followed by the main works package in March 2022. The company was principal contractor on the first phase of the scheme, completed in early 2021. The site knowledge gained by the team on that phase has assisted greatly when dealing with the construction element of the phase two works. “We have worked with TopHat previously on other schemes so there is a positive relationship between TopHat and O’Keefe,” says O’Keefe project manager Daniel Gough. The Kitchener Barracks project involves the construction of three four-storey blocks of modular apartments which will comprise 96 one- and two-bedroom homes. On this phase, some 240 modular sections were assembled on site and cassette corridor sections were then installed at the upper levels between the rows of apartments. O’Keefe’s role includes part-construction of foundations, drainage and services for the modular apartments, plus access roads and external finishings. Although the apartment modules are manufactured off-site, they still require foundations and services to be built in-situ. The foundations are mass concrete strip footings bedded a minimum 200mm into the underlying chalk strata. One of the biggest challenges for O’Keefe has been to ensure the on-site works perfectly align with the factory-built modules. Working to exacting tolerances, O’Keefe has formed upstands to receive the prefabricated modular units. “Co-ordination is vital when off site manufacturing and site build foundations are carried out,” says Daniel Gough. “It is essential that precise as-built surveys are carried out to ensure that the position and levels are within the specified tolerance and any drainage pipes are located correctly.” O’Keefe formed the drainage connections prior to the modular sections being installed. Service entries were taken into the plantrooms situated in the two stair cores and then distributed to the modular units. Reinforced concrete upstands and slabs were constructed within the two cores and the end escape stairs and a reinforced concrete in-situ lift core constructed to each of the cores, with a steel framework installed prior to installation of the modules. O’Keefe’s contract has also involved construction of a reinforced concrete (RC) frame extension off the back of the existing Khartoum Building, dating from the 1930s. The RC frame comprises a lower ground floor/basement level for parking, including electrical vehicle charging bays, with a ground level transfer slab above. This forms part extension for housing apartments and part outdoor terrace. A particular challenge here was the interface between the existing Khartoum Building and the new RC frame. “The existing building was originally cut to demolish the western side some years ago – this was carried out and surveyed in a method to assist with best coordinating the design of the new RC frame with the remaining building elements,” explains Daniel. “The complex design has been a continuous, coordinated process assisted by O’Keefe, the consultant engineers, architects and TopHat, to ensure that further survey work was carried out to slabs, roofs, cavities and foundations for the structural frame to have its final design. “Underpinning was carried out on the building in the early stages of the project and then the installation and cutting back completed after the concrete had cured. “TopHat and O’Keefe have worked together throughout the RC frame element of the works to monitor progress and provide live survey data to the consultant engineers and architects to assist with overcoming any issues encountered during the RC frame build,” says Daniel. Andrew Shepherd, managing director of TopHat Solutions said: “TopHat have worked closely with O’Keefe on this complex and ground breaking project. It was essential that we had a partner that was able to address a number of different challenges from foundations for an innovative modular project through to a concrete frame that would tie into an existing heritage building. This ongoing relationship has been formed on a process of innovation and continuous improvement, which underpins our joint approach to future projects.” Building, Design & Construction Magazine | The Choice of Industry Professionals